In the intricate world of manufacturing, tube factories hold a pivotal role. As a linchpin in industries ranging from automotive to construction, these factories not only shape materials but also the future of innovation. Engaging with the experience, expertise, authoritativeness, and trustworthiness of tube manufacturing can foster a deeper understanding of its phenomenal impact.
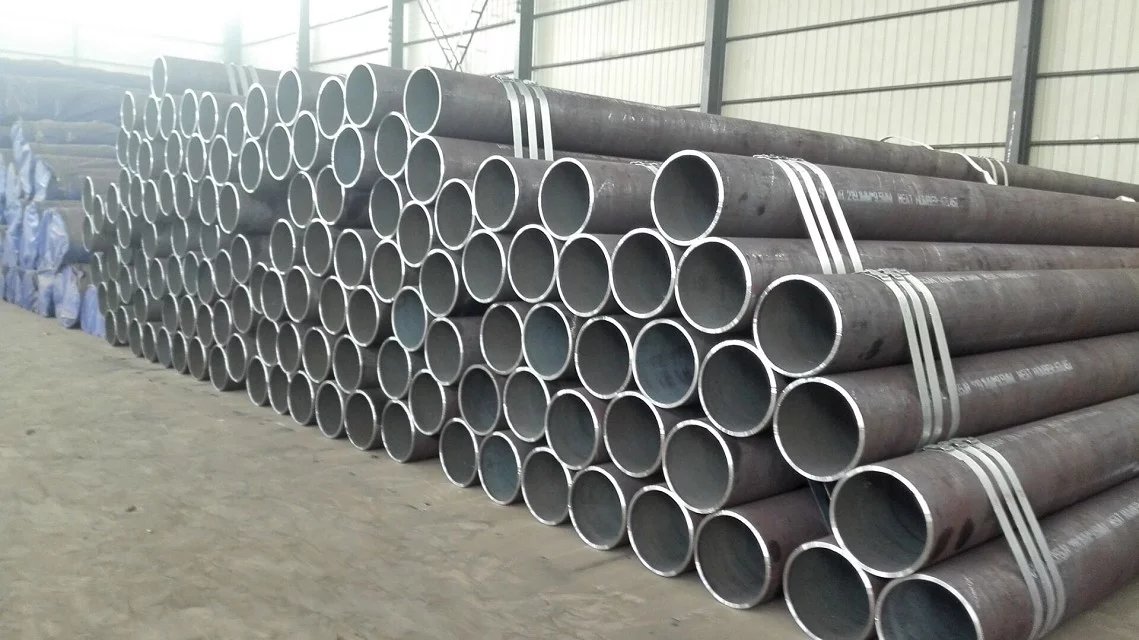
A tube factory is not just a manufacturing site; it is a cutting-edge facility where precision and technology meet innovation. The journey of a tube begins with raw materials that are meticulously selected for quality and suitability. This phase is critical—each type of tube, be it steel, aluminum, or copper, serves a unique purpose and requires specific characteristics to perform effectively in its designated application.
Consider the steel tube, a staple in automotive industries. Its strength and ability to withstand high pressure make it ideal for engine parts and suspension systems. A tube factory specializing in steel tubes employs high-frequency induction welding. This advanced technique involves heating the steel edges seamlessly to create a strong bond, ensuring durability and reliability. The expertise required for this process underscores the critical need for skilled professionals who understand both the material properties and the intricacies of modern welding technology.
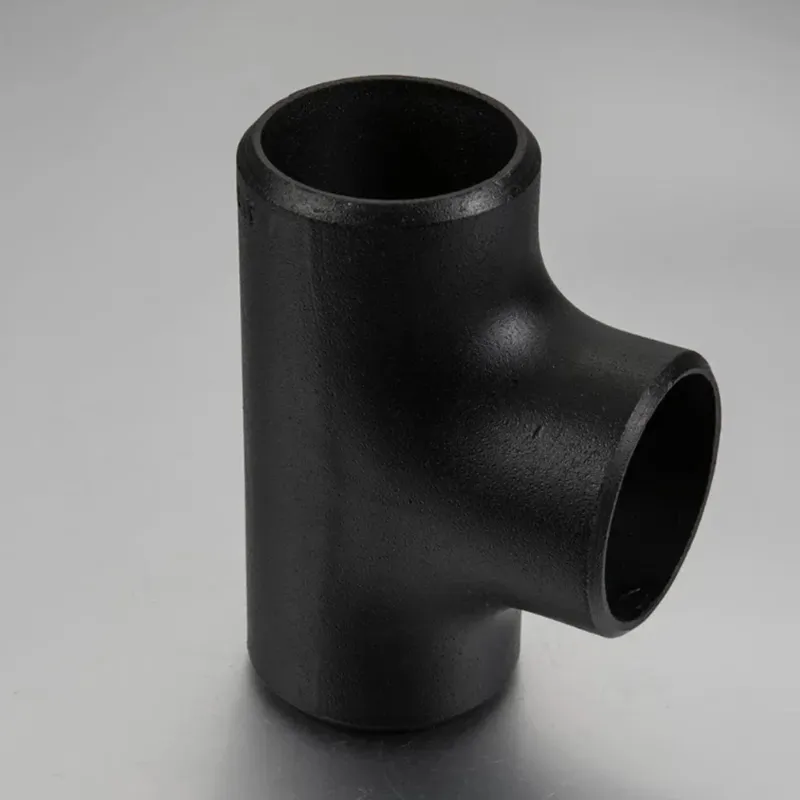
The journey within a tube factory is marked by a sophisticated production line. Expertise shines through in the numerous stages of production, each demanding precision and care. These stages include cutting, shaping, and treating the tubes through processes such as annealing—a heat treatment that alters the microstructure to reduce hardness and increase ductility. This specific treatment is essential for tubes that need to be bent or shaped without breaking, enhancing their versatility and expanding their use in various industries.
In building trust and credibility, a tube factory relies heavily on consistent quality control and adherence to international standards. Each tube produced is subjected to rigorous testing, including pressure tests, stress tests, and non-destructive examinations. These tests are not just mere formalities; they are vital in ensuring that every tube meets stringent safety and performance criteria. Customers trust tube factories that can demonstrate a flawless track record of compliance with ISO certifications and other global benchmarks. This authoritativeness in quality assurance elevates a factory's reputation and fosters long-term partnerships.
tube factory
In today's market, sustainability and environmental responsibility are cornerstones of trustworthiness. The modern tube factory is an exemplar of eco-friendly manufacturing practices. By implementing recycling programs and using energy-efficient machinery, these factories reduce waste and carbon emissions. Initiatives such as closed-loop water systems for cooling processes and implementing solar power are not only beneficial for the environment but also enhance the factory's standing as a forward-thinking and responsible entity.
Customer experience is another pillar that cannot be overlooked. Engaging directly with clients, understanding their specific needs, and offering customized solutions are critical components of a successful tube factory. This involves working closely with clients, from the design phase through to production, ensuring that the tubes manufactured align perfectly with their operational needs. This personalized approach not only meets customer expectations but often exceeds them, building a relationship of trust and reliability.
A well-rounded tube factory is as much about the people as it is about the technology. Continuous training and development of the workforce ensure that the factory remains at the forefront of innovation. Investing in employee expertise not only enhances production capabilities but also contributes to a culture of excellence and motivation within the workforce.
Moreover, embracing digital transformation through Industry 4.
0 technologies is reshaping the future of tube factories. Implementing smart manufacturing systems enhances efficiency and precision while predictive maintenance algorithms reduce downtime, further optimizing productivity.
In conclusion, a tube factory is a beacon of industrial prowess. The successful operation of such a complex entity requires a blend of experience, specialized knowledge, authority in production standards, and a solid foundation of trustworthiness through ethical practices. As these factories continue to evolve, their impact resonates across various sectors, driving both economic growth and technological advancement. Understanding these dynamics offers not only a glimpse into the world of manufacturing but also an appreciation for the skill and dedication that powers this essential industry.