Welding steel pipes together requires both skill and understanding of the materials involved to ensure a strong, reliable connection. Steel pipes find applications across numerous industries, from construction to manufacturing, where efficient and seamless joints are critical.
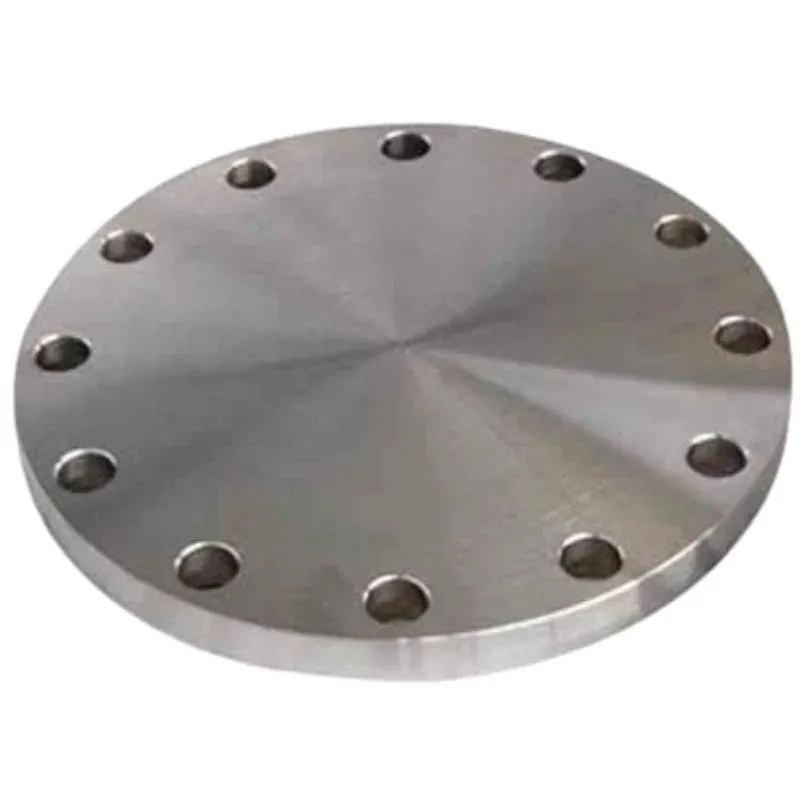
A crucial first step in welding steel pipes is to understand the properties of the steel being used. Different steel grades have varying levels of carbon and alloy content, which affect their weldability. Low-alloy steels are typically easier to weld, while high-carbon steels may require preheating to prevent cracking or other weld defects. Therefore, always consult the specific material data sheets for guidance on the best welding practices for the particular type of steel you're working with.
Once you have an understanding of the material, selecting the appropriate welding technique is essential. Shielded Metal Arc Welding (SMAW), also known as stick welding, is a prevalent choice for welding steel pipes due to its versatility and ease of use in different environments. It is particularly beneficial for outdoor projects where wind could affect gas-shielded welding processes.
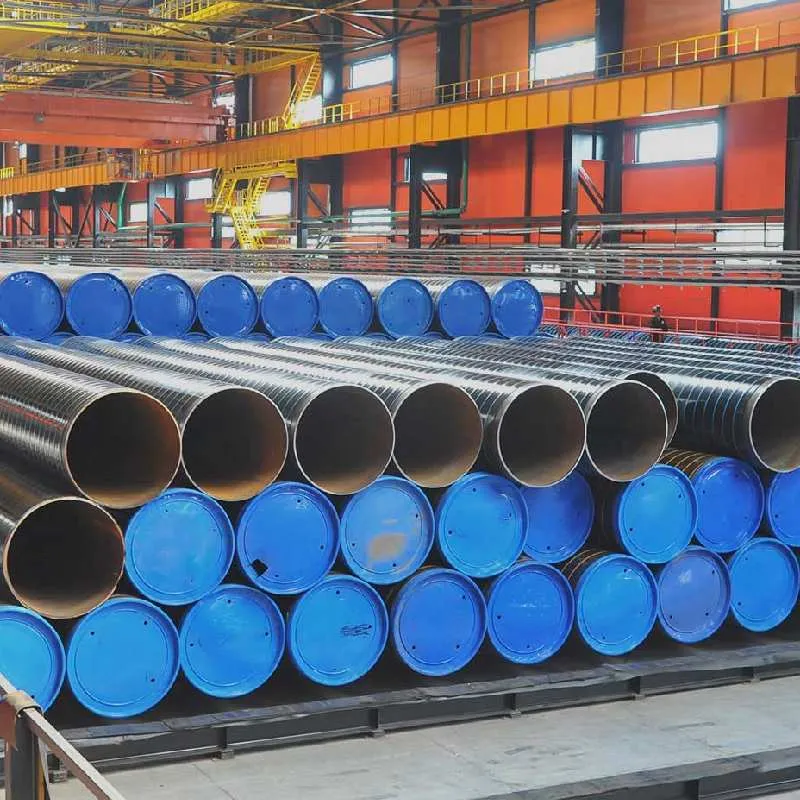
Gas Tungsten Arc Welding (GTAW) or TIG welding is another favored method, especially for high-precision tasks, as it allows for superior control over the weld pool and produces high-quality, clean welds. Although it requires more coordination and skill, the results are often worth the effort for tasks demanding high aesthetic values or critical structural integrity.
Preparation of the steel pipes is a pivotal aspect that cannot be overstated. Start by cleaning the pipe ends thoroughly to remove any rust, dirt, or oil that can obstruct the welding process and weaken the final joint. Align the pipes correctly and use clamps to hold the pieces in perfect position during welding, which is essential for achieving a uniform weld bead and reducing the risk of defects.
Preheating the steel can be an advantageous step for certain types of steel, such as those with high carbon content. Preheating helps reduce thermal stress, minimizes the risk of cracking, and ensures even penetration throughout the welding process. Monitoring the cooling rate post-welding is equally important to avoid rapid cool-downs, which might lead to brittleness.
welding steel pipe together
Another important consideration is choosing the correct filler material. The compatibility of the filler metal with the pipe material directly impacts the mechanical properties of the weld. Always consult AWS (American Welding Society) guidelines to select the appropriate filler rod or electrode that matches the base metal in composition and strength.
Furthermore, one cannot overlook the importance of a skilled welder. The expertise of the welder affects the quality of the weld significantly. A well-trained welder understands the intricacies of controlling weld puddles, adjusting current settings, and dealing with varying pipe diameters and thicknesses.
Quality control and inspection are the final steps in ensuring a successful welding operation. Non-destructive testing methods such as ultrasonic testing, radiography, and magnetic particle inspection can be utilized to detect potential internal flaws or weaknesses in the weld. Regular inspection helps in catching defects early, thereby ensuring the longevity and safety of the steel pipe system.
To build trust with stakeholders and ensure compliance with industry standards, documentation throughout the welding process is vital. Keeping detailed records of material certifications, welding procedures, and inspection results demonstrates adherence to best practices and builds confidence in the quality of the work.
Welding steel pipes seamlessly combines scientific knowledge with skilled craftsmanship. Each project offers unique challenges and requires a tailored approach to overcome them. Staying informed about the latest technologies and continuously refining skills not only enhances the welding process but also aligns with the principles of Experience, Expertise, Authoritativeness, and Trustworthiness. While the demand for welded steel pipes remains strong, excelling in this field means never compromising on quality or safety, two cornerstones of long-lasting structural integrity.