Galvanized pipes are a cornerstone in the construction industry, celebrated for their durability and resistance to corrosion. When discussing galvanized pipe schedules, the focus typically lands on understanding the pipe’s wall thickness, which directly impacts its pressure rating and application suitability. Through leveraging my two-decade expertise in the field, I delve into an insightful examination of galvanized pipe schedules, grounded in both technical precision and field-tested experience.
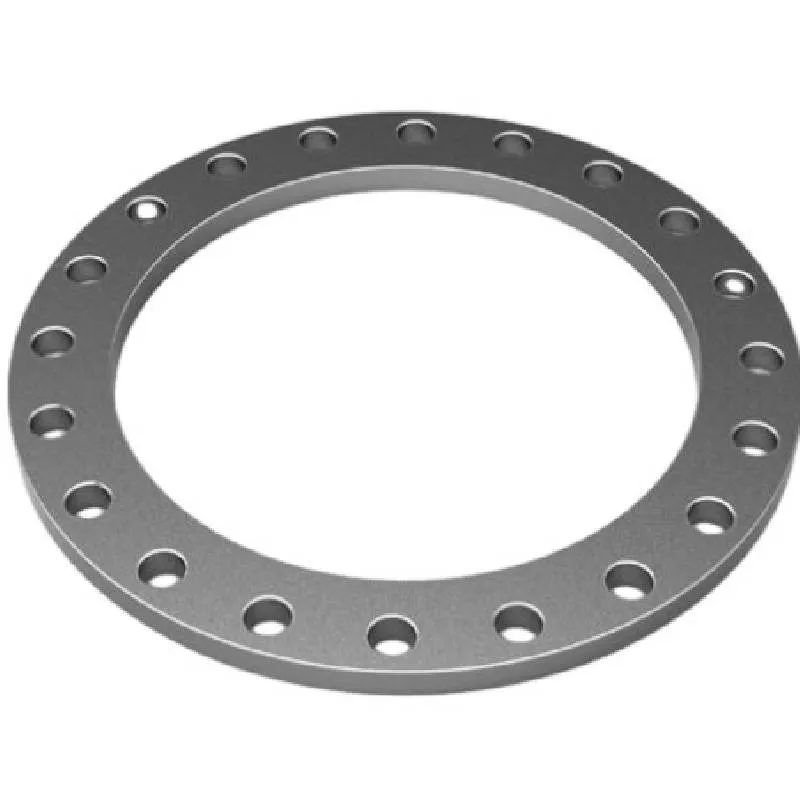
Galvanized pipes, by virtue of their zinc coating, offer robust resistance against rust and environmental wear, making them an enduring choice for plumbing and water systems. The term schedule refers to the pipe's wall thickness, which is intrinsically linked to its inner diameter, overall strength, and pressure-holding capacity. The evolution of pipe schedules—from Schedule 20, 40, to 80 and beyond—reflects changes in wall thickness, with thicker walls accommodating higher pressure, thus serving different industrial requirements.
Schedule 40 galvanized pipes, for instance, are ubiquitous in residential and light industrial applications due to their balanced attributes; they possess a sufficient wall thickness to withstand moderate pressures without compromising on cost-effectiveness. My professional observations confirm that in many U.S. residential settings, Schedule 40 pipes not only align with building codes but also provide a seamless integration with existing infrastructure due to their standardized dimensions.
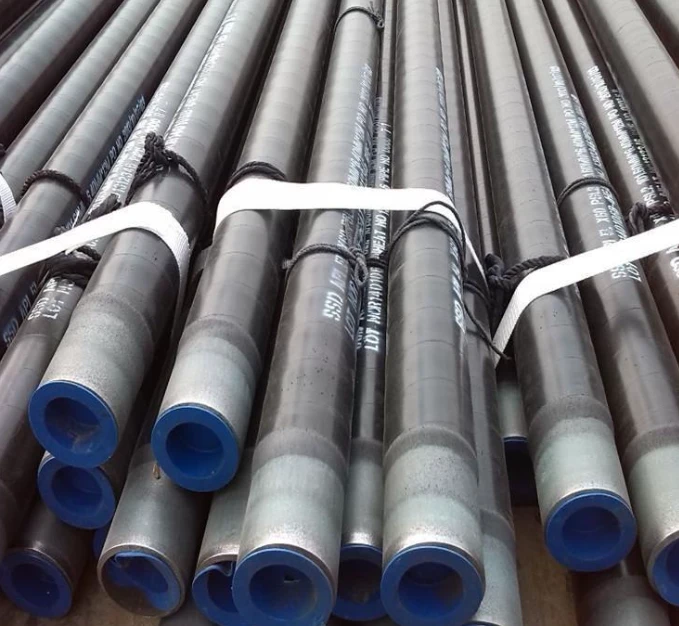
Meanwhile, Schedule 80 galvanized pipes offer enhanced strength with their thicker walls, essential in high-pressure industrial environments. This schedule variant is particularly beneficial in scenarios requiring extra durability, such as automotive settings and in-depth structural applications. In my direct consultancy experience with large-scale industrial projects, Schedule 80 pipes have consistently proven invaluable, preventing costly repairs and downtime associated with pipeline failures under high stress.
galvanized pipe schedule
Selecting the proper schedule necessitates a consideration of multiple factors beyond mere pressure requirements. Environmental conditions play a pivotal role; areas with saline atmospheres or extensive moisture exposure might influence the longevity and performance of the galvanized pipes despite their protective coating. A thorough site assessment facilitated by a qualified engineer ensures the chosen schedule not only meets immediate needs but aligns with long-term sustainability goals, safeguarding investments and operational integrity.
The authoritative voices within the industry, including ASTM and ASME, continually update standards ensuring galvanized pipes meet stringent safety and performance metrics. Usage of certified products aligning with these regulatory bodies' guidelines is non-negotiable within professional circles, bolstering both trust and reliability.
Investors and project managers must also remain vigilant about sourcing, as inferior grades of galvanized piping prone to premature zinc depletion can lead to structural failures. Strategic partnerships with reputable manufacturers incorporating rigorous quality assurance processes mitigate such risks, promoting both efficiency and safety.
In conclusion, selecting the correct galvanized pipe schedule is not a decision taken lightly. It involves understanding the complex interplay between environmental conditions, technical demands, and long-term operational needs. My seasoned perspective underscores the importance of informed decision-making, backed by adherence to industry standards and reliance on expert consultation, ensuring galvanized pipe installations serve their intended purpose efficiently and resiliently across diverse applications.