Flanges play a vital role in the oil and gas industry, providing reliable connections for pipelines, valves, and other equipment. The variety in their design, material, and functionality is essential to address the specific challenges encountered in this field, such as high pressures, extreme temperatures, and corrosive environments. Understanding the different types of flanges and their applications can significantly enhance operational safety and efficiency.
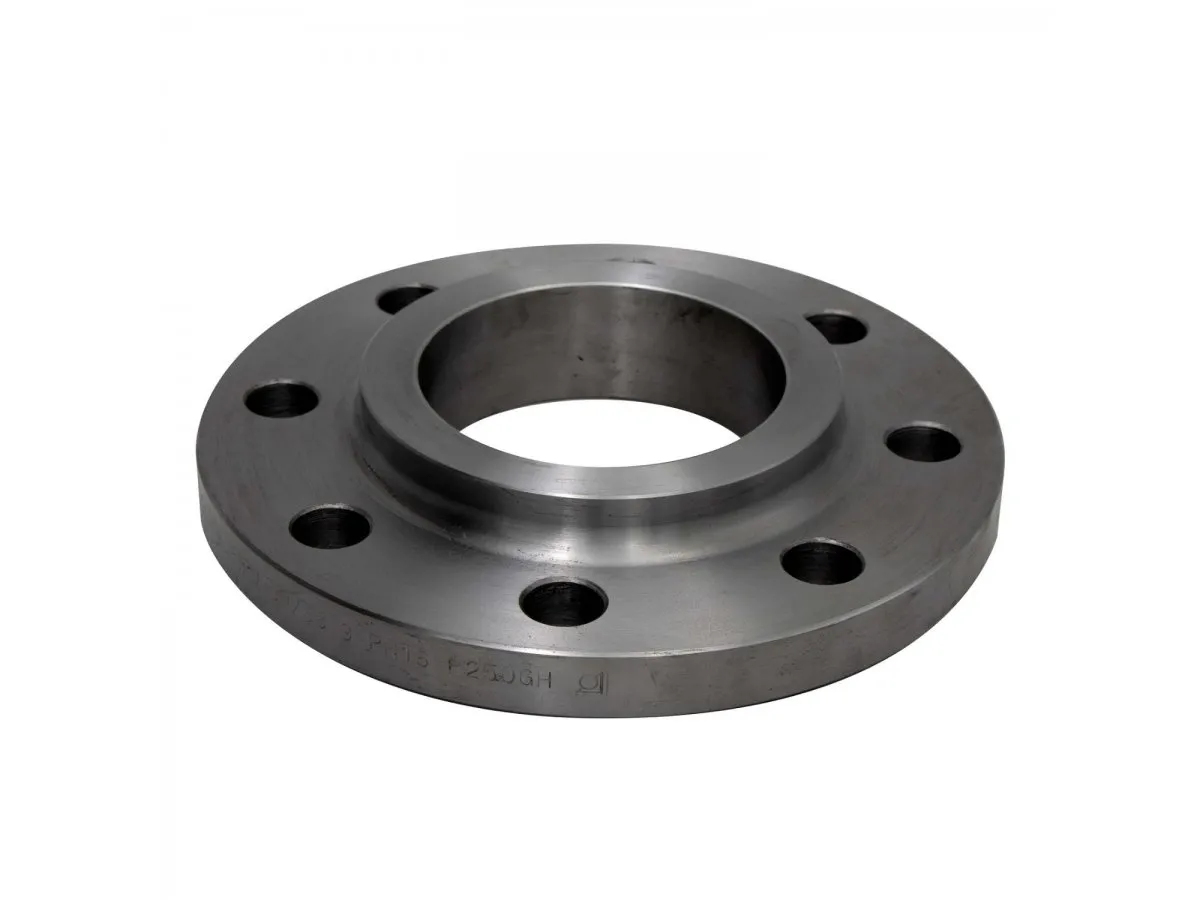
Weld Neck Flanges
Weld neck flanges are renowned for their ability to withstand extreme conditions. They feature a long, tapered hub that provides reinforcement, reducing stress at the flange base. This design is particularly advantageous in environments subject to high pressures and variable temperatures. The welding process ensures a strong, leak-proof connection to the pipeline, making this flange type a preferred choice for critical applications where safety is paramount.
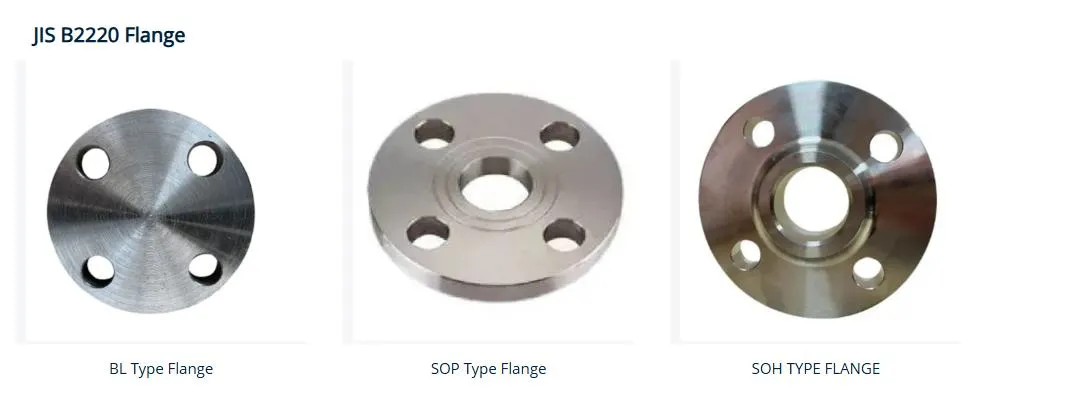
Slip-On Flanges
Slip-on flanges are praised for their ease of installation and cost-effectiveness. Unlike weld neck flanges, slip-on flanges are designed to slip over the pipe.
A fillet weld at the flange's inside and outside diameters ensures a secure connection. While they may not offer the same strength as weld neck flanges, their simplicity and lower cost make them ideal for low-pressure applications where the demands on the piping system are less severe.
Socket Weld Flanges
Socket weld flanges are engineered for high-pressure applications and offer a smooth bore for unrestricted flow. The pipe is inserted into the flange's socket end and fillet welded at the hub, resulting in a strong and durable joint. This type of flange is particularly suitable for small-diameter, high-temperature piping systems, where its design minimizes leakage and provides a clean transition from the pipe to the flange.
Blind Flanges
Blind flanges are used to seal off or close the end of a piping system, valves, or pressure vessel openings. They do not have a bore and are essential for maintenance and inspection of pipelines. These flanges can withstand high pressure and temperature and are often used as a cover to test the flow of gases or liquids through a pipeline. Blind flanges ensure the integrity and safety of a system by allowing for thorough inspection and maintenance.
types of flanges in oil and gas
Lap Joint Flanges
Lap joint flanges are used in systems that require frequent dismantling for inspection or cleaning. These flanges are not welded or fixed to the pipe; instead, the pipe end is fitted with a stub end, and the flange piece is free to rotate around it. This allows for quick assembly and disassembly without the need for persistent alignment adjustments. Lap joint flanges are ideal for systems that undergo regular maintenance and in applications where space constraints require flexible pipe layouts.
Threaded Flanges
Threaded flanges, also known as screwed flanges, feature a female thread within the bore that matches the male thread of the piping. This design makes them easy to install without the need for welding, making them particularly useful in high-pressure, non-corrosive environments. They are most commonly used in small-diameter piping systems where welding is hazardous or impractical.
Integral Flanges
Integral flanges are an intrinsic part of the equipment or the pipe and are forged directly from the material. They provide excellent strength and rigidity, making them suitable for high-pressure and high-temperature applications. Integral flange designs eliminate the need for separate joining parts, thus reducing the points of possible failure and ensuring better overall system integrity.
Conclusion
Selecting the appropriate flange type is crucial for ensuring the safety, reliability, and efficiency of oil and gas operations. Each flange type offers distinct advantages adapted to specific conditions and industrial needs, from the robust weld neck flanges to the flexible lap joint flanges. Understanding these distinctions and their applications underlines not only technical expertise but also emphasizes a commitment to maintaining the high standards expected in this demanding industry. As technology evolves, so too will the materials and designs of flanges, offering ever-more sophisticated solutions to meet the dynamic challenges of the oil and gas sector.