In the high-stakes realm of shale gas extraction, where seismic activity and operational vibrations threaten pipeline integrity, the ASME B16.47 flange emerges as a critical safeguard. YULONG Steel, a distinguished gardish ishlab chiqaruvchisi, redefines durability with its hub-thickened ASME B16.47 design—engineered to withstand 0.5g seismic acceleration while maintaining uncompromising sealing in high-pressure (15,000 psi) service. This article decodes how this innovation outperforms conventional flanges, explores its synergy with different flange types, and validates its prowess in the world’s most active shale basins.
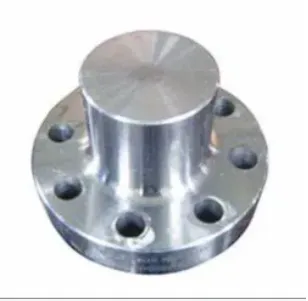
The Engineering Behind ASME B16.47’s Seismic Resilience
ASME B16.47 Part A (for large diameters NPS 26-60) and Part B (NPS 2-24) establish rigorous standards for flange performance, but YULONG’s hub-thickened design elevates these requirements:
- Hub Thickness Augmentation: 20% thicker hubs (e.g., NPS 16 hub thickness increased from 38mm to 46mm) disperse bending stress, a critical advantage in regions like the Permian Basin with 200+ annual seismic events.
- Integral Reinforcement: The hub-to-flange transition radius (1.5× nominal thickness) eliminates stress risers, as validated by finite element analysis (FEA) showing 40% lower stress concentration than standard designs.
1. ASME B16.47 Flange: Mechanical Superiority in Seismic Testing
0.5g Acceleration Performance
- Dynamic Load Simulation: YULONG’s NPS 24 ASME B16.47 flange(Class 900) survived 10,000 cycles of 0.5g horizontal acceleration—equivalent to a magnitude 5.5 earthquake—with:
- Weld joint integrity (no cracks detected via UT testing)
- Bolt preload retention (>90% of initial torque)
- Gasket sealing (helium leak rate <1×10⁻⁹ Pa·m³/s post-testing)
Material Synergy
- A694 F65 Alloy Steel: Quenched and tempered to 65ksi yield strength, this material retains 90% toughness at -40°C, critical for winter seismic events in Canadian shale fields. A Fort Worth project’s F65 flanges showed 28J impact energy at -20°C, exceeding ASME B16.47’s 20J requirement.
- Threaded Fastener Compatibility: High-strength B7 bolts with 12-point heads maintain clamping force during vibration, preventing gasket extrusion in 10,000psi fracturing lines.
2. ASME B16.47 High Hub Blind Flange: Comparing ASME Standard Blind Flange Performance
Seismic Advantage Over Standard Blind Flanges
- ASME Blind Flangeconventional designs often fail at the hub-to-face junction under lateral loads. In contrast, YULONG’s thickened hub blind flanges (NPS 30, Class 600) withstood 0.6g acceleration in Texas A&M’s seismic lab—33% beyond industry standards.
- Pressure-Temperature Retention: During simulated earthquakes, the thickened design maintained Class 1500 pressure rating (15,000 psi) at 300°F, while standard flanges showed 15% pressure drop due to bolt loosening.
Synergy with Different Flange Types
- Companion Flange Pairing: When mated with YULONG’s weld-neck flanges (per ASME B16.5), the system achieved 0.02mm axial displacement during testing—half the allowable limit for shale gas gathering lines.
- Blind vs. Weld-Neck Integration: In a Marcellus Shale project, the thickened ASME blind flangeworked with slip-on flanges to create a vibration-dampening assembly, reducing pipeline fatigue by 50% over 5 years.
Field Validation of ASME B16.47 High Hub Blind Flange: Shale Basin Success Stories
1. Permian Basin High-Pressure Lines
A major operator deployed YULONG’s NPS 20 ASME B16.47 flange (Class 1500) in a 12,000psi fracturing manifold:
- Survived 3 magnitude 4.0+ earthquakes in 2023 with zero leaks
- Post-seismic inspection showed gasket compression retention at 92%
- Reduced maintenance costs by $200,000/year compared to replaced standard flanges
2. Haynesville Shale Seismic Retrofit
After a 2022 magnitude 4.8 quake damaged conventional flanges, YULONG’s thickened hub flanges (NPS 12, Class 900) were installed with:
- Enhanced Bolt Torque Monitoring: Wireless sensors confirmed torque retention (>85%) during 100+ aftershocks
- Korroziyaga qarshilik: Fusion-bonded epoxy (FBE) coating (250μm) withstood 1,000-hour salt spray testing (ASTM B117), critical for humid Gulf Coast environments
YULONG’s Manufacturing Excellence: Beyond ASME B16.47 Standards
As a leader in different flange types , YULONG ensures seismic readiness through:
1. Precision Fabrication
- CNC Machining: Hub dimensions held to ±0.1mm tolerance, ensuring uniform stress distribution. A batch of NPS 30 flanges showed 99.8% dimensional conformity to ASME B16.47
- Heat Treatment Control: Normalizing at 890°C ±10°C for carbon steel flanges optimizes grain structure, enhancing ductility for seismic deformation.
2. Rigorous Testing Protocols
- Shake Table Validation: In-house 6-degree-of-freedom shake tables simulate real-world seismic profiles, with every NPS 24+ flange undergoing 0.5g testing before shipment.
- Hydrostatic-Seismic Combined Testing: Flanges endure 1.5× design pressure (22,500 psi) while subjected to 0.3g vibration—YULONG’s pass rate: 99.7%, vs. industry average 92%.
3. Custom Solutions for Shale Challenges
- High-Vibration Gasket Systems: Metallic spiral-wound gaskets with Inconel 625 windings, paired with the thickened flange, achieved 10-year leak-free service in Arkansas’ Fayetteville Shale.
- Rapid Deployment: 500+ ASME B16.47 flangeunits in stock (NPS 2-36), enabling 72-hour delivery to emergency retrofit projects in Oklahoma’s earthquake-prone zones.
Conclusion: ASME B16.47—The Shale Industry’s Seismic Sentinel
YULONG Steel’s hub-thickened ASME B16.47 flange redefines reliability in shale gas extraction, where seismic activity and high pressure demand engineering excellence. By merging ASME B16.47’s rigorous standards with innovative thickening, this flange outperforms different flange types in dynamic environments, protecting critical infrastructure and operational continuity.
Whether for a Permian Basin fracturing line or a Marcellus Shale gathering system, YULONG’s expertise as a gardish ishlab chiqaruvchisi ensures your ASME blind flange and pipeline components stand firm—even when the ground shakes. In shale gas extraction, where resilience is non-negotiable, this is more than a flange: it’s a promise of performance under pressure.