When it comes to joining together two pipes, welding is often the method of choice, offering a seamless and robust connection ideal for various applications, from plumbing to industrial manufacturing. The nuances involved in welding two pipes together demand a blend of practical experience, specialized knowledge, authoritative judgment, and trustworthy practices to ensure both safety and performance are uncompromised.
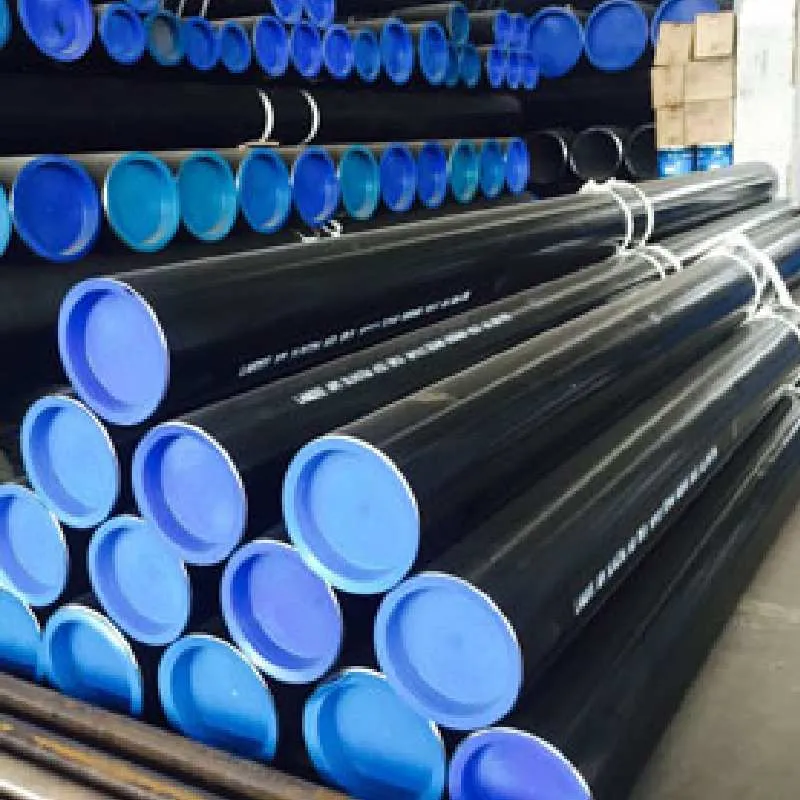
Successful pipe welding begins with selecting the appropriate type of weld, which largely depends on the material of the pipes and their intended use. Commonly used welding methods include TIG (Tungsten Inert Gas), MIG (Metal Inert Gas), and Stick Welding. TIG welding, known for its precision, is especially suitable for thin-walled pipes and materials like stainless steel and aluminum. In contrast, MIG welding is more versatile and user-friendly, often preferred for larger-scale projects involving thicker, non-ferrous metals. Stick welding, while traditional, remains relevant for its adaptability across different environments and materials.
Proper preparation of the pipes before welding cannot be overemphasized. It involves cleaning the pipe surfaces from contaminants such as oil, rust, and dirt, as impurities can lead to weak welds or defects. The edges of the pipes must be beveled to create a chamfer that allows the weld to penetrate deeply, ensuring a strong joint. Utilizing abrasives or beveling tools can achieve the ideal edge angle and finish.
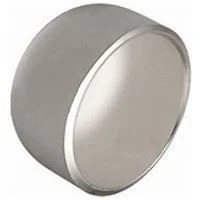
A critical component of pipe welding is alignment. Misalignment can lead to joint failures or recurring stress points within the piping system. Utilizing pipe clamps or spider clamps can help maintain alignment throughout the welding process. Furthermore, maintaining a consistent gap between the pipes is essential, often achieved by employing spacers or fit-up tools to ensure proper penetration and filler material distribution during welding.
In terms of expertise, the quality of the weld heavily relies on the welder's skill and understanding of the welding parameters. Adjustments to parameters such as current, voltage, and travel speed are necessary based on the pipe material and its thickness. For instance, materials with higher conductivity, like copper, may require higher settings than steel. It is also paramount to control the interpass temperature between consecutive weld passes, preventing structural weaknesses due to rapid cooling or overheating.
weld two pipes together
Authoritativeness in pipe welding comes from adherence to industry standards and codes, such as those set by the American Welding Society (AWS) or the American Society of Mechanical Engineers (ASME). These standards dictate the acceptable practices and provide guidelines for the quality and safety of welds. Certifications for welders serve not only as a mark of competence but also as a reassurance of adherence to stringent benchmarks.
Trustworthiness in welding processes involves ensuring every weld undergoes rigorous testing and inspection. Non-destructive testing methods, such as radiography or ultrasonic testing, are integral to identifying possible internal defects without damaging the weld. Visual inspections can help detect surface discrepancies, but comprehensive testing ensures integrity under pressure. Documentation of inspections and tests contributes to transparency and accountability, especially in critical applications like gas pipelines or structural frameworks.
Finally, the broader consideration of the weld environment is crucial. Factors such as weather, humidity, and location can affect welding quality. For instance, welding outdoors or in damp conditions requires additional precautions, such as ensuring proper shielding gases and protective gear to prevent contamination and ensure welder safety.
Welding two pipes together, while a common industrial process, involves an intricate balance of technical skill, understanding material science, and rigorous standards adherence. With every weld being a testament to craftsmanship, attention to detail from preparation to inspection underlines the dedication required for this vital task. By maintaining a commitment to precision, safety, and quality, welded pipe joints can meet the demands of a multitude of applications, standing as reliable foundations in diverse fields.