In the intricate world of industrial piping systems, flanges play a critical role in ensuring reliable and efficient operations. As an essential component, flanges allow for the connection of pipes, valves, pumps, and other equipment, forming a robust pipeline network. Understanding the different types of flanges is crucial not only for optimizing system design but also for maintaining safety standards and operational efficiency.
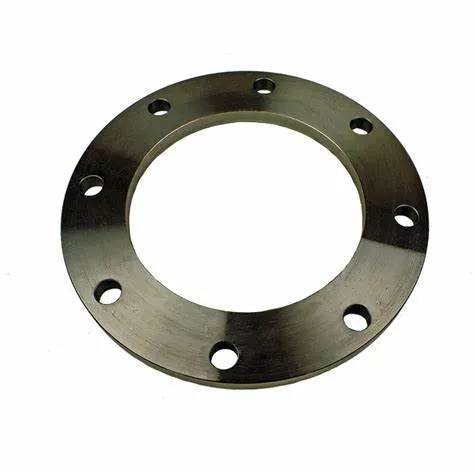
Flanges come in various types, each serving distinct functions and purposes within a piping system. The selection of the appropriate flange type can significantly influence the performance and durability of the system. Here, we delve into the most prevalent flange types, dissecting their unique characteristics and applications, supported by expert insights and industry experience.
1. Weld Neck Flanges Known for their high-strength connection, weld neck flanges are ideal for high-pressure and high-temperature applications. These flanges feature a long tapered hub that reinforces the flange, allowing it to withstand excessive bending forces. They are widely used in petrochemical and oil pipeline systems where safety and reliability are paramount. Expertise dictates careful installation to avoid alignment issues that could compromise the system integrity.
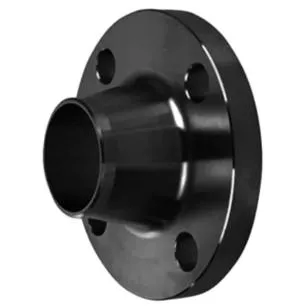
2. Slip-On Flanges Favoured for their ease of assembly, slip-on flanges are designed for low-pressure applications. They slip over the pipe and are welded both inside and outside to provide sufficient strength. Despite being cost-effective, their load-bearing capacity is lesser compared to weld neck flanges. Therefore, they are predominant in applications where cost-efficiency and moderate pressure management are key, as seen in water treatment and refrigeration plants.
3. Blind Flanges Utilized to cap off a pipeline, blind flanges serve to terminate a system or facilitate future extensions and inspections. They do not have a bore, making them suitable for high-pressure containment, such as in boiler systems and shipbuilding. Expertly engineered for leak-proof seals, blind flanges ensure system reliability and operator safety.
4. Socket Weld Flanges Ideal for high-pressure, small-diameter applications, socket weld flanges provide a more secure and leak-resistant connection compared to slip-on flanges. They feature a socket in which the pipe is inserted and then fillet welded. This flange type is extensively used in chemical processing industries where tight seals are crucial to prevent hazardous leaks.
types of flanges used in piping
5. Lap Joint Flanges Known for flexibility and ease of alignment, lap joint flanges are suitable for systems requiring frequent disassembly. These flanges comprise a stub end that is welded to the pipe,
with the flange loose behind it. Their design is particularly beneficial for systems involving costly or exotic materials, as they allow the reuse of flanges with different stub ends.
6. Threaded Flanges These flanges are distinguished by a tapered thread, which is closely compatible with similarly threaded pipes. Predominantly used in low-pressure applications, they do not require welding, making them suitable for explosive atmospheres where welding is hazardous. Threaded flanges find their prominence in the plumbing industry where simplicity and safety are prioritized.
7. Orifice Flanges Essential for flow measurement applications, orifice flanges are employed alongside orifice meters. They incorporate tapping holes to facilitate pressure measurements and are a critical component in oil and gas pipelines where accurate flow data is indispensable. Industry experts highlight their importance in optimizing energy consumption and enhancing the operational efficiency of a system.
Selecting the right flange type requires a comprehensive understanding of the system’s operational demands, pressure, temperature conditions, and material compatibility. Consulting with seasoned professionals and adhering to industry standards is essential to ensure the best outcomes. This informed approach not only boosts system performance but also fortifies trust with stakeholders through enhanced safety and reliability.
In conclusion, the diverse types of flanges used in piping cater to various industrial needs, each offering specific advantages tailored to particular applications. While cost and ease of installation may drive some choices, the long-term benefits of durability, safety, and performance should guide the final decision. By leveraging industry expertise and trustworthy practices, businesses can optimize their piping systems for the challenges and demands of modern industry.