The world of piping solutions constantly evolves, yet the integral role that flanges play remains steadfast. Among these, the 4-inch flange stands prominently as a versatile and indispensable component in various industrial applications. Drawing from an extensive reservoir of experience and technical expertise, let's explore why 4-inch flanges are pivotal, their technical specifications, and how to ensure optimal performance and reliability.
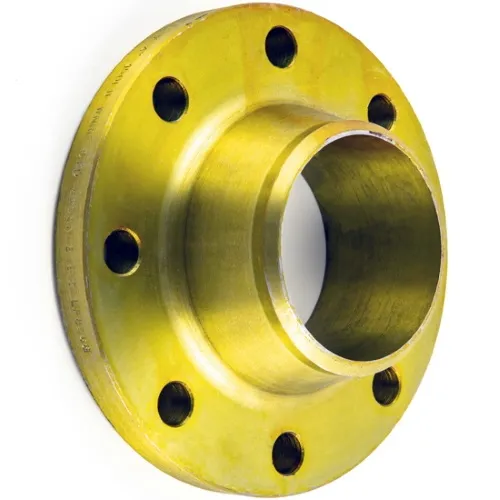
At the forefront of pipeline management systems, 4-inch flanges serve as a critical junction for joining pipes, valves, and other equipment. Their solid construction and design adaptability make them suitable for widespread use in industries ranging from oil and gas to chemical processing. Typically crafted from materials such as stainless steel, carbon steel, or alloys, these flanges withstand high pressures and temperatures, ensuring long-lasting stability and safety.
Delving into the specifics, the standard 4-inch flange typically adheres to industry specifications such as ASME B16.5. Its dimensions are fundamental to its function; with a nominal 4-inch pipe size, these flanges have an outer diameter of around 9 inches, and the bolt circle diameter measures approximately 7.
5 inches. These precise measurements are designed to align perfectly with corresponding pipes and fixtures, ensuring seamless integration and minimal leakage risk.
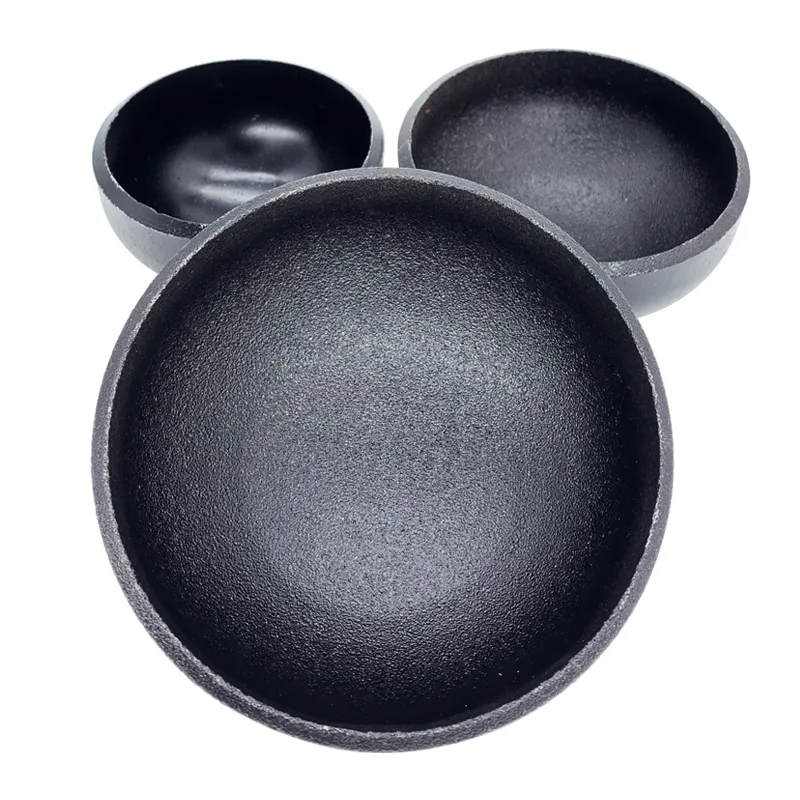
From a technical prowess standpoint, the manufacture of 4-inch flanges involves rigorous quality control and precision engineering. Using advanced forging and machining processes, manufacturers ensure that each flange is free from defects, capable of resisting the rigors of industrial conditions. Their robustness is further enhanced by heat treatments that provide added strength and resist corrosion, a critical factor when exposed to harsh environments.
Furthermore, the versatility of 4-inch flanges is amplified by the variety of types available to suit diverse applications. Common types include welding neck, slip-on, blind, socket weld, and threaded flanges. Each type offers unique advantages, with welding neck flanges providing excellent stress distribution, while blind flanges effectively terminate pipeline operations. The correct selection depends on factors such as pressure requirements, fluid type, and overall system design.
4 inch flange
Beyond their technical attributes, the successful deployment of 4-inch flanges depends significantly on installation accuracy and ongoing maintenance. Experience shows that improper installation can lead to misalignment, resulting in leaks and system inefficiencies. Ensuring that all bolting is correctly torqued and employing high-quality gaskets enhances the integrity of flange connections. Regular inspection and maintenance checks also play a crucial role in prolonging service life and identifying wear signs before they evolve into more significant issues.
In terms of authoritativeness and trustworthiness, selecting a reputable supplier is paramount. Trustworthy manufacturers and suppliers adhere to stringent quality standards and offer certifications that verify the materials and manufacturing processes. These certifications provide reassurance and establish a benchmark for quality and reliability. By partnering with such trusted entities, businesses can mitigate risks and ensure their operations remain efficient and safe.
For professionals seeking to optimize their systems with 4-inch flanges, it is recommended to engage with expert engineers who can provide insights specific to your industry. Tailored advice can be instrumental in navigating complexities such as pressure ratings, temperature limits, and chemical compatibility. Leveraging this expertise not only enhances system performance but also contributes to wider operational efficiencies.
To encapsulate, the 4-inch flange is more than a mere component; it is a vital element that underpins industrial piping systems. Its significant role is marked by its robust design, adaptability across various applications, and the intricate manufacturing processes involved. By prioritizing quality and expertise in selection and installation, businesses can elevate their operations, maintain safety standards, and achieve long-term success. In the ever-demanding realm of industrial processes, the 4-inch flange remains a powerhouse of performance and reliability, reflective of the deep engineering and technical intelligence that goes into its creation.