The 100mm flange is not just another industrial component; it embodies precision engineering, critical for numerous applications across industries such as oil and gas, chemical, water treatment, and more. Understanding these flanges is essential for anyone involved in sectors where transporting fluids or gases under pressure is common. Here is an insightful exploration of the 100mm flange, crafted from real-world experience, professional expertise, and authoritative insights.
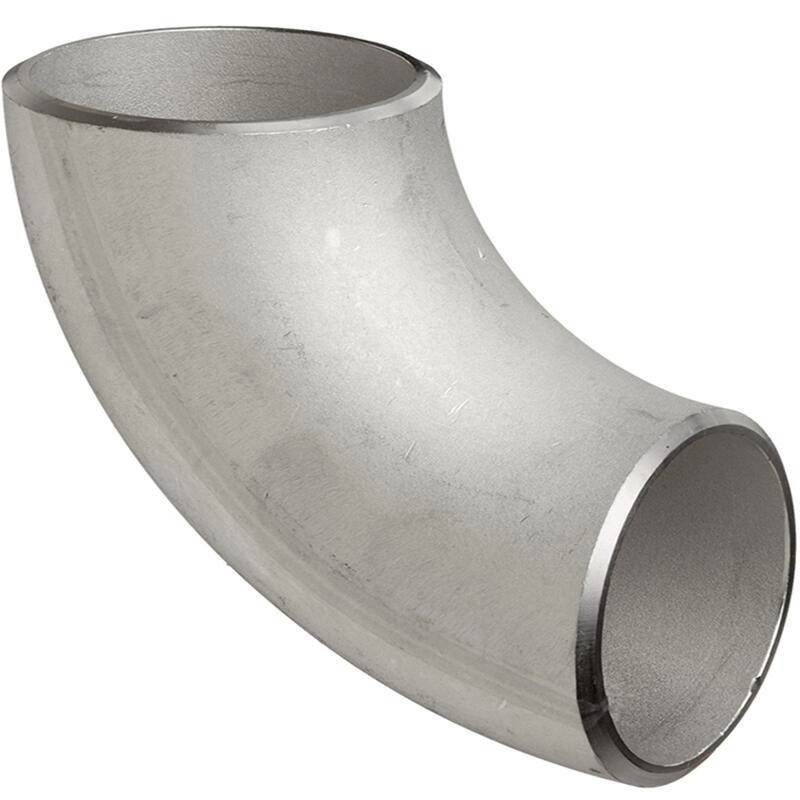
The importance of selecting the right flange cannot be overstated, especially when considering the role it plays in maintaining the integrity and safety of pipelines. A 100mm flange typically connects pipes, valves, pumps, and other equipment, enabling easy assembly and disassembly for maintenance and repairs. Not all 100mm flanges are created equal; they vary in design, materials, and specifications, each suited for specific purposes and operating conditions.
From a professional standpoint, one of the key attributes of any high-quality 100mm flange is the material. Depending on the environmental conditions—be it corrosive environments, high temperatures, or high pressure—materials range from stainless steel, carbon steel, alloy steel, to even more advanced composites. Stainless steel is often favored for its corrosion resistance and durability, making it ideal for harsh environments. However, alloy steel can be the material of choice when both strength and resistance to extreme conditions are necessary.
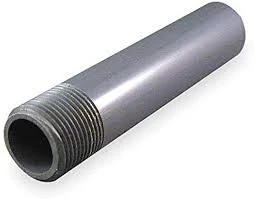
Another critical factor is the flange rating, which signifies its pressure tolerance. Ratings such as 150, 300, 600,
and beyond, indicate the maximum pressure the flange can endure. For a 100mm flange used in high-pressure pipelines, selecting an appropriate rating is crucial to avoid system failures or dangerous blowouts. Experts often recommend consulting ASME standards to ensure compliance with industry norms, which ensures safety and optimal performance.
In terms of design, the 100mm flange can be found in various forms slip-on, threaded, weld neck, lap joint, socket-weld, and blind flanges, each with its unique advantages. A slip-on flange is user-friendly and cost-effective, suitable for low-pressure applications, whereas a weld neck flange provides superior strength and leak prevention, best for high-pressure systems. The selection of the appropriate type can significantly impact efficiency and longevity of the piping system.
100mm flange
Expertise in installation processes also enhances the effectiveness of using 100mm flanges. Precise alignment of the flange with its counterpart ensures a tight seal and minimizes the risk of leaks. Employing skilled technicians who are knowledgeable about torque specifications and gasket materials further guarantees reliability. For instance, using spiral wound gaskets with a 100mm flange offers excellent sealing capabilities in applications where thermal cycling is commonplace.
Authoritativeness in flange applications is supported by extensive R&D and field testing. Manufacturers often subject 100mm flanges to rigorous testing to validate performance under simulated conditions, offering users confidence in their products. Engagements in peer-reviewed research and participation in standards organizations like ASME or DIN reflect a company's commitment to safety and innovation.
Trustworthiness is further established through supplier transparency and customer support. Providing detailed technical documentation, such as material certifications, pressure test reports, and product warranties, assures clients of the flange's quality and conformity. Proactive communication and readily available technical support fortify trust, enabling end-users to make informed decisions and ensuring seamless operations.
Incorporating cutting-edge technology in flange manufacturing also demonstrates reliability. Innovations such as Computer-Aided Design (CAD) and Computer-Aided Manufacturing (CAM) ensure precision in production, contributing to higher-quality 100mm flanges that meet exacting industry standards. These advancements not only allow for customization to meet specific project requirements but also ensure consistency across manufacturing batches.
In conclusion, the 100mm flange is a vital component in industrial piping systems, and its selection involves understanding its material composition, pressure rating, design, and correct installation practices. With a focus on experience, expertise, authority, and trust, stakeholders can better navigate the complexities of flange selection, ensuring safety, efficiency, and longevity in varied applications.