Socket weld pipe fittings are a critical component in piping systems, renowned for their leak-proof joints and structural integrity, making them indispensable in high-pressure and combustible applications. Unlike threading or other forms of connection, the socket weld fitting system involves inserting a pipe into a recessed area of the fitting, creating a welded seal. This method enhances the overall strength of the piping assembly, making it ideal for a range of industrial processes.
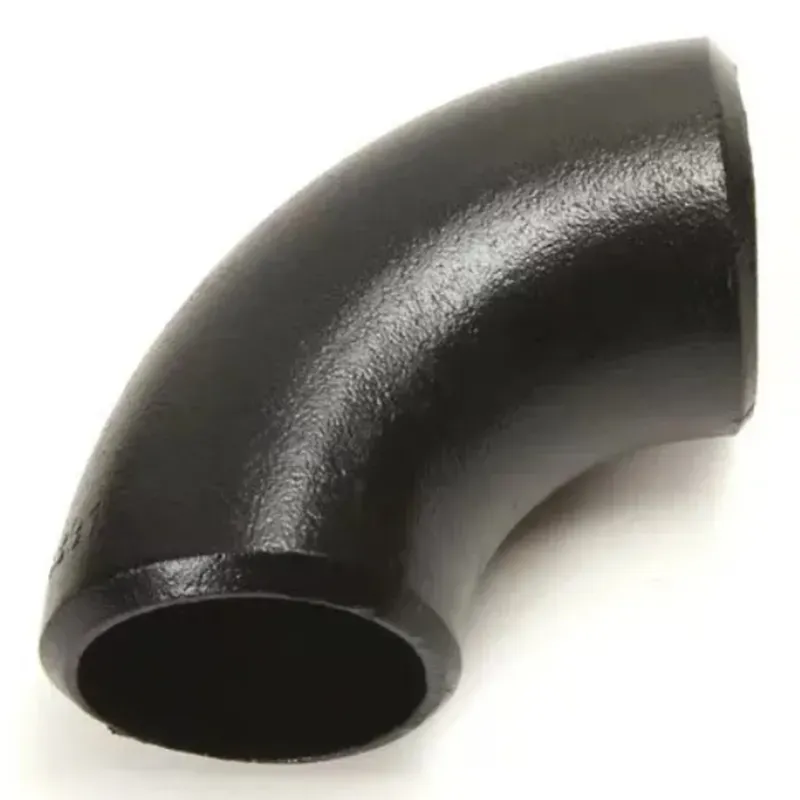
The primary advantage of socket weld pipe fittings lies in their robust nature. When employed in industries such as oil and gas, petrochemical, and power generation, they provide the durability and resilience required to withstand high pressure and temperature fluctuations. The welding process ensures a seamless junction, minimizing the risk of leaks, which is a significant concern in environments handling volatile or hazardous substances.
One of the most compelling experiences shared by industry professionals is the ease of installation associated with socket weld fittings. The design aids in precise alignment, which is crucial during the welding process. Installers appreciate the less restrictive nature of these fittings compared to other welded connections, allowing for more flexibility in tight spaces. Experts often recommend socket weld fittings for piping systems with small diameters, where precision and reliability are paramount.
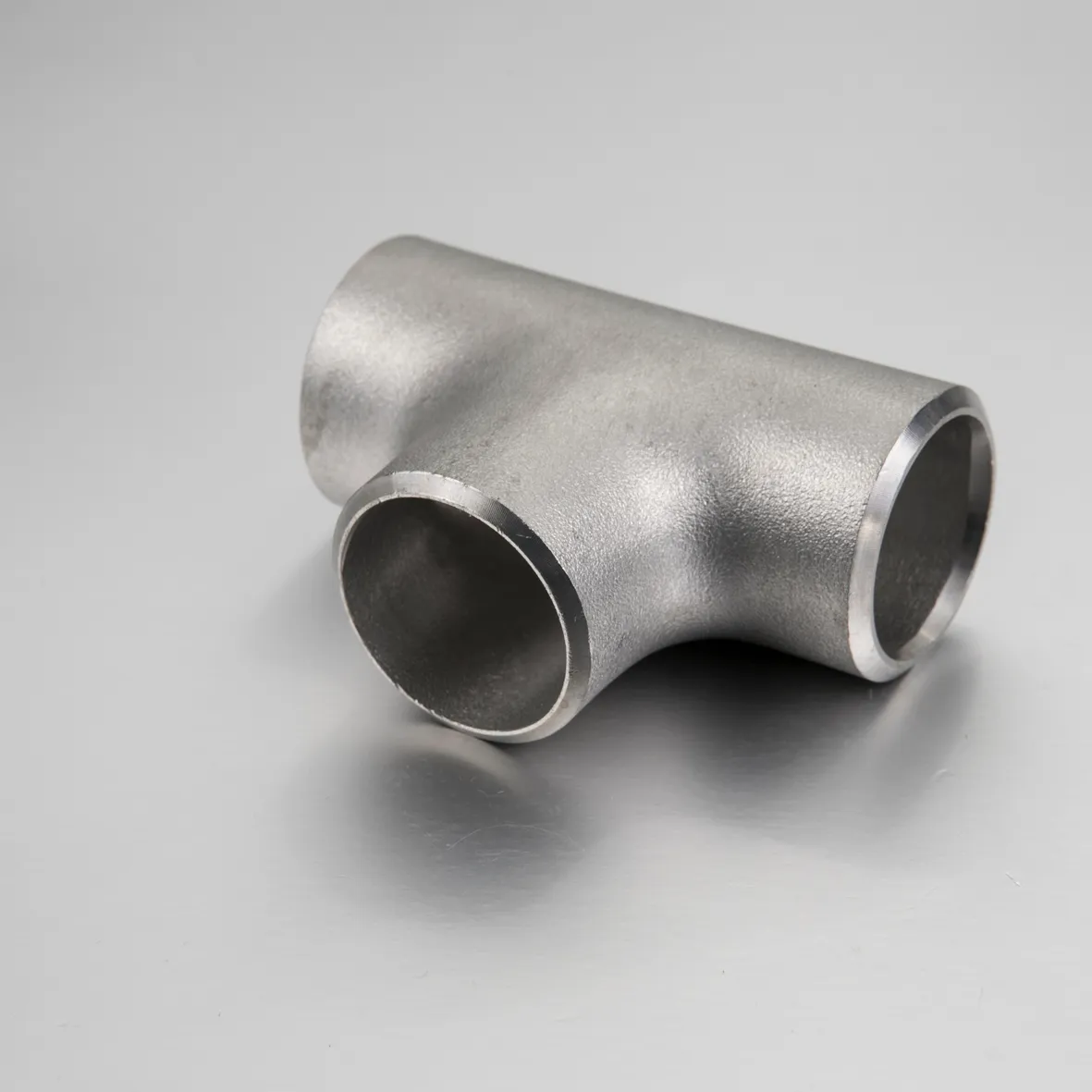
From an expertise standpoint,
the production of socket weld fittings demands high standards. Manufacturers utilize high-grade materials such as stainless steel, carbon steel, and alloy steel, ensuring they meet stringent industry specifications like ASME standards. This adherence to quality not only confirms their suitability for high-pressure applications but also their longevity in service, reducing the need for frequent replacements and, consequently, maintenance costs.
socket weld pipe fitting
In terms of authoritativeness, socket weld pipe fittings have consistently demonstrated their efficacy in various critical applications. Organizations like the American Society of Mechanical Engineers (ASME) and the American National Standards Institute (ANSI) provide guidelines and specifications, which serve as benchmarks for these fittings. Following these standards assures that the fittings possess the necessary attributes to perform reliably under demanding conditions. Industry certifications and compliance with internationally recognized standards reinforce the trust placed in them by engineers and project managers globally.
Trustworthiness in utilizing socket weld fittings is further bolstered by their performance in real-world applications. They are known for their ability to withstand thermal cycling, preventing structural failures that could lead to operational downtimes. The welding process also alleviates crevice corrosion risks, as there are fewer crevices for corrosive substances to reside. This feature is particularly beneficial in chemical processing and offshore applications, where corrosion resistance is a primary concern.
In conclusion, socket weld pipe fittings offer a combination of strength, reliability, and adaptability, making them a preferred choice in critical industrial systems. Their ease of installation, conformance to high manufacturing standards, and proven track record in performance underscore their credibility and appeal to professionals aiming to build efficient and safe piping infrastructures. For those looking to implement a robust and leak-proof solution in their piping designs, socket weld fittings represent an authoritative and trustworthy choice.