Welded steel pipe, a crucial component in modern infrastructure, is a testament to the advancements in metallurgy and engineering. These pipes are fabricated by joining individual steel plates or strips through a welding process, resulting in a seamless and durable conduit that can withstand high pressures and temperatures.
The manufacturing of welded steel pipes involves several stages. Initially, a coil of steel sheet is unrolled and cut into specific widths. These strips then undergo an edge-forming process to ensure proper alignment before being shaped into a circular form. The edges are heated and pressed together using high-frequency electric currents, creating a strong weld that is often stronger than the base metal itself. This method, known as electric resistance welding (ERW), ensures the integrity of the pipe.
Once the initial seam is made, the pipe undergoes further shaping and sizing to meet the precise dimensions required for its intended use. It is then heat-treated to refine its mechanical properties and alleviate internal stresses developed during the forming process. After cooling, the exterior of the pipe is coated with an anti-corrosive material to protect against environmental factors such as moisture and chemicals.
One of the significant advantages of welded steel pipes is their adaptability
One of the significant advantages of welded steel pipes is their adaptability
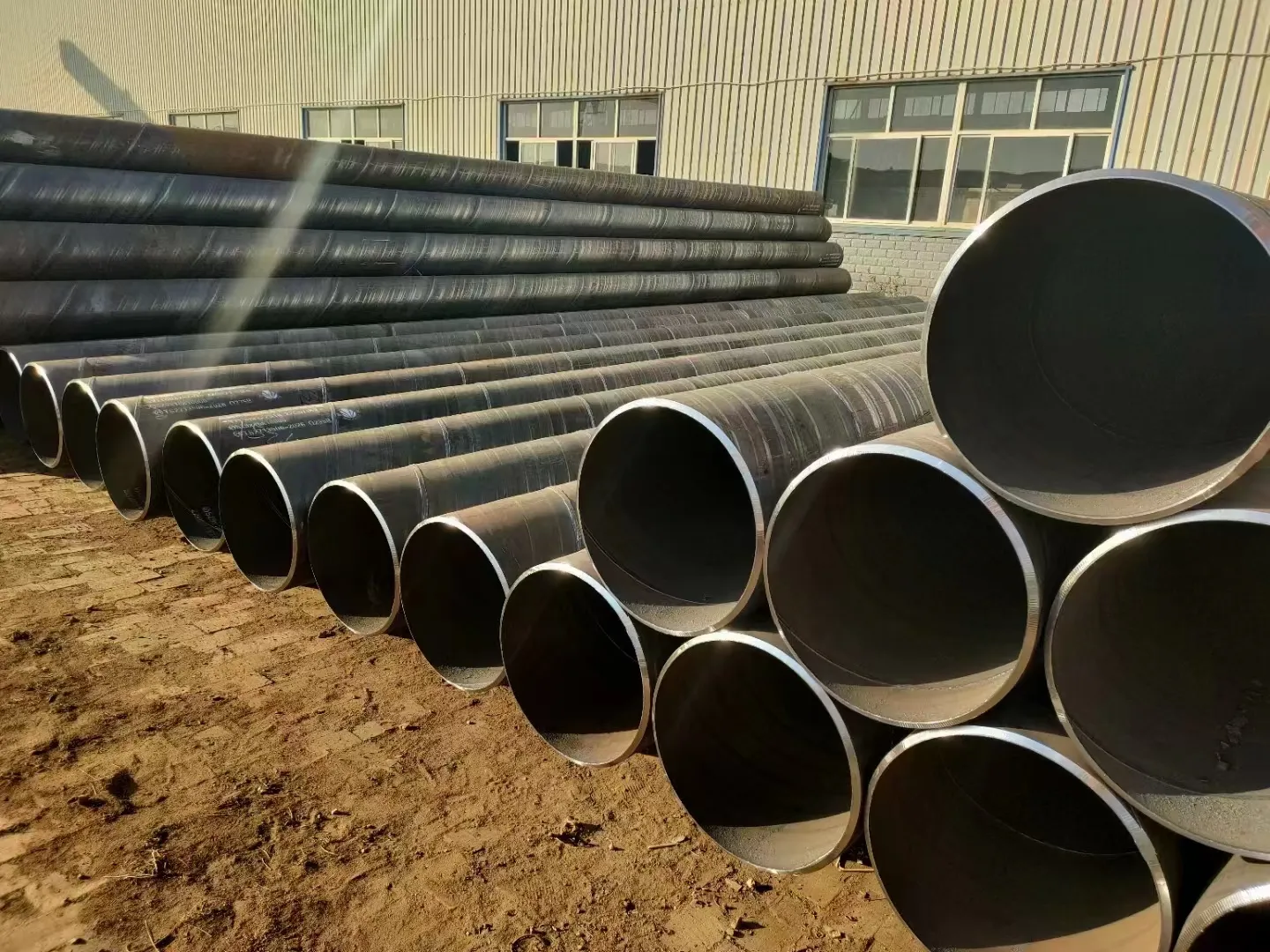
One of the significant advantages of welded steel pipes is their adaptability
One of the significant advantages of welded steel pipes is their adaptability
welded steel pipe. They come in various diameters and wall thicknesses, making them suitable for a range of applications including oil and gas pipelines, water supply systems, and sewage networks. Their durability and strength make them ideal for underground installations where they must resist soil movement and corrosive elements.
In the construction industry, welded steel pipes serve as piles for foundations, offering superior load-bearing capacity. They also play a vital role in the transportation sector, where they are used to build robust scaffolding and support structures for bridges and overpasses.
Despite their many benefits, welded steel pipes require rigorous quality control measures during production to ensure they meet safety standards. Non-destructive testing methods like ultrasonic and X-ray inspections are employed to detect any flaws in the welds or the metal itself.
In conclusion, welded steel pipes are an essential part of our built environment, providing reliable and efficient solutions for transporting fluids and supporting structures. Their strength, flexibility, and durability have made them indispensable in numerous industries worldwide, ensuring that they will continue to be a cornerstone of modern engineering for years to come.