Welded pipes are an integral component in various industries, from construction and engineering to energy and manufacturing. With a focus on delivering both durability and efficiency, these pipes have become a staple for professionals seeking reliable solutions. To understand welded pipes fully, it’s essential to delve into their benefits, applications, and the expertise required for their use.
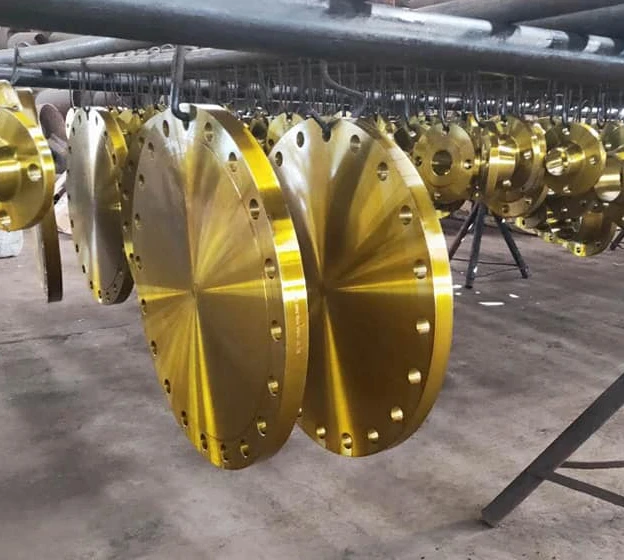
The construction of a welded pipe involves welding the seams of rolled-up strips of metal, usually steel or stainless steel, to form a solid, circular shape. This method of construction is known for its efficiency and cost-effectiveness, as it allows for the mass production of pipes in various sizes and thicknesses. The process includes Electric Weld (ERW), Double Submerged Arc Weld (DSAW), and Longitudinal Weld (L-SAW), each offering distinct advantages based on the application.
One of the primary benefits of welded pipes is their ability to withstand high pressure, making them ideal for transporting gases and liquids over long distances. Their seamless construction offers a smooth interior surface, promoting unobstructed flow and reducing the risk of corrosion. This characteristic is particularly crucial in the oil and gas industry, where maintaining the integrity of transported materials is paramount.
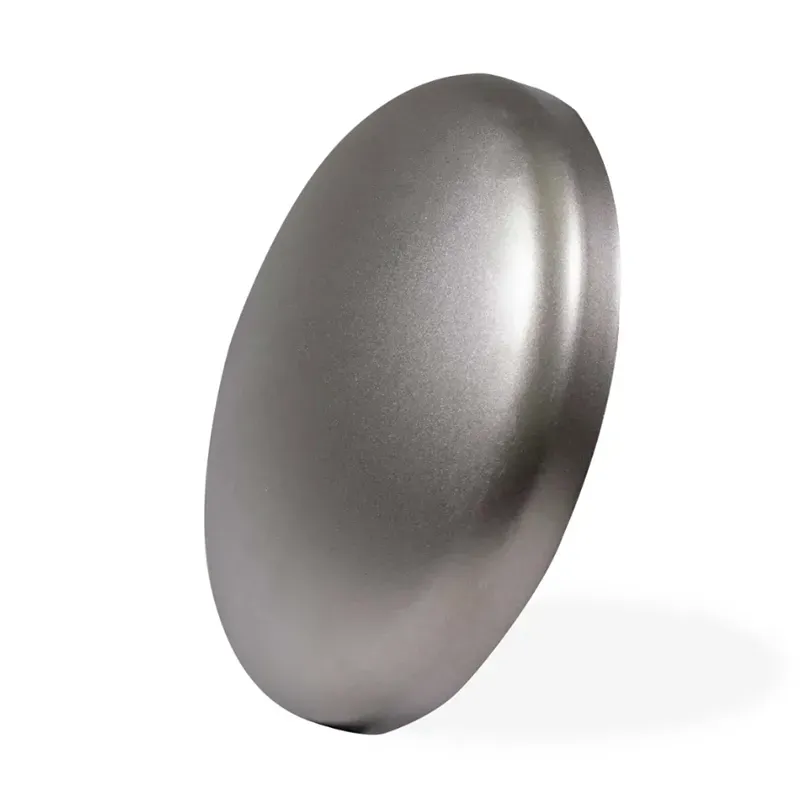
In manufacturing, welded pipes are praised for their versatility. They are essential in fabricating equipment and machinery, providing structural support due to their robustness and reliability. Their adaptability allows for customization in thickness and length, meeting the specific needs of complex industrial applications.
From an environmental perspective, the manufacturing process of welded pipes has seen significant advancements, with a focus on sustainability. Utilizing recycled materials has become commonplace, reducing waste and contributing to a reduction in the carbon footprint of production operations. This not only aligns with global sustainability goals but also appeals to environmentally conscious consumers and businesses.
weld pipe
The expertise required to work with welded pipes cannot be overstated. Professionals in the field must possess a deep understanding of the materials' properties and the specifications necessary for each application. This knowledge ensures that the selection and installation of the pipes meet the stringent standards required by industrial regulations and safety protocols.
Authoritative sources, including industry standards organizations, provide invaluable resources for understanding the complexities of welded pipes. The American Society for Testing and Materials (ASTM) and the American National Standards Institute (ANSI) offer guidelines that establish the quality and safety benchmarks for these pipes. Adhering to such standards not only guarantees performance but also assures the trustworthiness of the end products.
In areas of engineering and architecture, welded pipes are invaluable for their structural capabilities. Their use in building frameworks due to their strength-to-weight ratio demonstrates the confidence professionals have in these products. Moreover, innovations in pipe design, such as corrosion-resistant coatings and smart monitoring systems, have expanded their application scope, reinforcing their position as a go-to solution in infrastructure development.
One cannot overlook the economic aspect of using welded pipes. Their cost-effectiveness compared to other options, such as seamless pipes, offers businesses the opportunity to maintain budgets without compromising on quality or performance. Cost savings extend beyond purchasing to installation, as welded pipes are easier to maneuver and fit into specified layouts, reducing labor costs and time.
In summary, welded pipes represent more than just a tool for industries; they are a testament to advanced engineering and adaptability in modern applications. With ongoing innovations and a commitment to sustainability, they continue to earn their place as cornerstones of industrial efficiency. As technology evolves, so too will the capabilities of welded pipes, ensuring they remain indispensable in a world that relies on robust and reliable infrastructure.