Flange 75 is a crucial component in numerous industrial applications, serving as a vital element in piping systems, mechanical assemblies, and equipment setups. The significance of this component is rooted not only in its structural and functional importance but also in the expertise required to select the right type and specification to ensure optimal performance and safety.
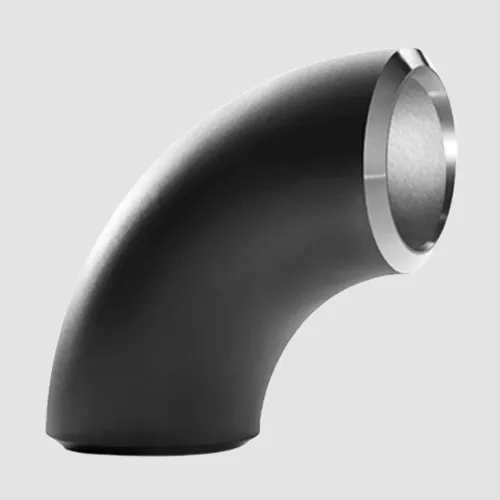
For those engaged deeply in industries such as oil and gas, chemical manufacturing, or water treatment, the choice of a flange is far from trivial. It involves a keen understanding of the operational environment, including temperature, pressure, and material compatibility. Flange 75, in particular, presents a specialized option that caters to specific needs and conditions, making expertise in its use not just advantageous, but essential.
Flange 75, generally denoted by a nominal diameter, represents a category where precision and performance are non-negotiable. It's the convergence of engineering discipline and practical application. Expert advice always recommends a thorough examination of the material composition. Materials such as stainless steel, carbon steel, or alloys are common, each selected based on their resistance to corrosion, heat tolerance, and mechanical wear.
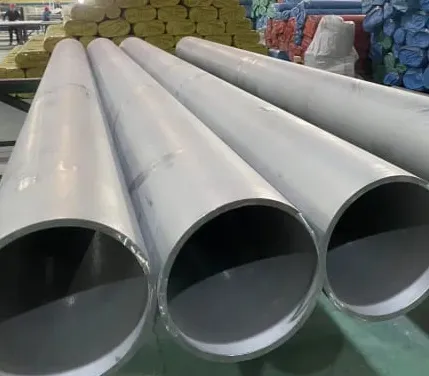
Experience reveals that selecting the right Flange 75 requires more than just an understanding of materials and specifications; it necessitates a familiarity with the standards governing flange production and use. Standards such as ASME (American Society of Mechanical Engineers), ANSI (American National Standards Institute), or DIN (Deutsches Institut für Normung) ensure that the product adheres to strict guidelines for safety and interoperability. For instance, in high-pressure systems, compliance with these standards is not merely a recommendation, but a prerequisite that experts rely on to prevent system failures.
From a technical expertise perspective,
the installation and maintenance of Flange 75 are equally critical. Proper alignment, torque of bolts, and use of appropriate gaskets influence the integrity and longevity of the flange connection. Authoritative guides and training programs are often referenced to mitigate risks such as leaks, which could lead to catastrophic failures.
flange 75
Moreover, the trustworthiness of a flange supplier contributes significantly to the decision-making process. Engaging with reputable and certified manufacturers ensures that the Flange 75 received is of the highest quality, often coming with certifications and warranties that protect the investment. Industry veterans typically evaluate suppliers not just based on cost but also on their track record for delivering reliable components.
The real-world operation of piping systems using Flange 75 components sheds light on the practical aspects that technical documentation might overlook. Field reports often highlight how variations in flange quality or installation precision can drastically affect performance. As such, reliance on a network of industry peers, expert forums, and continuous education is vital for keeping abreast of the latest technologies and practices.
Furthermore, the advent of digital technologies in flange design and manufacturing is enhancing the precision and customization of Flange 75, tailored to increasingly specific applications. Cutting-edge CAD software and simulation tools enable engineers to visualize stress points and predict lifecycle performance, thus elevating the efficacy of flange systems.
In conclusion, Flange 75, while a specific and technical product, embodies the broader principles of expertise, engineering precision, and rigorous standards application. The proper selection, installation, and maintenance of this component are imperative for professionals in fields where reliability and safety are paramount. Its role is enhanced by the infusion of technology and collaborative knowledge exchange among seasoned professionals, ensuring that each application meets the intended specifications and operational demands with unyielding confidence and accuracy.