Understanding the ins and outs of a 4-inch pipe flange can be a game-changer for industries reliant on robust piping systems. With extensive experience in the field of industrial equipment, the pivotal role of pipe flanges becomes increasingly apparent in maintaining the integrity and efficiency of pipelines.
The 4-inch pipe flange, in particular, stands out for its versatility and essential applicability across various sectors.
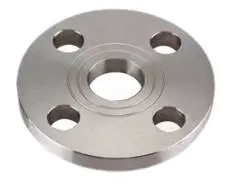
Manufactured with precision, the standard 4-inch pipe flange is designed to align with the specifications of virtually any piping system that requires a seamless connection. Expertise in material science and engineering ensures these flanges meet rigorous industry standards. Typically constructed from stainless steel, carbon steel, or alloys like nickel and copper, their durability in corrosive environments is unmatched, making them invaluable to the petrochemical, waterworks, and power generation industries.
When discussing the expertise required for selecting the appropriate flange, it is important to consider the operational conditions which include temperature, pressure, and fluid type. The size and pressure rating of a 4-inch flange are vital; they are specified under standards such as ANSI/ASME B16.5 for pipelines ranging from ½ inch to 24 inches. This ensures compatibility across various systems and adherence to international safety protocols.
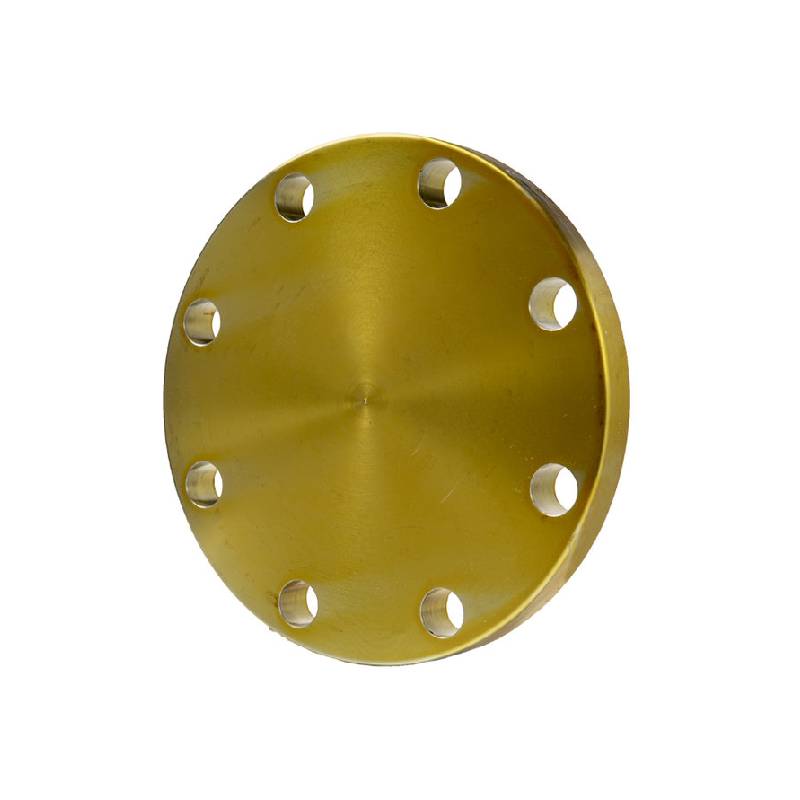
The installation of a 4-inch pipe flange demands a clear understanding of its components—typically including the flange ring, gasket, bolts, and nuts. An authoritative figure in the industry would stress the importance of using high-quality gaskets made from materials such as PTFE, rubber, or graphite, as they form the critical seal between flanges. Moreover, correctly sized bolts and nuts, usually matching the material of the flange, are crucial for maintaining joint integrity, especially under high-pressure conditions.
4 inch pipe flange
Trustworthiness in the industry is often built on the proven performance of materials and products. Quality assurance comes from rigorous testing, including hydrostatic pressure testing and ultra-sonic flaw detection. Companies with certifications like ISO 90012015 assure clients of flanges that perform exceptionally well in high-stakes environments.
For practical application, a power plant might use a 4-inch flange within their high-temperature steam systems. The flange ensures no leakage occurs as the superheated steam travels along the network of pipes, preserving system efficiency and safety. In the oil and gas sector, pipe flanges are vital for constructing pipelines that span vast distances, where reliability and leak prevention are non-negotiable.
Moreover, ongoing research and development within this field have pushed the boundaries, leading to innovations such as flanges with improved resistance to cracking and fatigue, enhanced sealing efficiency, and the capability to withstand extreme oscillating pressures. Companies investing in this level of expertise often collaborate directly with clients to tailor flange solutions that meet specific operational demands.
In conclusion, the 4-inch pipe flange may seem like a small component in the grand scheme of industrial systems, yet it plays a crucial role in functionality, safety, and efficiency. Those in the industrial field recognize that the success of a piping system is built on the quality, design, and installation precision of components like the 4-inch flange. For engineers and industrial procurement professionals, these flanges are indispensable tools in their arsenal, backed by the depth of expertise and trust built through years of reliable service.