DIN EN 1092-1 Type 01/A flanges, commonly known as plate flanges, represent a critical component in various industrial applications due to their simplicity and versatility. These components, tailored to meet stringent manufacturing standards, play an indispensable role in facilitating secure connections within piping systems. Understanding the nuances of these flanges involves delving into their design, application, and material selection, underlining their importance in maintaining system integrity.
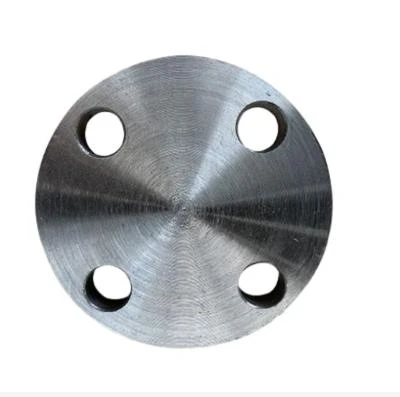
Our journey begins by exploring the engineering principles that underscore the use of EN 1092-1 Type 01/A flanges. Specifically crafted for industries demanding high precision, these flanges exhibit a flat, circular disk shape with a central hole for attachment to a pipeline or equipment. Unlike their raised face counterparts, their flat interface presents an economical solution for various projects, delivering a cost-effective approach without compromising on performance.
Material choice in the production of Type 01/A flanges helps to enhance their robustness. Often, carbon steel is employed due to its excellent mechanical properties and cost efficiency. However, applications exposed to aggressive mediums or demanding climates often necessitate the use of stainless steel or other alloys, which provide superior resistance to corrosion and thermal conditions. The material's resilience ensures that the flange not only sustains system reliability but also extends operational lifespan, thus promoting industrial safety and efficiency.
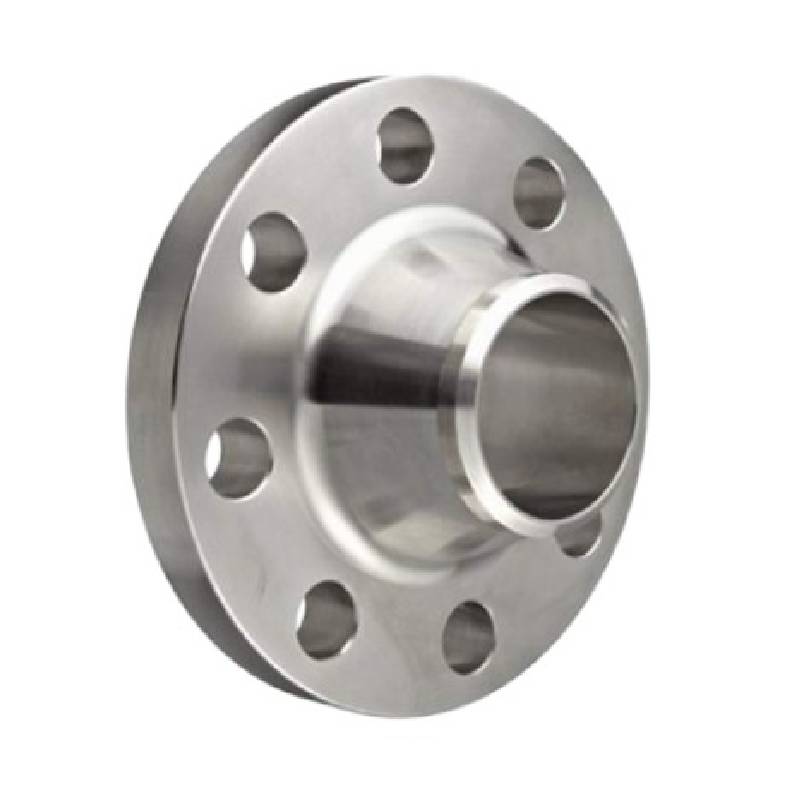
In terms of application,
the scope of EN 1092-1 Type 01/A flanges is broad and multifaceted. These flanges find placement in sectors ranging from water systems to pharmaceutical operations, highlighting their adaptability. Their design accommodates various piping systems, facilitating smooth fluid transportation and secure connectivity. This adaptability is particularly advantageous in setups requiring frequent assembly and disassembly, where flange efficiency and robustness are paramount.
en1092 1 01a
Industry-specific standards mandate rigorous testing and certification to authenticate the performance of these flanges. By adhering to EN 1092-1 specifications, manufacturers ensure each flange’s capability to withstand diverse pressures and temperatures. This emphasis on quality and adherence to international standards instills confidence among engineers and designers, who rely on these components to uphold system reliability.
A crucial aspect often overlooked is the installation technique and maintenance regime associated with these flanges. Proper alignment during installation guarantees the optimal function of the flange, minimizing the risk of leaks or misalignment-induced mechanical strains. Subsequently, regular maintenance checks, coupled with a proactive replacement strategy for worn or damaged flanges, contribute significantly to mitigating system failures.
From an environmental perspective, flanges crafted and maintained under EN 1092-1 standards offer sustainability benefits. By ensuring leak-proof connections, they aid in the prevention of harmful emissions and wastage that could negatively impact ecosystems. This environmental stewardship reflects a broader industrial commitment toward sustainable practices, seeking to balance operational excellence with ecological responsibility.
In conclusion, the EN 1092-1 Type 01/A flanges stand as a testament to engineering precision, offering valuable insights into their applicability and performance across industry verticals. Whether viewed from the lens of cost efficiency, material diversity, or environmental sustainability, the strategic implementation of these flanges within piping systems underscores their indispensable role in modern engineering. By prioritizing informed material selection, adherence to standards, and meticulous maintenance practices, industries can harness the full potential of these components, ensuring operational success for years to come.