Flange couplings play a pivotal role in connecting rotating shafts in industrial machinery. They ensure seamless torque transmission, minimize shaft misalignment, and reduce vibrations, enhancing the machinery's overall efficiency and longevity. When selecting the appropriate flange coupling types, it is essential to understand their distinct features and applications to make well-informed decisions that enhance operational performance.
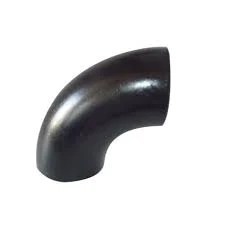
Flange couplings can be broadly categorized into several types, each tailored for specific applications and operational conditions.
The rigid flange coupling is perhaps the most fundamental type. Characterized by its secure mechanical fit and robust construction, it is typically employed in applications where shaft alignment is near perfect, as it provides no flexibility in adjustments. This type eliminates any relative motion between the connected shafts, ensuring a stable and solid connection. Industries where machines are naturally aligned, such as water treatment plants or in certain manufacturing processes, frequently adopt rigid flange couplings.
On the other hand, the flexible flange coupling offers a blend of performance and adaptability. Designed to accommodate minor misalignments and fluctuations, these couplings incorporate an elastomeric element between the flanges. This feature absorbs shock loads and dampens operational vibrations, which is crucial in dynamic systems such as conveyor belts or large-scale fans. Additionally, flexible couplings can accommodate axial, radial, and angular misalignments, making them suitable for machinery that experiences variable operational conditions or where precise alignment is challenging to maintain.

Another popular configuration is the gear flange coupling. Its unique design comprises interlocking teeth that facilitate torque transfer across misaligned shafts. Gear flange couplings are often used in heavy-duty environments like mining or construction, where robust performance under high torque is paramount. Its ability to accommodate large misalignments makes it indispensable in applications where precision alignment is not feasible. Furthermore, the teeth are usually lubricated, reducing wear and enhancing the service life of the coupling.
Spring-loaded flange couplings provide an innovative solution for applications requiring gentle engagement and disengagement during operation. By employing a set of springs, these couplings allow controlled torque transfer and are pivotal in applications involving frequent start-stop cycles, such as assembly lines or packaging units. They mitigate the impact of sudden torque changes on associated machinery, reducing downtime and maintenance costs.
flange coupling types
Within the domain of advanced mechanical applications, the Magnetic flange coupling stands out due to its contactless nature. Utilizing magnetic forces to transmit torque, these couplings eliminate the risk of mechanical wear and are most appropriate for environments where sealing and contamination concerns are critical, such as chemical or pharmaceutical processing. Their non-contact design also allows for service in vacuum and cryogenic settings.
Increasingly, intelligent flange couplings—integrating IoT technologies—are emerging. By embedding sensors and communication devices, these couplings can provide real-time data on operational status, efficiency, and predictive maintenance alerts. This technological advancement ensures that modern industrial setups remain ahead in terms of efficiency and responsiveness to mechanical conditions, enhancing overall reliability.
When selecting the appropriate flange coupling, it is crucial to consider factors such as rotational speed, torque capacity, misalignment tolerance, and environmental conditions. Each type brings unique advantages, and understanding these will guide you to the ideal solution that promotes operational excellence. Consulting manufacturers or industry experts can further aid in selecting the right coupling type, ensuring that the integration will reinforce the machinery’s performance and contribute to its longevity.
In summary, flange couplings are indispensable in industrial applications, providing essential connections that maintain operational efficiency. Recognizing the various types and their distinct applications ensures optimal machinery performance, minimizing downtime, and reducing maintenance costs. By leveraging the expertise in choosing and maintaining flange couplings, industries can realize improved productivity and sustainable operational practices.