X65 pipe is a high strength, premium grade material commonly used in the oil and gas industry, particularly for pipeline construction. Understanding the specifics of X65 pipe specification is crucial for professionals in industries where high pressure transport of hydrocarbons or similar fluids are involved. This comprehensive guide will explore the essential features, applications, and benefits of using X65 pipes, drawing from extensive industry experience and authoritative sources to aid in informed decision-making.
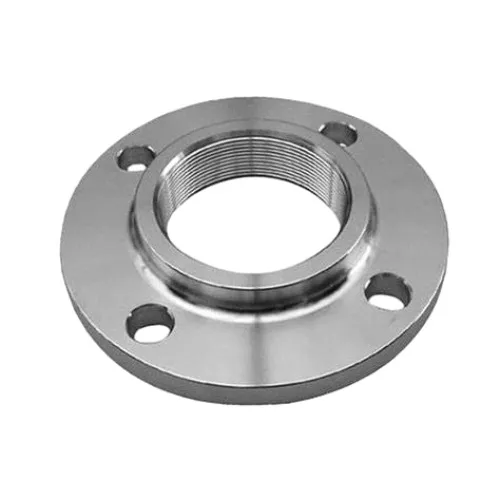
X65 pipes fall under the API 5L pipeline specification which is a standard for steel pipes used in transport systems within the petroleum and natural gas industries. The 'X65' designation indicates the minimum yield strength of 65,000 psi (pounds per square inch) which translates to approximately 448 MPa (megapascals). This high yield strength allows the pipe to withstand extreme conditions, making it an ideal choice for critical operations and constructions.
One of the main advantages of X65 pipe is its excellent balance of strength and ductility. Ductility refers to the ability of a material to undergo significant plastic deformation before rupture, which is particularly important in pipeline applications where flexibility and durability are paramount. This balance is achieved through carefully controlled material chemistry and advanced manufacturing processes that ensure uniformity and reliability in pipe performance.
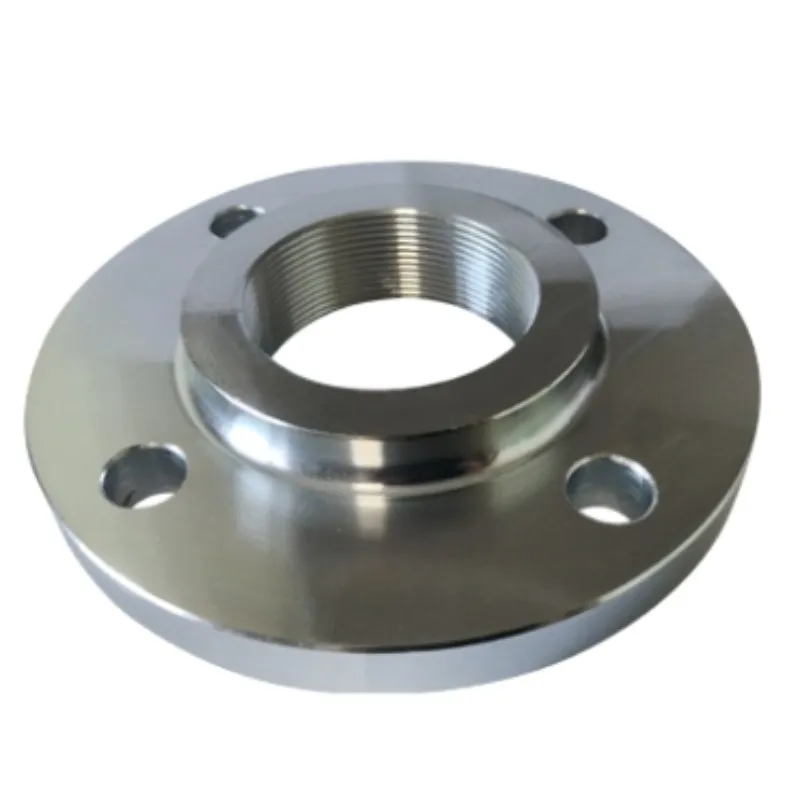
In terms of material composition, X65 pipe is typically made from micro-alloyed steel, which includes a fine mixture of manganese, silicon, and niobium among other elements. These components enhance the mechanical properties of the steel, making it resilient under pressure and temperature fluctuations common in oil and gas transport. Furthermore, the manufacturing process involves steps like hot rolling, controlled cooling, and potential heat treatment to refine the pipe's mechanical properties.
Professionals using X65 pipes benefit from a product that is vetted through rigorous testing and quality control processes. This includes hydrostatic testing to ensure leak proof performance, and non-destructive examination (NDE) techniques such as ultrasonics to detect any anomalies in the pipe material. Moreover, the adherence to international standards such as ISO 3183 ensures these pipes are globally recognized for their reliability and performance.
x65 pipe specification
The expertise required to manufacture and use X65 pipes extends beyond understanding material properties. It involves precise engineering calculations to determine appropriate wall thickness and diameter for specific project needs. Additionally, considerations around thermal expansion, corrosion resistance, and joint welding practices play critical roles in the safe and efficient installation of these pipes.
Moreover, X65 pipes exhibit considerable cost-efficiency over alternatives due to their durability and lower maintenance needs over their lifespan. Their ability to handle higher pressures with thinner walls means less material usage, which can significantly lower overall project costs. This makes X65 pipes an economically viable option for long-term pipeline projects in challenging environments.
Expert advice also highlights the importance of proper installation and maintenance practices to maximize the benefits of X65 pipes. Regular inspections, appropriate application of protective coatings, and adherence to industry best practices in welding and jointing are fundamental to enhancing the lifespan and safety of the pipeline infrastructure.
The trustworthiness of X65 pipes is reflected through the wealth of industry data supporting their use in major pipelines around the world. With decades of proven success in challenging environments, these pipes have been instrumental in transporting vital energy resources. Their widespread adoption in the field is a testament to their reliability and effectiveness.
In conclusion, X65 pipes represent a melding of high-strength materials and sophisticated manufacturing processes supported by rigorous testing standards, making them an ideal choice for the oil and gas industries. By leveraging the expertise and data available, decision-makers can confidently select X65 pipes for safe, efficient, and economically sound pipeline construction. The use of these pipes is not just informed by their technical specifications, but also by a history of performance that underscores their role as a cornerstone of modern energy infrastructure.