Navigating the complexities of selecting the perfect 8-inch flange for industrial applications is crucial for operational efficiency and safety. An 8-inch flange serves as a vital component in piping systems, facilitating the seamless joining of pipes, valves, and other equipment. Whether you're working in oil and gas, chemical processing, or any other heavy-duty industry, understanding the intricacies of these mechanical connectors can significantly impact your project's success.
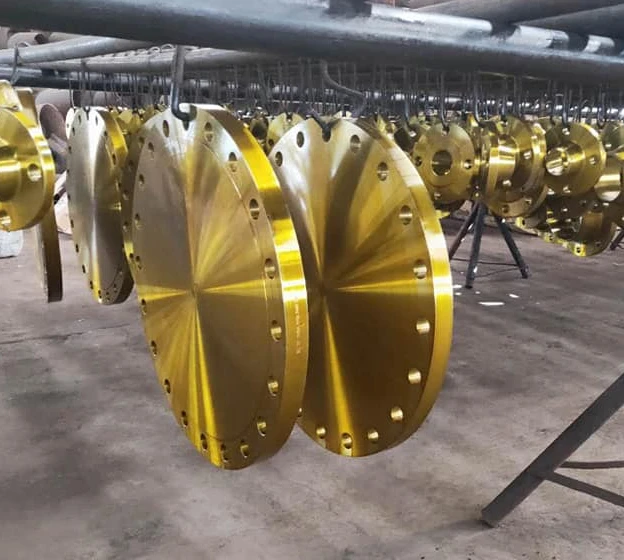
The primary consideration when choosing an 8-inch flange is material selection. Depending on the specific application, flanges are made from various materials, including stainless steel, carbon steel, and exotic alloys such as Inconel or Hastelloy. Stainless steel flanges are popular for their corrosion resistance and versatility. In environments where extreme temperatures and corrosive elements are present, opt for materials like Inconel, known for superior high-temperature resistance and robust chemical compatibility.
Equally critical is the flange's pressure rating, often specified by referring to standards such as ANSI, ASME, or API. These standards ensure that the flanges can withstand the pressure and temperature of the system they are integrated into. For high-pressure applications, a Class 1500 or 2500 flange may be appropriate, whereas lower pressure systems might only require a Class 150 or 300.
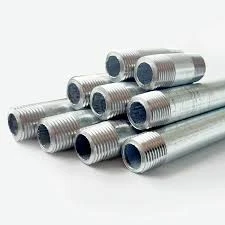
The facing type of an 8-inch flange also demands close attention. The most common facing types include raised face (RF), flat face (FF), and ring-type joint (RTJ). Raised face flanges are prevalent due to their flexibility and ability to enhance gasket compression, leading to improved sealing. For applications needing superior sealing under high pressure, RTJ flanges are preferred due to their metal-to-metal seal that accommodates minimal leakage.
An often-overlooked parameter is the bolt pattern and size. It's essential to ensure compatibility with existing systems, as mismatched bolt patterns can compromise the structural integrity and lead to catastrophic failures. Double-checking the bolt diameter, number of bolt holes, and the pitch circle diameter against your system specifications is a critical step.
8 inch flange
Furthermore, the surface finish of a flange can't be ignored, especially when dealing with sealing surfaces. The smoother the finish, the better the gasket will seal. Ideal surface finishes are specified by RMS (Root Mean Square) values, with a typical range for standard flanges being between 125-250 RMS. Cleaner and smoother finishes are crucial for systems requiring higher safety and seal integrity.
The lifecycle cost of an 8-inch flange encompasses both the purchase price and the maintenance expenses over time. Investing in high-quality flanges can reduce maintenance costs and extend the lifespan of your piping system—this is particularly true in aggressive environments where frequent replacements can incur significant labor and downtime costs.
Ensuring installation by skilled professionals further enhances the trustworthiness of your flanged system. Proper torque application when bolting the flanges can prevent leaks and guarantee system integrity. Misalignment or improper torque can lead to flange failures, hence the need for precision during installation cannot be overstated.
Expertise in selecting the right 8-inch flange involves understanding these multifaceted aspects to ensure the system's longevity and reliability. These connectors are not just mechanical necessities but are fundamental elements that can affect the overall efficiency and safety of an industrial operation. By integrating authoritative knowledge and rigorous standards, professionals can trust that their choice of flange will serve its purpose effectively, ensuring continuity and safety in their operations.