Welding round pipes effectively requires not only a good understanding of the materials but also precision and expertise. This intricate process, often seen in industries ranging from construction to automotive, involves joining round sections of metal to create sturdy, reliable structures. The challenge of welding round pipes is compounded by their shape, which can cause complications such as inconsistent heat distribution and difficulty in achieving uniform welds.
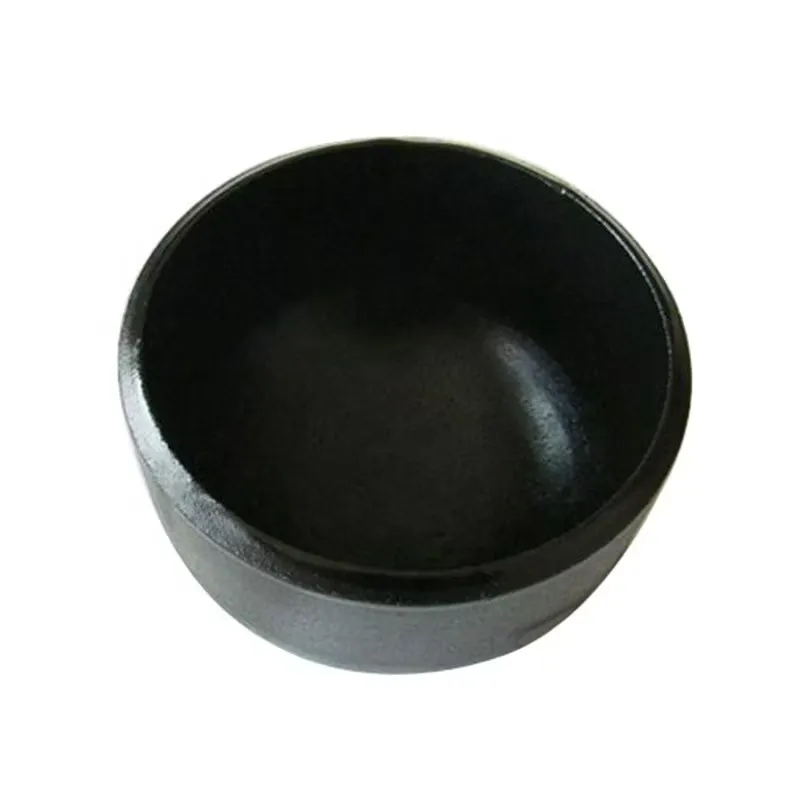
Professionals in the field emphasize the importance of preparation before even striking the first arc. Selecting the right filler material is crucial and should match the base metal as closely as possible to ensure a strong bond. Stainless steel, for example, demands a suitable filler that can withstand high temperatures without compromising integrity or causing contamination. Furthermore, cleaning the pipe thoroughly is essential. Any traces of oil, rust, or dirt can affect the quality of the weld, leading to weak points susceptible to cracking.
Positioning plays a significant role in achieving a successful weld. For round pipes, the use of a rotatable clamp or specialized pipe welding stand can greatly improve the outcome. This equipment allows for stable positioning of the pipe, reducing the likelihood of defects caused by movement or instability during welding. Additionally, it enables the welder to maintain a consistent technique, crucial in producing a clean and reliable seam.
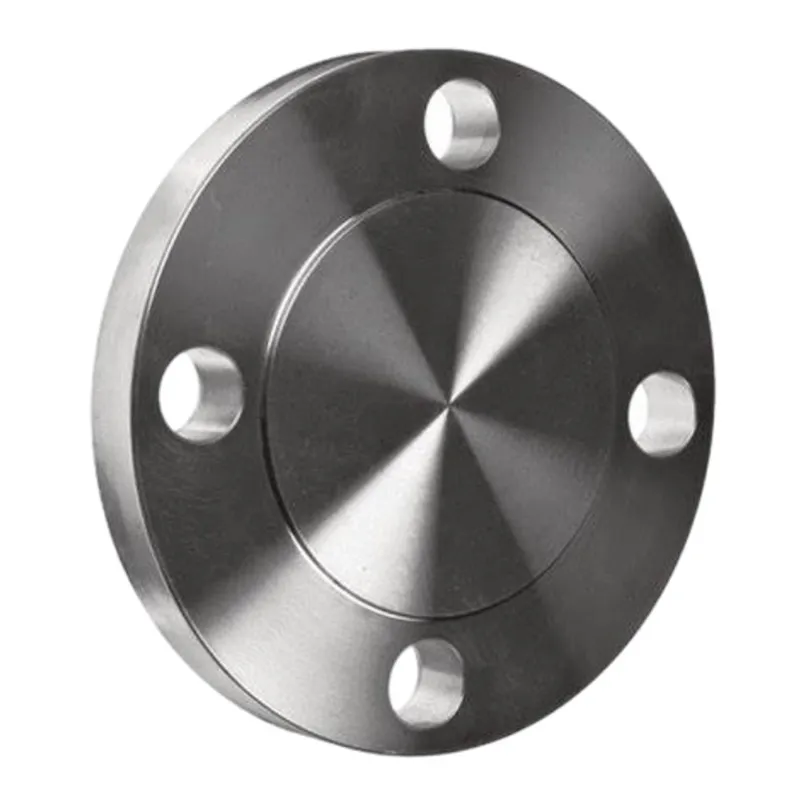
Employing the correct welding technique is paramount. Tungsten Inert Gas (TIG) welding is often recommended for round pipe welding due to its precision and control. TIG welding allows for more focused heat application, which is beneficial in preventing warping or burn-through in thinner pipes. However, for thicker pipes, Metal Inert Gas (MIG) welding might be more suitable due to its faster welding speed and deeper penetration, essential for achieving a robust weld.
welding round pipe
Heat distribution is another critical factor to consider. Round pipes, especially those with larger diameters, can suffer from uneven heating, which might lead to distortion or weak seams. Preheating the pipe before welding can mitigate this risk, ensuring that the entire pipe is at a uniform temperature when welding begins. Equally, post-weld heat treatment may be necessary for high-stress applications, further strengthening the pipe and prolonging its service life.
Expert welders understand the significance of compliance and certification. Adhering to established standards such as those set by the American Welding Society (AWS) can greatly enhance the reliability of a welded round pipe. Certified welders often exhibit a higher level of skill, backed by documented training and experience. This professional assurance is particularly vital in sectors where safety and reliability are paramount.
Finally, consistent inspection and testing should not be overlooked. Non-destructive testing (NDT) methods, such as ultrasonic or radiographic testing, can reveal internal flaws invisible to the naked eye. These tests provide a layer of confidence that the welded pipe meets all necessary specifications and safety standards.
In summary, the successful welding of round pipes is a meticulous process that hinges on preparation, technique, and quality assurance. By prioritizing these aspects, professionals can produce welds that not only meet but exceed industry standards, establishing a benchmark for excellence and safety in the fabrication of round pipes.