For industries that demand high quality and standardized components, EN 1092-1 Type B1 flange is a term that frequently appears in technical discussions. Its reputation stems not only from its compliance with European standards but also from its robustness in application across various industries. Understanding the nuances of this flange type is critical for professionals seeking to optimize their systems and ensure longevity and reliability.
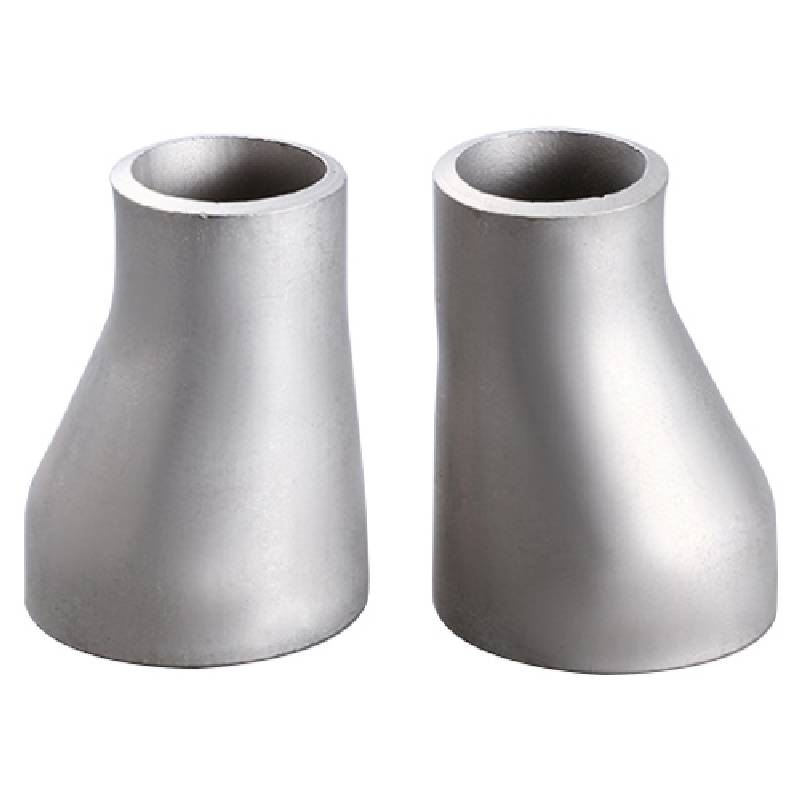
The EN 1092-1 Type B1 flange, primarily used in piping systems, is a product of rigorous engineering. This flange is characterized by its use in conjunction with welded neck flanges or blind flanges. It is often favored for its butt welding configuration, which is integral in achieving a high-integrity and leak-proof joint. This configuration is particularly advantageous in high-pressure systems where leaks could lead to significant operational risks.
One of the standout features of the Type B1 flange is its versatility in accommodating different pressure ratings. Depending on the manufacturing specifications, these flanges can operate optimally across various pressure classes, making them suitable for both low and high-pressure systems. This adaptability ensures that industries ranging from petrochemical to water treatment can benefit from the reliable performance of these components.
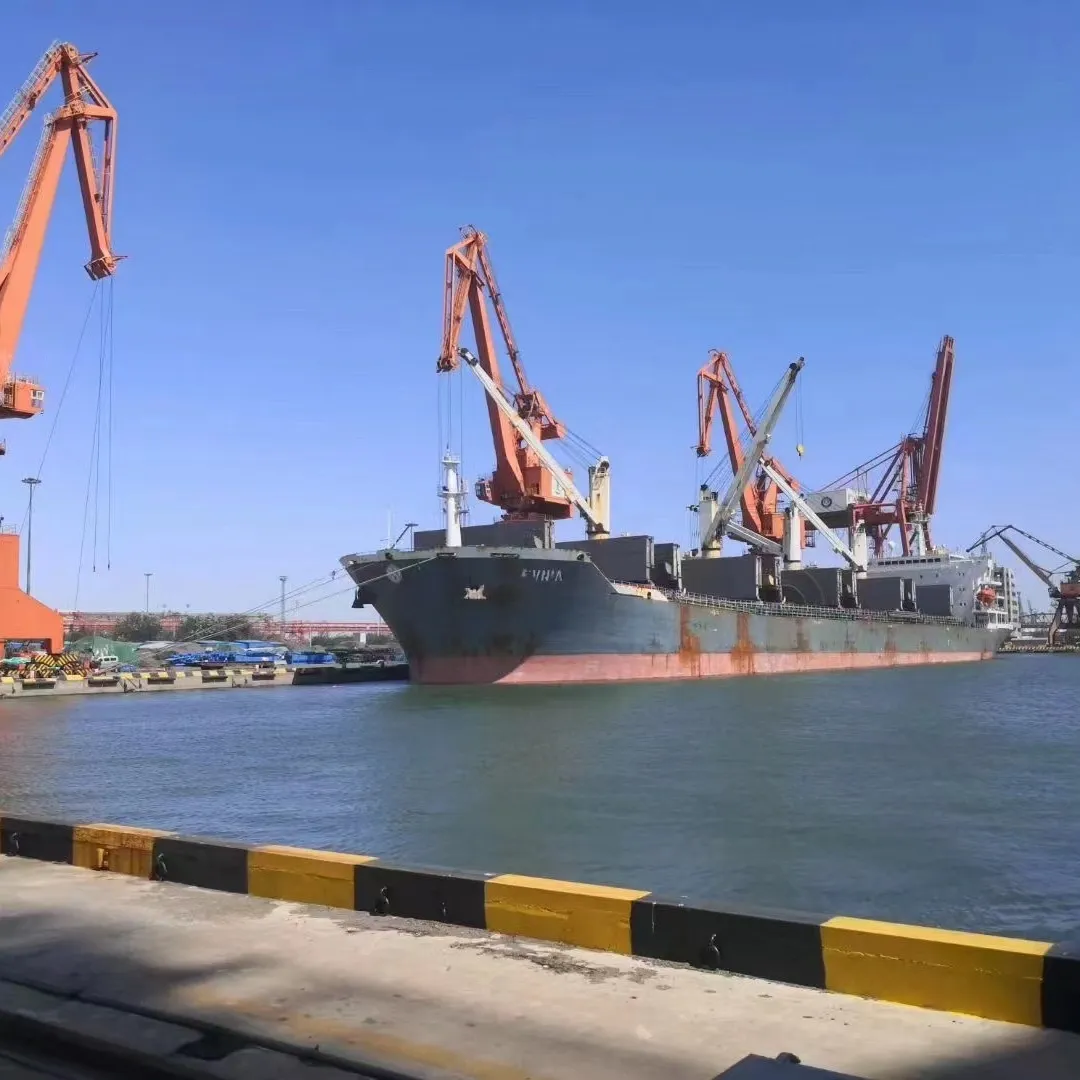
In terms of materials, the EN 1092-1 Type B1 flanges are fabricated using an array of metals to suit specific industrial applications. Stainless steel is a popular choice due to its excellent corrosion resistance, which is essential for environments exposed to harsh chemicals or extreme temperatures. Carbon steel options are also prevalent, often preferred for their strength and cost-effectiveness in standard applications. Some manufacturers may offer these flanges in other alloys depending on the required mechanical properties or environmental considerations.
The expertise behind the production of these flanges lies in meticulous design and precise engineering standards. Manufacturers must adhere to detailed specifications regarding dimensions, tolerances, and surface finishes. This precision ensures that, once installed, the flanges will perform predictably without requiring frequent maintenance. Engineering teams often utilize finite element analysis (FEA) to simulate stress distribution and identify potential points of failure before finalizing the design.
Such rigorous testing underscores the reliability and durability that EN 1092-1 Type B1 flanges are known for.
en 1092 1 type b1
A key aspect often discussed by industry experts is the installation process of these flanges. Ensuring proper alignment and following the correct welding procedures is paramount to maximizing the flange's performance and lifespan. Poor installation can not only lead to leaks but also compromise the structural integrity of the piping system. Therefore, experienced personnel should oversee the fitting and welding to ensure adherence to best practices and standards.
From a practical perspective, procurement of EN 1092-1 Type B1 flanges should be approached with attention to both certification and supplier reputation. Certifications such as PED (Pressure Equipment Directive) can be indicators of quality, ensuring that the product meets stringent safety and performance standards required by the European Union. Additionally, engaging with suppliers known for their consistency and quality control can mitigate risks associated with subpar manufacturing practices.
Trust is paramount in industries where safety and reliability are non-negotiable. Consequently, the decision to integrate EN 1092-1 Type B1 flanges into a system should be informed by a thorough evaluation of the supplier's adherence to industry standards, their track record, and third-party reviews. When these flanges perform as expected, they can contribute significantly to the efficiency and safety of operations, instilling confidence in stakeholders and regulatory bodies alike.
In conclusion, the EN 1092-1 Type B1 flange represents a blend of precision engineering and industry expertise. Its adaptability across different pressures and environments, combined with its robust design, makes it a cornerstone component for many industrial applications. Understanding its specifications, materials, and installation nuances is essential for any professional seeking to enhance system integrity and performance. As industries continue to evolve, these flanges will undoubtedly remain vital, showcasing the importance of quality and expertise in industrial components.