The world of industrial manufacturing and engineering relies heavily on the use of pipe flanges to ensure robust and reliable connections in a variety of applications. Among the various types, the 1 1 2 pipe flange stands out as a crucial component in fluid transfer systems, offering unique benefits that cater to specific industrial needs.
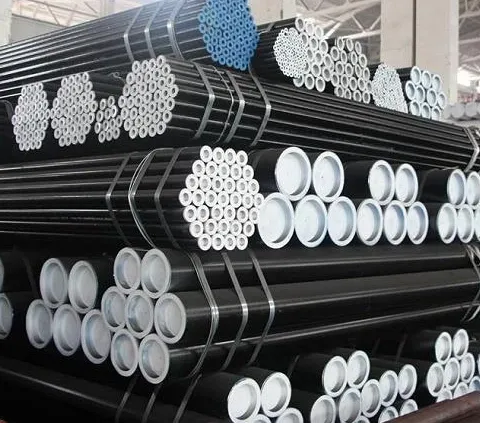
A 1 1 2 pipe flange refers to a flange used in pipes that have a nominal bore size of one and a half inches. This particular specification is widely utilized across many sectors, including petrochemical plants, water treatment facilities, and manufacturing units, where precise and durable pipe connections are needed. Its versatility arises not only from its size but from its ability to be adapted to different pressures and temperature conditions, making it an integral part of many operations.
Experience is key when dealing with 1 1 2 pipe flanges. Those who have worked with different piping systems will testify to the importance of selecting the right flange type for a given application. Whether used in high-pressure steam conduits or corrosive chemical environments, the right material and design can significantly impact the effectiveness and longevity of the pipe system. Experienced technicians often recommend stainless steel flanges for environments exposed to moisture and oxidation, while carbon steel flanges might be suitable for high-pressure requirements where temperature fluctuations are minimal.
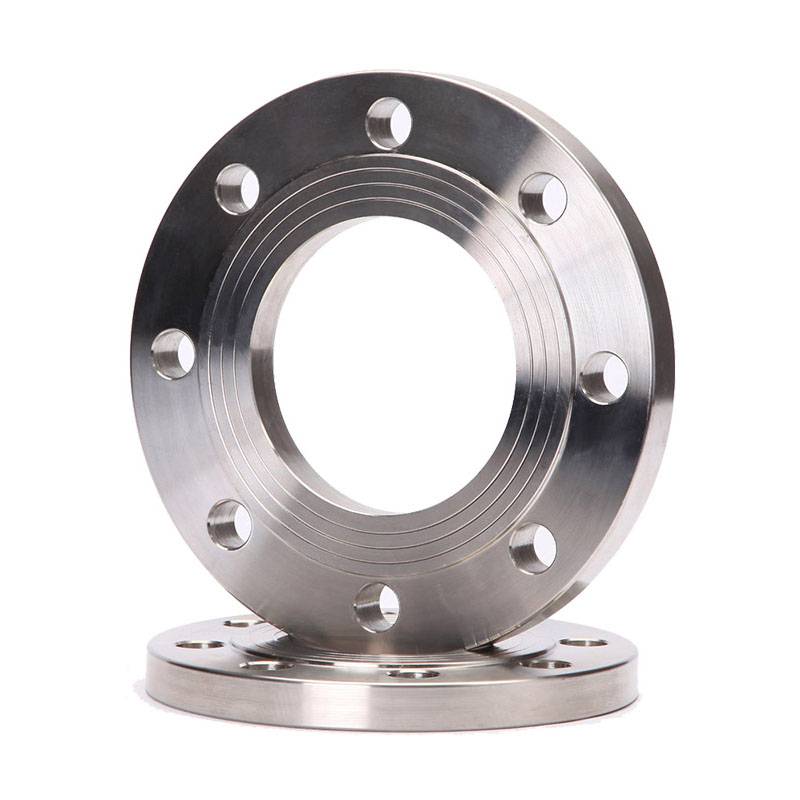
Experience also plays a role in installation and maintenance. Proper alignment is critical when installing flanges to prevent leakage and ensure a secure fit. Maintenance involves regular inspection of gaskets and bolts, which, if neglected, could lead to system failures. Technicians with hands-on experience know the tell-tale signs of wear and can address potential issues before they escalate, which underscores the value of having seasoned professionals oversee these tasks.
1 1 2 pipe flange
The expertise involved in manufacturing 1 1 2 pipe flanges lies in the understanding of various industrial standards and specifications. Manufacturers must adhere to stringent industry standards such as ASME, ANSI, and DIN when producing flanges to ensure compatibility and safety. Expertise is also reflected in the design process, where engineers must calculate factors such as load-bearing capacities, stress distribution, and material properties to create flanges that not only meet but exceed industry requirements. This expertise is paramount in applications where even the slightest miscalculation can lead to significant operational setbacks.
In terms of authoritativeness, companies that produce 1 1 2 pipe flanges often have decades of experience in the industry, backed by certifications and memberships in professional organizations. These companies employ rigorous quality control processes, using advanced non-destructive testing methods to verify the integrity of their products. Authoritative manufacturers are also at the forefront of innovation, frequently updating their product lines to incorporate the latest advancements in metallurgy and engineering design. When selecting a supplier, businesses often look for these credentials as a testament to the manufacturer’s capability and reliability.
Trustworthiness, meanwhile, is demonstrated through a manufacturer’s ability to provide comprehensive documentation, such as Material Test Reports (MTRs) and Certificates of Compliance. Transparent communication and support services are hallmarks of a trustworthy partner. Clients need assurance that the products they purchase meet all safety and performance standards. This trust is further cemented by a manufacturer’s willingness to offer warranties and stand behind their products, ensuring that customers can rely on their flanges for critical applications without hesitation.
The 1 1 2 pipe flange is more than just a mechanical component; it is a critical part of many industrial operations, and its success depends heavily on experience, expertise, authoritativeness, and trustworthiness. Businesses seeking reliable piping solutions must consider these factors to ensure they select flanges that align with their operational demands and safety standards. By doing so, they can maintain seamless operations, reduce downtime and enhance the overall efficiency of their systems.