Flange pricing is a crucial consideration for industries ranging from oil and gas to manufacturing and automotive. Understanding the dynamics affecting flange costs, the factors contributing to fluctuations, and identifying strategies for cost-efficiency are vital for any business that relies on these essential components.
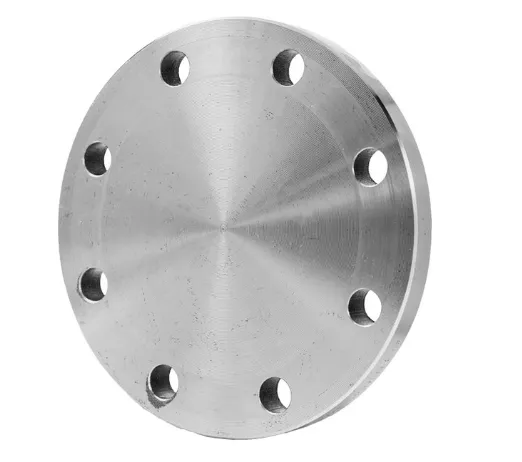
Flanges are primarily used to connect pipes, valves, pumps, and other equipment to form a piping system. They are typically welded or screwed, and are available in various materials including stainless steel, carbon steel, and alloy steel, each affecting the price significantly. The choice between slip-on, weld neck, socket weld, lap joint, and blind flanges can also impact the total cost involved in a project.
The price of flanges is influenced by multiple factors.
First and foremost is the material choice. Stainless steel flanges, known for their corrosion resistance and durability, typically carry higher prices than those made from carbon steel. Alloy steel flanges, offering specific properties depending on the alloying elements, might cost more or less depending on the market demand for those materials and their availability.
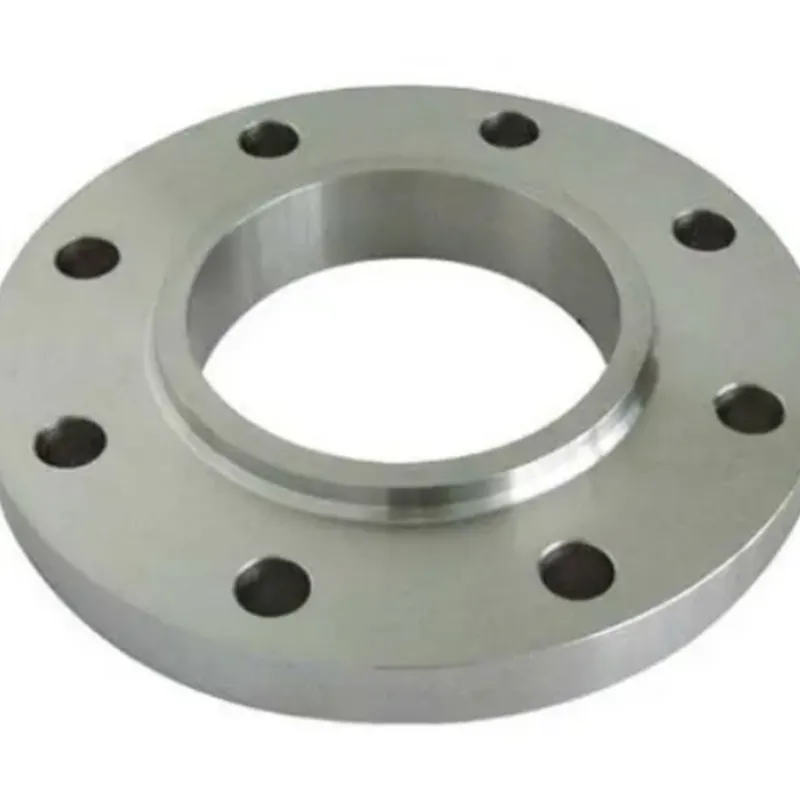
Another significant factor is the manufacturing process. Custom flanges, tailored to specific requirements in terms of size, pressure, or unique industrial applications, usually incur additional costs. The complexity and precision of these processes reflect directly in the pricing structure. Furthermore, the geographical location can alter pricing due to transportation costs and supply chain logistics.
Industry standards and certifications also play a crucial role in flange pricing. Compliance with international standards such as ANSI, ASME, DIN, or JIS can add to costs but ensure that the flanges meet stringent performance and safety requirements. Such compliance is often non-negotiable in sectors where reliability and safety are paramount.
The market dynamics, including the influence of global supply and demand, impact flange prices as well. Events such as geopolitical tensions, changes in regulatory environments, or shifts in the global economic landscape can lead to fluctuations in raw material costs or manufacturing dynamics, eventually affecting flange pricing.
flange price
To navigate these pricing challenges, businesses can implement several strategies. Developing long-term partnerships with reliable suppliers can help stabilize costs through negotiated pricing, future contracts, or bulk purchasing agreements. Engaging in ongoing supplier assessments ensures that companies are consistently receiving quality products without unexpected price surges.
Adopting a Total Cost of Ownership (TCO) approach also allows companies to evaluate the true cost of flanges over their lifecycle, rather than simply up-front purchase costs. This includes considerations of maintenance, durability, efficiency, and eventual disposal or recycling.
The trend towards digitization and smart technologies can further provide cost efficiencies. Advanced monitoring systems can extend the life of flanges by predicting wear and tear, thus reducing the need for frequent replacements.
Moreover, leveraging data analytics can help companies forecast demand more accurately and optimize inventory levels, thus reducing overstocking costs or shortages that could increase expenses during high-demand phases.
As sustainability becomes a key factor in procurement decisions, companies are increasingly focusing on environmentally friendly materials and technologies. Investing in green technology not only potentially reduces costs in the long term but also aligns with global sustainability initiatives and regulatory requirements.
In conclusion, understanding the comprehensive factors affecting flange prices enables companies to make informed decisions that balance cost with quality and compliance. With strategic planning and adoption of innovative solutions, businesses can effectively manage their flange procurement processes, ensuring reliability and cost-efficiency in their operations.