Industrial pipe welding is a crucial process in various industries such as oil and gas, manufacturing, and construction. It involves joining two pieces of metal pipes together using a range of welding techniques. The quality and efficiency of the welding work are essential for ensuring the structural integrity and safety of the pipelines.
One of the most common welding techniques used in industrial pipe welding is shielded metal arc welding (SMAW), also known as stick welding. This method uses a flux-coated electrode rod that melts and forms the weld seam between the two pipes. SMAW is a versatile method that can be used for welding pipes of various sizes and materials, making it popular in the industry.
Another popular welding technique for industrial pipe welding is gas tungsten arc welding (GTAW), also known as Tungsten inert gas (TIG) welding. GTAW uses a non-consumable tungsten electrode and a separate filler material to create the weld seam. This method is known for its high precision, cleanliness, and ability to weld pipes made of metals such as stainless steel, aluminum, and titanium.
Furthermore, gas metal arc welding (GMAW), also known as MIG/MAG welding, is commonly used in industrial pipe welding for its efficiency and speed. GMAW uses a continuously fed wire electrode and a shielding gas to create the weld seam. This method is suitable for welding pipes of various thicknesses and allows for high productivity in large-scale welding projects This method is suitable for welding pipes of various thicknesses and allows for high productivity in large-scale welding projects
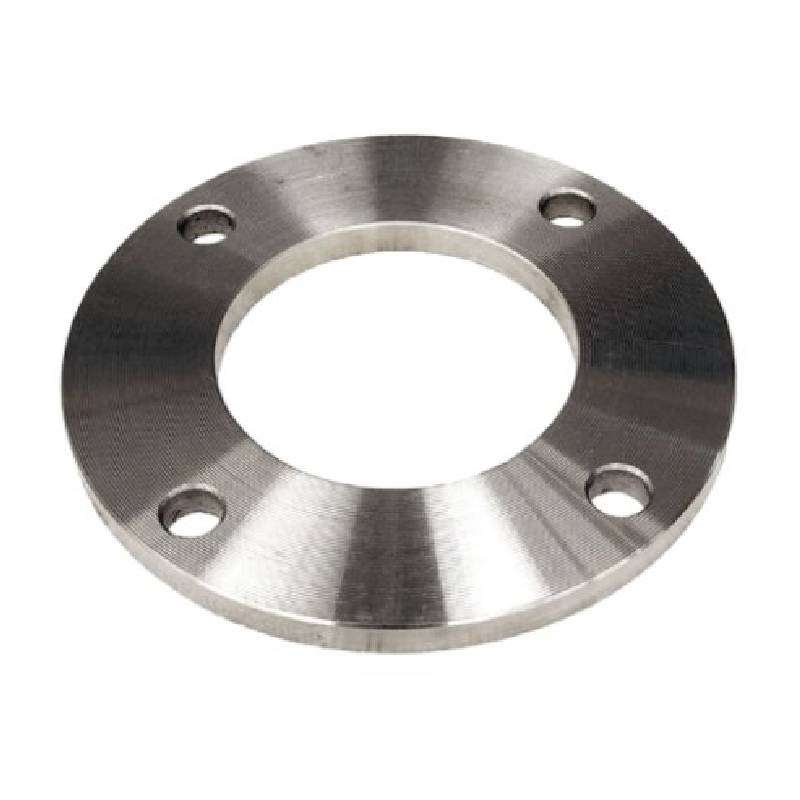
This method is suitable for welding pipes of various thicknesses and allows for high productivity in large-scale welding projects This method is suitable for welding pipes of various thicknesses and allows for high productivity in large-scale welding projects
industrial pipe welding.
In addition to the welding techniques mentioned above, there are various other specialized welding methods used in industrial pipe welding, such as flux-cored arc welding (FCAW), submerged arc welding (SAW), and pipe orbital welding. Each method has its advantages and is chosen based on the specific requirements of the project.
Quality control is a critical aspect of industrial pipe welding to ensure that the weld seams meet the required standards and specifications. Non-destructive testing methods such as visual inspection, radiographic testing, ultrasonic testing, and magnetic particle inspection are used to detect any defects or imperfections in the weld seams.
Proper training and certification of welders are essential for ensuring the quality and safety of industrial pipe welding. Welders must be familiar with the welding procedures, techniques, and equipment used in pipe welding. They must also follow safety protocols and regulations to prevent accidents and ensure a high standard of workmanship.
In conclusion, industrial pipe welding plays a vital role in the construction and maintenance of pipelines in various industries. The use of advanced welding techniques, quality control measures, and skilled welders are essential for ensuring the integrity and durability of pipe welds. By following best practices and standards in industrial pipe welding, companies can ensure the safety and reliability of their pipelines for years to come.