In the realm of industrial applications and plumbing systems, precision components play an indispensable role, and a 1/2 inch flange is a pivotal example of this. This versatile component may seem small in scale, but its implications and utility are profound, ensuring the seamless operation of various essential systems. This article will delve into the world of 1/2 inch flanges, exploring their applications, material options, and the expertise involved in selecting and utilizing this critical component.
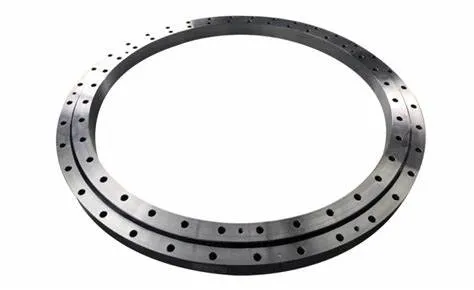
The 1/2 inch flange serves as a connector, providing stability and a secure seal between pipes, valves, pumps, and other equipment. Its size makes it particularly effective in systems where compactness is as crucial as reliability. Frequently employed within both domestic and industrial contexts, these flanges are versatile for plumbing, chemical processing, and even in high-pressure environments. The expertise required to select the appropriate flange type depends largely on the specific application and the environment in which it will operate.
There are numerous types of 1/2 inch flanges available on the market, each crafted from a range of materials including stainless steel, carbon steel, and PVC. The choice of material significantly impacts the flange's performance characteristics
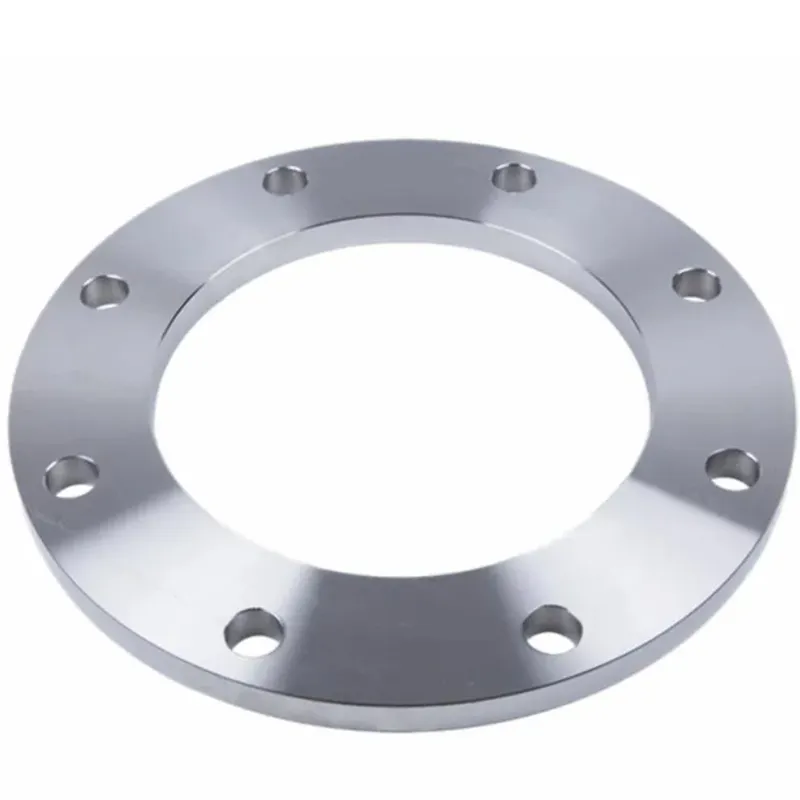
1. Stainless Steel Flanges Known for their robustness, resistance to corrosion, and longevity, stainless steel flanges are often the go-to choice for industries where hygiene and durability are paramount. They are commonly used in food processing, pharmaceuticals, and other sectors where contamination must be minimized.
2. Carbon Steel Flanges These offer excellent performance in high-pressure environments. While not as corrosion-resistant as stainless steel, carbon steel flanges are a cost-effective choice for water and gas pipelines where such conditions are managed.
3. PVC Flanges Lightweight and resistant to chemical deterioration, PVC flanges are ideal for low-pressure applications such as drainage systems and residential plumbing.
1 2 inch flange
An authoritative understanding of the environment and operational pressures is critical when choosing a flange. Incorrect selection can lead to system failures, leaks, or even catastrophic malfunctions, thus underscoring the importance of a highly knowledgeable selection process. Engaging with suppliers who offer specialized advice and support can enhance the trustworthiness of decisions made in this realm.
The installation process for a 1/2 inch flange demands technical precision and expertise. Proper alignment and torquing of bolts ensure a thorough seal, essential to prevent leaks and maintain system integrity. Technicians must follow specified procedures, employing the correct tools and torque settings to guarantee that flanges are fitted optimally.
Ensuring the credibility of this information involves consulting industry standards, such as those set by the American Society of Mechanical Engineers (ASME), which provides extensive guidelines for manufacturing and installing flanges of all dimensions and configurations.
Incorporating technological advancements, many industries are moving towards the use of digital torque measurement and alignment tools. These innovations aid in achieving unparalleled precision during installation, thus enhancing the reliability and performance of the system. Staying abreast of these technological advancements is critical for professionals seeking to maintain their competitive edge in the market.
Moreover, maintenance of installed flanges warrants an ongoing commitment to quality control and regular system checks. Routine inspections ensure that flanges remain free of corrosion, wear, and misalignment, all of which can compromise system efficacy. Replacement of gaskets and re-torquing of bolts may be necessary to ensure continued performance in line with initial specifications.
In conclusion, the 1/2 inch flange is a small but mighty component integral to multiple systems requiring high reliability and performance. Its selection, installation, and maintenance require an in-depth understanding of the physical demands and operational conditions it will encounter. Employing components from reputable manufacturers, staying informed on current best practices and technological trends, and leveraging extensive industry standards contribute to achieving successful and trusted applications. By prioritizing expertise, authority, and trustworthiness in the handling of such components, businesses can ensure longevity and efficiency across their operational frameworks.