In the intricate world of industrial engineering and construction, flanges play a crucial role in connecting pipes, pumps, valves, and other equipment to form a robust piping system. Understanding the various flange types and sizes is essential for ensuring successful project outcomes and operational safety.
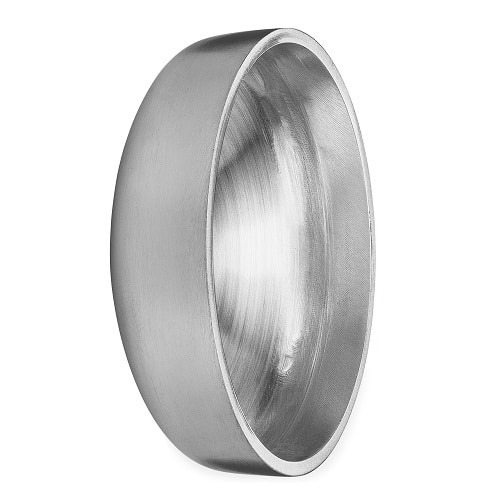
Flanges come in a broad array of designs, each serving specific functions tailored to project requirements. The material selection, pressure and temperature ratings, and specific applications determine which type of flange is suitable for a job. This expertise not only maximizes efficiency but also ensures adherence to industry standards and safety regulations.
Slip-On Flanges are prevalent in low-pressure applications due to their cost-effectiveness and ease of installation. These flanges slip over the pipe and are welded both inside and outside to increase strength and prevent leakage. However, they are not recommended for high-pressure environments because they may not withstand high stress.
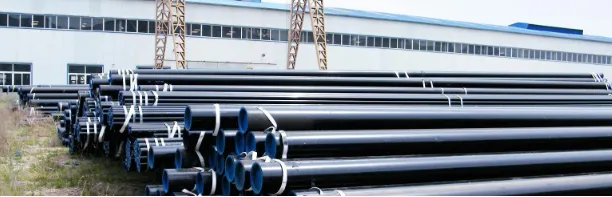
Weld Neck Flanges, identifiable by their protruding neck, offer robustness in high-pressure and high-temperature scenarios. The neck design ensures the gradual transition of stress, enhancing overall strength and reliability. This attribute makes them ideal for critical applications such as refineries, processing plants, and shipbuilding.
Blind Flanges are essential for terminating pipe ends or nozzles that are not in use. They provide easy access for inspection and maintenance within piping systems, which is crucial for ensuring operational safety. Expertise in blind flange application ensures that systems can be sectioned off or brought online without significant disruption.
Socket Weld Flanges are designed for small-diameter, high-pressure applications. These flanges are prized for their strength, as they allow a seamless surface and are typically used in chemical processing applications. It’s important to weld correctly to avoid potential crevice corrosion, showcasing the need for expert installation.
flange types and sizes
Lap Joint Flanges are used in conjunction with stub ends and are commonly applied in systems where frequent inspection or dismantling is required. They allow for easy rotation to provide alignment with bolts and facilitate convenient maintenance without needing to cut the pipe.
Threaded Flanges are unique because they can connect pipes without welding. This makes them popular in environments where the use of a flame is dangerous. Their ease of installation highlights the advantage of utilizing experienced technicians in environments where safety is paramount.
Understanding flange sizes is critical as it affects seamless integration into existing systems. Flange sizes define the diameter of connected pipes and must be precisely matched to ensure airtight seals. The North American industry often follows ANSI/ASME standards that specify dimensions such as nominal diameter and thickness, alongside pressure classes ranging from 150 to 2500.
A professional approach entails accurate sizing through advanced measuring techniques and alignment tools. This is crucial to prevent issues like misalignment or leakage due to improperly sized flanges. In the competitive industrial market, clear insight into these specifics significantly boosts operational efficiency and reduces the chance of costly downtime.
Trustworthy suppliers and manufacturers are indispensable resources in obtaining quality flanges. They provide valuable documentation, such as material test reports and pressure ratings, ensuring that the components meet project specifications and regulatory standards. Engaging with certified suppliers not only guarantees product quality but also builds confidence with stakeholders who demand reliability and safety assurances.
To thrive in industries relying on seamless and high-pressure systems, extensive knowledge and practical expertise in flange types and sizes are indispensable. Through experience-backed decisions and authoritative resources, businesses can achieve superior operational performance, reduced system failures, and safe work environments. While flange installation may appear straightforward, its impact on system integrity is profound and demands experienced oversight. With continued advancements in industrial standards, staying informed and embracing expert guidance in flange selection and application is more vital than ever.