The world of piping and plumbing solutions hinges greatly on the quality and reliability of its components, with the stainless steel blind flange being a standout piece. Navigating the selection and utilization of stainless steel blind flanges demands an understanding rooted in real-world experience and industry expertise.

When it comes to installing blind flanges, experience speaks volumes. Professionals who have spent years in the field recognize that these components serve a crucial role in sealing the ends of piping systems. This is essential for maintenance purposes, pressure testing, and ensuring that no foreign substances infiltrate the system. The process of installing a blind flange might sound straightforward, but ensuring a perfect fit requires precision and a high level of skill. A seasoned expert would understand any pipe's nuances and idiosyncrasies, making necessary adjustments with ease and efficiency.
Blind flanges made from stainless steel are renowned for their durability and resistance to corrosion. Unlike other materials, stainless steel can withstand extreme temperatures and pressures, a testament to its versatility and strength. Specialists in materials science advocate for stainless steel due to its impeccable performance in harsh environments, such as offshore drilling or chemical processing plants. This material's anti-corrosive properties are a result of the chromium content, which forms an invisible layer on the surface that prevents rust and damage.
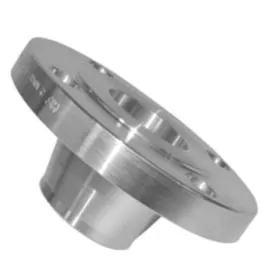
Industry specialists often emphasize the importance of selecting the appropriate blind flange for specific applications. This is where expertise in flange types and specifications becomes indispensable. Stainless steel blind flanges come in numerous grades, each tailored for a particular pressure rating or temperature range. For example, the ASME standards outline various pressure classes (such as 150, 300, 600, etc.) that correspond to the flange's intended use. Those trusted in the industry will often guide their clients in choosing the right flange based on these criteria, ensuring maximum safety and long-term performance.
stainless steel blind flange
Reputation and authority in the field of flange manufacturing are crucial. The best manufacturers are often those with decades of experience and a track record of quality assurance. They are involved in continuous research and development, pushing the boundaries of material science and production techniques. This pursuit of excellence is what separates credible manufacturers from those of less repute. Industry leaders are typically accredited by several standards organizations, ensuring that their stainless steel blind flanges meet and exceed global quality norms.
Having trust in your components is non-negotiable. Businesses and engineers put their faith in components knowing that they can trust their performance under pressure, literally and metaphorically. Trust in blind flanges stems from rigorous testing and quality control procedures that reputable manufacturers employ. These tests simulate real-world conditions and pressures, providing end-users with confidence in the product's reliability and safety.
Informed decision-making in selecting stainless steel blind flanges is enhanced by leveraging digital resources and consultations with experts. Online databases and technical sheets provide essential information on dimensions, material properties, and compatibility. Additionally, engaging with seasoned professionals during the purchasing process can yield insights and recommendations that align with project-specific requirements.
In summary, stainless steel blind flanges are more than just piping components—they are a blend of robust material science, engineering expertise, and industry authority. They embody the ideal trifecta of durability, precision, and dependability, making them indispensable to any piping infrastructure. For those seeking to ensure the utmost in quality and performance, trusting in established experts and manufacturers not only safeguards their investment but underscores a commitment to excellence in engineering.