When considering industrial applications, choosing the right flange for your projects is crucial. The 2 inch flange stands out as a key component, offering adaptability and durability across various uses. This article delves into the practical applications, material considerations, and installation tips for a 2 inch flange, providing insights based on extensive industry experience and expertise.
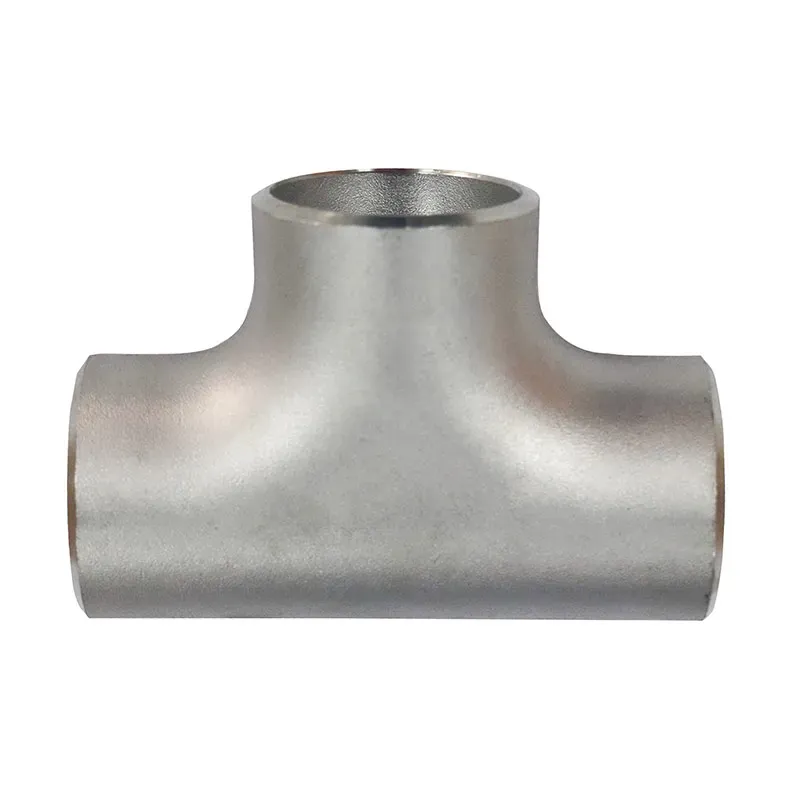
One of the primary reasons the 2 inch flange is widely used is its optimal size, which offers a balance between compactness and structural capacity. This makes it ideal for medium-sized piping systems prevalent in industries like petrochemicals, water treatment, and HVAC systems. The versatility of the 2 inch flange lies in its ability to handle substantial pressure and temperature variations, which are common in industrial environments.
Material selection is another critical factor in the performance of a 2 inch flange. Common materials include carbon steel, stainless steel, and alloy-specific compositions. Carbon steel flanges are known for their cost-effectiveness and strength, making them suitable for non-corrosive environments. Conversely, stainless steel flanges provide excellent resistance to corrosion and are ideal for systems exposed to moisture or acidic conditions. For higher temperature applications, flanges made from specialized alloys can offer enhanced strength and longevity, even under extreme conditions.
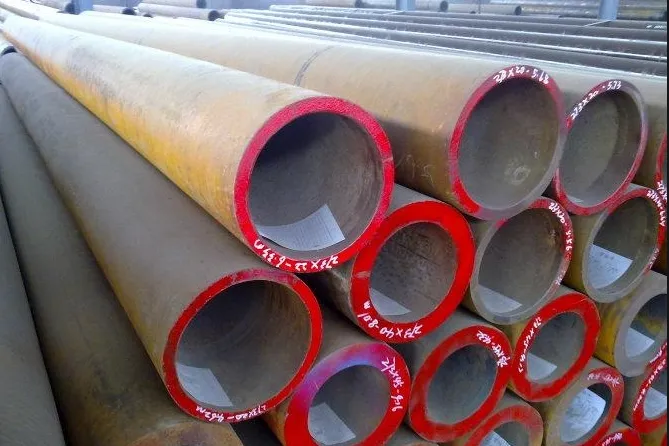
Installation of a 2 inch flange requires meticulous attention to detail to ensure system integrity and safety. Proper alignment with the adjoining pipes and components is crucial to prevent leaks and maintain optimal system performance. Utilizing a torque wrench during installation can ensure that bolts are tightened to the manufacturer's specifications, promoting an even distribution of pressure across the flange surfaces and preventing potential warping or misalignment.
Regular maintenance and inspection of flanges are necessary to extend their lifespan and avoid system failures. This includes checking for signs of wear, corrosion, or deformation, which could compromise system integrity. In industries where safety and reliability are paramount, employing non-destructive testing methods such as ultrasonic or radiographic testing can further enhance maintenance protocols, ensuring that potential issues are identified and addressed before they escalate.
2 inch flange
When selecting a 2 inch flange, it’s also essential to consider the flange type that best suits your application. The most common types include weld neck, slip-on, blind,
and socket weld flanges. Weld neck flanges are favored in high-pressure systems due to their robust welded joint with the pipe, providing durability and reducing stress concentration. Slip-on flanges, while easier to install, may not provide the same level of strength as their weld neck counterparts but are cost-effective for lower-pressure applications. Blind flanges are utilized to seal off the end of piping systems, crucial for maintenance and pressure testing, while socket weld flanges allow for a smooth bore and better fluid flow, reducing turbulence within the system.
Expertise in the field underscores the importance of considering environmental factors such as thermal expansion, vibration, and potential chemical exposure when selecting and installing flanges. These factors can significantly impact the long-term performance and safety of the piping system.
Trust in the products used in industrial applications is built through a combination of rigorous testing, adherence to industry standards, and third-party certifications. Reputable manufacturers provide documentation and certification such as ASTM or ASME compliance, offering peace of mind and assurance of quality when incorporating a 2 inch flange into your systems.
In conclusion, understanding the specifics of a 2 inch flange, from material selection to application type and installation methods, is essential for optimizing system performance and longevity. By leveraging extensive industry knowledge and focusing on quality components, engineers and industry professionals can achieve system reliability and efficiency, underscoring the indispensable role of the humble flange in industrial applications.