In the world of industrial components, flange factories play a crucial role in ensuring the seamless operation of countless applications. As the backbone of mechanical connections, flanges are indispensable in industries ranging from oil and gas to waterworks. A visit to a cutting-edge flange factory reveals a blend of advanced manufacturing techniques and stringent quality assurance processes that underline the importance of such components in our day-to-day industrial functions.
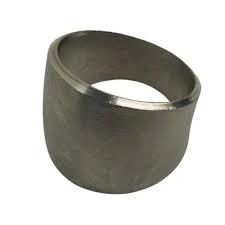
The journey of a flange begins with the careful selection of raw materials. A reputable flange factory sources high-grade steel and other alloys to guarantee durability and performance. This step is critical as the choice of material influences not only the flange's strength but also its resistance to environmental factors like corrosion and pressure variances. The expertise of metallurgists in the factory ensures that each batch of material meets international standards before entering the manufacturing process.
When it comes to manufacturing, precision is paramount. Modern flange factories are equipped with state-of-the-art CNC machinery that allows for the creation of flanges with exceptional accuracy. These machines, often operated by seasoned technicians with years of experience, can produce flanges in a variety of sizes, pressure ratings, and specifications. Whether a customer requires a standard or custom-designed flange, the factory's capability to adapt and deliver is a testament to its professional expertise.
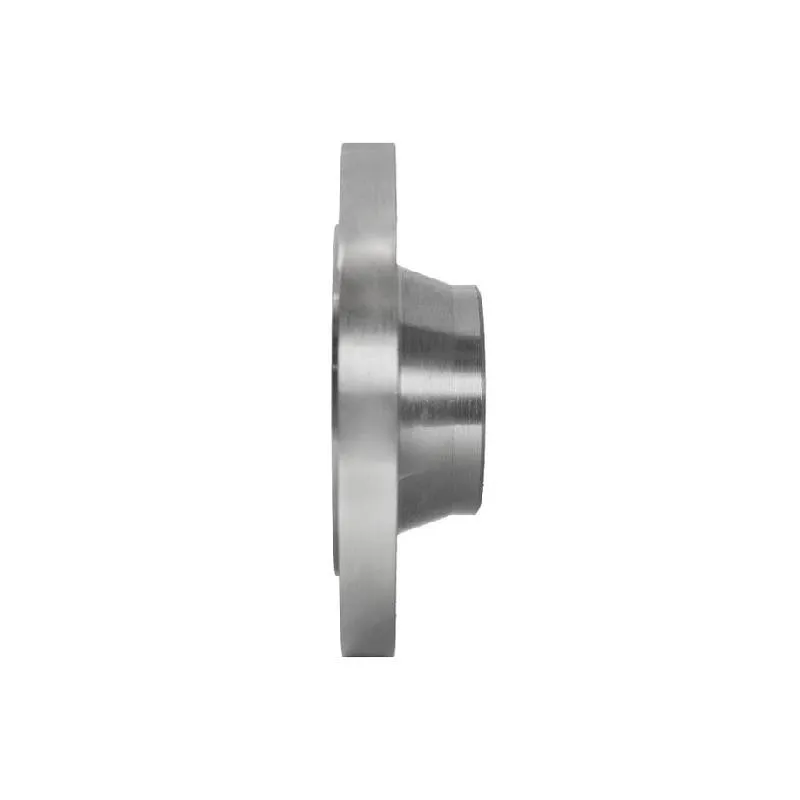
Quality assurance in a flange factory is a rigorous process that underscores the facility's commitment to reliability and safety. Each flange undergoes a series of tests, including dimensional checks, pressure testing, and surface inspections. The factory's dedication to maintaining a high level of authoritativeness in its testing procedures is crucial in building trust with clients. OEMs and contractors rely heavily on the factory's documented quality controls that align with international benchmarks such as ISO and ASME standards.
flange factory
Furthermore, a prominent flange factory invests in continuous training for its workforce. By staying abreast of the latest advancements in flange technology and industry regulations, the factory's engineers and technicians are able to provide solutions that are both innovative and compliant. This emphasis on professional development ensures that the factory remains at the forefront of the industry, offering products that integrate seamlessly into complex industrial systems.
From a logistical standpoint, a flange factory's efficiency in production and distribution significantly enhances its trustworthiness. The ability to maintain consistent production timelines and offer global shipping solutions reflects the factory's commitment to customer satisfaction. Additionally, a comprehensive after-sales service that includes installation support and troubleshooting advice further solidifies the factory's reputation as a reliable partner in the supply chain.
In conclusion, a flange factory embodies a synthesis of experience, expertise, authoritativeness, and trustworthiness. Through meticulous material selection, advanced manufacturing techniques, stringent quality assurance, and a commitment to continuous improvement, flange factories produce components that are fundamental to the industrial sector. For industry professionals and businesses seeking dependable and high-performance flange solutions, choosing the right factory is a strategic decision that impacts the overall efficacy and safety of their operations.