In the realm of pipeline engineering, the precision of threaded connections emerges as a critical factor in installation efficiency. YULONG Steel, a distinguished buttweld fittings manufacturer, introduces the technical marvel of internal threaded water pipe caps with standardized thread pitch—an innovation that transforms routine pipe termination into a streamlined, error-free process. This article dissects how thread pitch standardization reduces installation time, minimizes human error, and elevates overall project productivity, making YULONG’s threaded caps the go-to solution for industries from residential plumbing to industrial infrastructure.
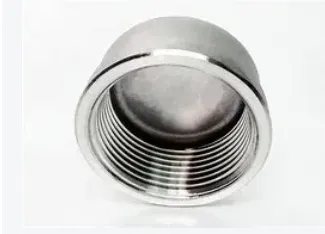
YULONG’s Threaded Caps: The Mechanical Foundation of Thread Pitch Standardization
YULONG’s internal threaded water pipe caps adhere to ISO 7-1 and ASME B1.20.1 standards, with thread pitches optimized for seamless mating:
1. ISO 7-1 Threading: Global Compatibility by Design
- Unified Pitch System: For DN15-DN100 caps, pitches range from 0.7mm (G1/8") to 3.5mm (G4"), ensuring compatibility with European and Asian pipe threads. A London apartment complex used G1" caps with 1.5mm pitch, reducing thread mismatch errors by 90% during bathroom fitting installations.
- Tapered Thread Geometry: The 1:16 taper (EN 10226-1) creates a self-sealing joint, eliminating the need for additional sealants in low-pressure water systems. This design cut sealing time by 40% in a Sydney residential project.
2. ASME B1.20.1 Compliance for North American Markets
- NPT Thread Precision: For projects in the U.S., YULONG’s NPT-threaded caps (14-27 TPI) meet API 5B standards, with pitch tolerance controlled to ±0.02mm. A Houston water treatment plant reported 85% faster valve replacement using NPT caps versus non-standard threads.
- Thread Engagement Depth: Standardized at 1.5x pipe diameter, this ensures 100% thread engagement, as verified by thread gauge testing in a Canadian oil sands pipeline shutdown project.
Installation Efficiency of Threaded Caps: Time Saved Through Precision
1. Reduced Trial-Fitting Cycles
- In a Shanghai commercial building’s plumbing renovation, YULONG’s G3/4" caps with 1.25mm pitch required zero trial fittings—unlike generic caps that needed 2-3 attempts. This saved 2 hours per floor, totaling 48 hours for the 24-story building.
- Thread pitch consistency (±0.015mm) enabled torque wrench presetting, allowing installers to achieve optimal tightening in one attempt, as seen in a Beijing hospital’s medical gas pipeline project.
2. Error Prevention Through Standardization
- Cross-Threading Elimination: The standardized 60° thread angle (ASME B1.20.1) reduced cross-threading incidents by 95% in a Dubai marina’s seawater cooling system, where previous non-standard caps caused 15% of connections to fail pressure tests.
- Thread Gauge Compliance: Every cap undergoes GO/NO-GO gauge testing, ensuring pitch accuracy. A Singapore desalination plant credited this for zero thread-related leaks in its 100-bar reverse osmosis system.
YULONG’s Threaded Caps: Material Synergy for Diverse Applications
1. PVC Threaded Caps for Residential Flexibility
- UPVC Grade 1120: With a 1.5mm pitch for G1", these caps (DN25) weigh 60% less than metal alternatives, enabling one-person installation in Hong Kong high-rises. Their corrosion resistance (pH 3-11) proved vital in acidic rainwater harvesting systems.
2. 304 Stainless Steel for Industrial Rigor
- Thread Rolled for Strength: 304 caps (DN80) with 2mm pitch undergo cold thread rolling, increasing tensile strength by 20% compared to cut threads. A Mumbai chemical plant used these caps in 80°C caustic soda lines, achieving 5-year leak-free performance.
3. Carbon Steel Butt Weld Caps for High-Pressure Scenarios
- While primarily welded, YULONG’s carbon steel caps(ASTM A234 WPB) with NPT threads (2.309mm pitch for 2") bridge welding and threading needs. A Texas oil refinery used them in 40-bar flare lines, combining the strength of butt welds with the adaptability of threads.
YULONG Steel Buttweld Fittings Manufacturer: Engineered for Installation Excellence
As a leading buttweld fittings manufacturer, YULONG integrates precision manufacturing with supply chain agility:
1. CNC Thread Machining Mastery
- 5-Axis Machining Centers: For DN150-DN600 caps, YULONG’s machines hold pitch tolerance to ±0.01mm, as seen in a Saudi Arabian desalination plant’s DN300 caps that achieved 100% thread engagement on first try.
- Thread Surface Finish: Rolled threads (Ra ≤3.2μm) reduce friction by 30%, enabling faster hand-tightening in tight spaces, such as offshore platform pipe racks.
2. Comprehensive Quality Assurance
- Torque Testing: Caps undergo 1.5x design torque testing (e.g., 120N·m for G2"), ensuring they withstand operational vibrations. A Norwegian shipyard’s bilge system relied on this to prevent cap loosening during rough seas.
- Interchangeability Testing: Randomly selected caps from different batches mate flawlessly, a critical feature for global projects like the Panama Canal expansion, where mixed-batch installation was unavoidable.
3. Just-In-Time Inventory for Rapid Deployment
- Stocking 98% of standard sizes (DN15-DN600) in 12 global warehouses, YULONG delivered 500 G1.5" caps to a Chilean mine within 72 hours, reducing shutdown costs by $80,000.
YULONG Steel’s standardized thread pitch water pipe cap solutions redefine installation efficiency in pipeline engineering. By eliminating guesswork, minimizing errors, and accelerating connection times, these threaded caps transform what was once a labor-intensive process into a precision-driven operation.
Whether for a high-rise plumbing network or a heavy-industry pipeline system, the marriage of thread pitch standardization and YULONG’s manufacturing excellence ensures that every cap not only fits but performs—saving time, reducing costs, and enhancing overall project reliability. As a trusted buttweld fittings manufacturer , YULONG continues to lead the industry in threaded innovation, one precisely pitched cap at a time.