Alloy steel seamless tubes have become a pivotal component in various industrial sectors, thanks to their remarkable strength, durability, and resistance to corrosion. In the world of modern manufacturing, construction, and engineering, these tubes stand out for the unique advantages they bring, especially when compared to their welded counterparts.
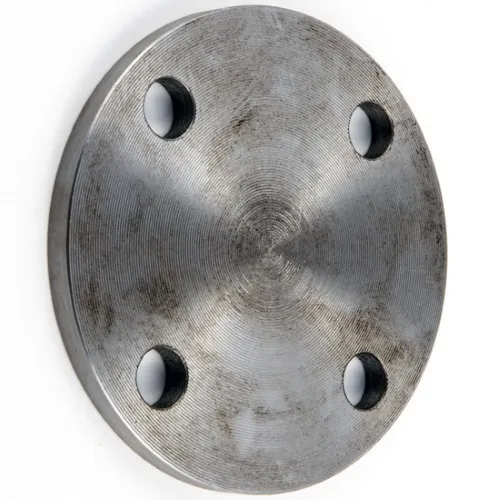
One of the primary factors that set alloy steel seamless tubes apart is their method of manufacture. Unlike welded tubes, seamless tubes are crafted through a process that involves piercing a solid billet of alloy steel, followed by elongation and shaping. This creates a tubular product without any joints or seams, reducing the potential for weak points that can arise in welded pipes. The absence of seams provides a uniform structure that ensures consistent performance, particularly under high-pressure and high-temperature conditions, making these tubes highly suitable for applications such as oil and gas exploration, power generation, and chemical processing.
In applications where precision and reliability are paramount, alloy steel seamless tubes excel due to their superior dimensional accuracy and exceptional structural integrity. Engineers and manufacturers often prefer them for their ability to withstand extreme environments without succumbing to the stresses that can lead to material failure. Industries that demand robust materials frequently choose alloy steel seamless tubes because they offer enhanced mechanical properties. These qualities ensure that the tubes can endure significant strain and stress, providing a longer service life and reducing the frequency of replacements and maintenance.

Several alloy formulations are used for creating seamless tubes, each designed to deliver specific properties for tailored applications. Common alloys used in manufacturing these tubes include chromium-molybdenum steels, which offer excellent resistance to high pressures and temperatures.
This makes them ideal for use in steam boilers and other high-pressure environments. Another popular choice is high-strength low-alloy (HSLA) steel, which provides additional toughness and resistance to atmospheric corrosion, often employed in structural applications and heavy-duty machinery.
Expertise in the production and application of alloy steel seamless tubes is crucial to ensuring optimal performance. Professionals in this field understand the intricate balance between the material composition and the operational environment. They provide guidance on selecting the appropriate alloy and tube specifications that align with the project's requirements. Such expert advice is vital to maximize the benefits and lifecycle of the tubes while minimizing downtime and operational costs.
alloy steel seamless tube
Trustworthiness in choosing alloy steel seamless tubes comes from sourcing them from reputable manufacturers who adhere to stringent quality control measures. These manufacturers follow international standards such as ASTM, ASME, and ANSI, ensuring the tubes meet or exceed industry expectations. Certifications and rigorous testing protocols further validate the integrity and reliability of the products, providing assurance to clients that they are investing in quality materials.
The authoritativeness of alloy steel seamless tubes in the industry is further cemented by extensive research and development efforts aimed at enhancing their properties. Innovations in metallurgy and manufacturing processes continue to expand the capabilities and applications of these tubes, securing their place as a preferred choice in various high-stakes industries.
Investing in alloy steel seamless tubes not only reduces the risk of operational failures but also aligns with sustainable practices by prolonging the lifecycle of infrastructures and machinery. The sustainability aspect, coupled with their unrivaled performance, positions these tubes as an indispensable resource in the global push toward efficiency and reliability in industrial operations.
In conclusion, alloy steel seamless tubes offer unmatched advantages in strength, durability, and performance. Their seamless construction eliminates common vulnerabilities, making them a trusted solution for high-pressure and high-temperature applications. With expertise, quality assurance from reputable manufacturers, and continuous innovation, these tubes remain at the forefront of industrial materials, delivering unparalleled value and reliability.