In the niche realm of industrial fittings and their applications, the term DIN flange often surfaces as a critical component in many projects. Known for its European origins, specifically standardized by the Deutsches Institut für Normung (DIN), these flanges serve as essential elements ensuring the secure connection of various sections of piping systems. Their role is pivotal in industries ranging from oil and gas to pharmaceuticals, demonstrating not just versatility but also reliability.
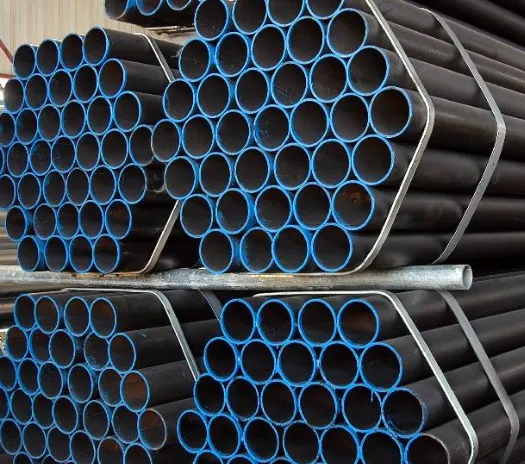
The demand for DIN flanges is significantly linked to their unparalleled specifications and performance assurances. One of their most attractive features is their consistency in quality, which is not merely a superficial observation but a testament to rigorous production standards that assure compatibility and longevity in use. For any engineer or technician working in a field where precision is paramount, this consistency translates to fewer hitches during implementation and in the long run, reduced operational disruptions.
However, what sets DIN flanges apart in the marketplace is not just their quality but the breadth of their adaptability to varying industrial needs. Available in a wide spectrum of sizes and materials, these flanges cater to a range of different pressure ratings and temperature applications. From mild steel suitable for low-pressure applications to stainless steel variants designed for harsh chemical environments, DIN flanges offer solutions that can be tailored to specific project requirements.
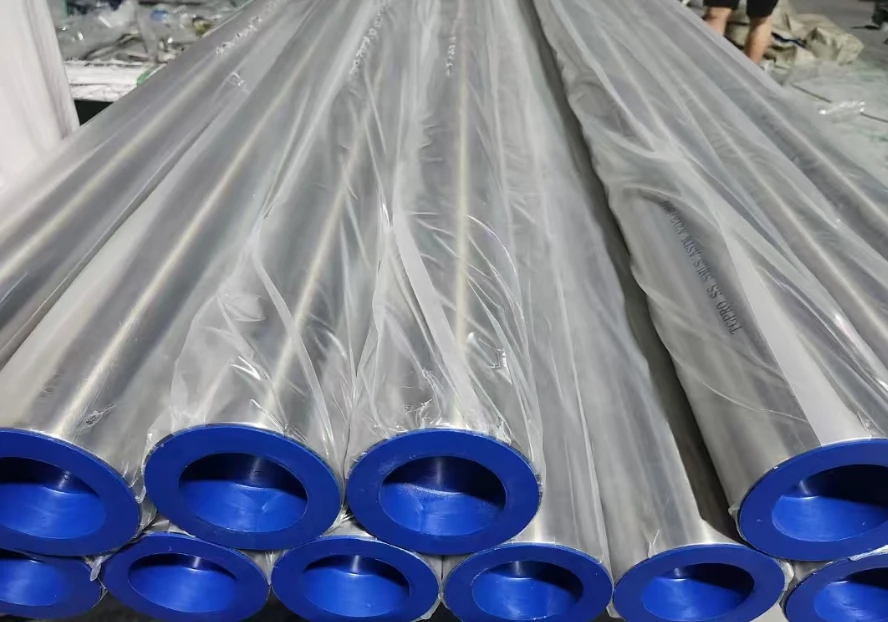
Specialists within the field often highlight the resilience of DIN flanges in critical applications where failure is not an option. This resilience is clearly evidenced in scenarios where high-pressure environments are prevalent. For instance, in petrochemical industries, where the integrity of connections is non-negotiable, DIN flanges have built a reputation as the go-to choice owing to their robustness and compliance with stringent safety regulations. Their reliability in such environments isn't merely anecdotal but is backed by a history of usage in projects where any compromise could lead to catastrophic outcomes.
Beyond mere product specifications, it is essential to delve into the operational experiences of those who predominantly work with DIN flanges. Accounts from project managers and engineers frequently commend the straightforward installation process associated with these flanges. Such ease of installation plays a crucial role in the broader industrial scheme, where time efficiency directly translates to cost-effectiveness. Moreover, the precise fit that comes with DIN flanges often reduces the margin for installation error, further solidifying their standing in the industrial equipment landscape.
din flange
From an expertise perspective, the development and refinement of DIN flanges are usually matched by ongoing research and innovation aimed at enhancing their application efficacy. Manufacturers often engage in continuous improvement processes focusing on aspects such as corrosion resistance, weight reductions, and the refinement of pressure containment capabilities. This commitment to advancement not only benefits current industrial applications but also paves the way for future technological integration, such as compatibility with smart monitoring systems.
Adding to the credibility and authority of DIN flange applications is the well-documented track record of safety and compliance. The rigorous standards that govern the production of these flanges are reflective of an unwavering commitment to maintaining safety and performance. Regulatory compliance ensures that regardless of their global market application, DIN flanges adhere to the highest possible standards, providing peace of mind to all stakeholders involved—project leads, engineers, and safety officers alike.
To encapsulate trustworthiness, the testimonials and feedback from users further cement the authority of DIN flanges in the industry. The practical insights offered by those on the ground often present the most compelling argument for their continued use. Whether it’s the assurance of leak-proof performance in a high-stakes chemical process or the satisfaction of seamless integration in a new plant installation, the experiences shared by professionals provide a narrative that both reassures and convinces the broader community.
In conclusion, DIN flanges are not merely connectors within a system but are integral components that ensure the integrity and efficiency of operations across various industries. Their standing is not just built on historical use but on continuous validation through real-world experience, expert endorsements, and steadfast adherence to safety and regulatory standards. This makes DIN flanges a reliable choice for any project where quality and safety are paramount concerns.