Flanges are essential components in a wide variety of industries, enabling the secure and efficient connection of pipes, valves, and other equipment. In particular, the flange dimension 2 1 2 often refers to a 2 1/2 inch flange, a common size used in numerous applications due to its adaptability and reliability. For those seeking a comprehensive understanding and application of these flanges, several key facets warrant attention.
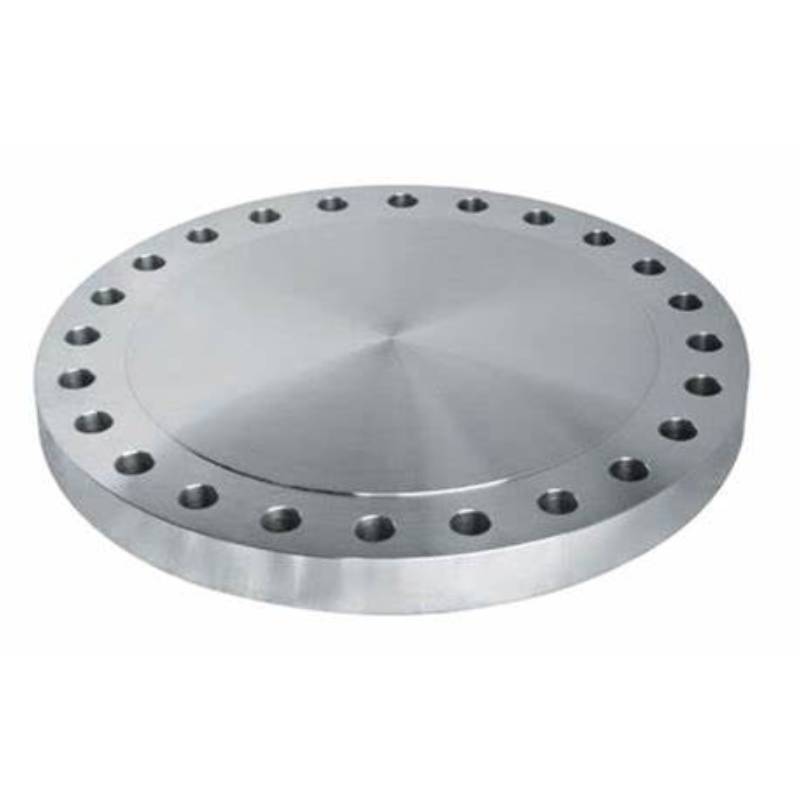
From an experiential perspective, engineers and operators who have extensively worked with 2 1/2 inch flanges highlight their versatility, especially in fluid and gas transmission systems. These flanges offer a robust solution for handling medium to high pressures, making them ideal for both commercial and industrial environments. Commonly used materials for these flanges include stainless steel, carbon steel, and alloy, each providing distinct advantages in terms of corrosion resistance, strength, and cost-effectiveness. Users frequently prefer stainless steel for its longevity and ability to withstand harsh, corrosive environments.
The expertise surrounding 2 1/2 inch flanges involves understanding their compatibility with various pipe schedules and pressure ratings. For instance, selecting the appropriate flange requires matching the flange class with the system’s maximum operating pressures and temperatures. The expertise lies in precisely calculating these parameters to prevent system failures and ensure optimal performance. Additionally, the flange face type, such as raised face, flat face, or ring-type joint, must be selected based on sealing needs and partnered equipment.
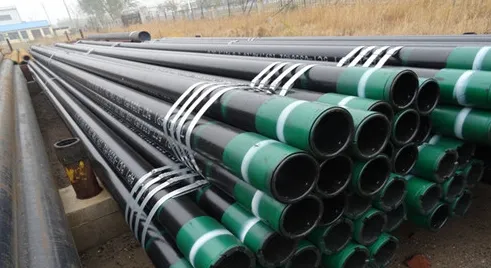
flange 2 1 2
Authoritativeness in the flange domain often comes from certifications and standards compliance. Flanges, including the 2 1/2 inch size, are typically manufactured in accordance with international standards like ANSI, ASME, DIN, or JIS. These standards dictate the dimensions, tolerances, materials, and testing procedures, ensuring consistent quality and compatibility across different systems. Professionals in the field tend to rely on manufacturers that demonstrate adherence to these standards, as well as those that offer thorough chemical and physical property documentation of the flanges.
Trustworthiness of any flange product, particularly a 2 1/2 inch flange, is bolstered by the quality assurance processes employed by the manufacturer. Reliable manufacturers implement rigorous testing protocols, including hydrostatic testing, ultrasonic testing, and radiographic inspection, to verify the integrity and performance of the flange under operational conditions. Additionally, manufacturers providing transparency in their supply chain and material sourcing further instill confidence among purchasers.
In summary, the seemingly simple 2 1/2 inch flange encapsulates a diverse range of considerations impacting its selection and implementation in industrial applications. By embodying a confluence of experience, expertise, authoritativeness, and trustworthiness, these flanges fulfill a critical role in ensuring the safety, efficiency, and longevity of piping systems across various sectors. Businesses and technical experts choosing the right flange type and adhering to industry best practices can significantly enhance the performance and reliability of their operations. This depth of understanding is not only crucial for maximizing the utility of 2 1/2 inch flanges but also for informing maintenance protocols and future upgrades within pipeline infrastructure.