Flanges and fittings are paramount components in the pipeline industry, serving as the backbone for expansive network systems. Their significance lies not only in their mechanical utility but also in ensuring synergies that enhance the fluid flow and structural integrity. Understanding these components requires a blend of experience, expertise, authoritativeness, and trustworthiness—elements essential for crafting solutions in diverse applications.
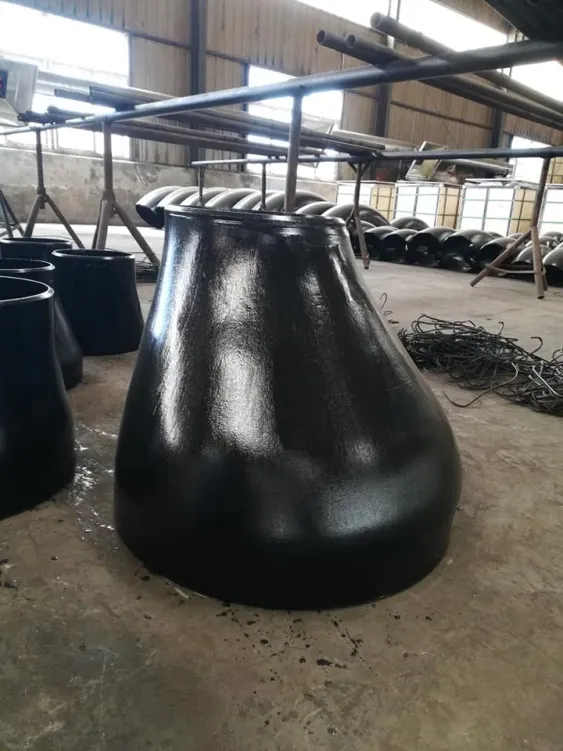
Flanges are primarily used to connect pipes, valves, pumps, and other equipment to form a piping system. They provide easy access for cleaning, inspection, or modification of the system. The intricate design of flanges, which includes bolt holes, gaskets, and alignment mechanisms, plays a crucial role in delivering stable connections that withstand high pressure and temperature conditions.
Fittings serve as the connectors, regulators, and terminators of pipe systems, dictating the functionality and flexibility of these networks. From elbows and tees to reducers and caps, each fitting addresses specific needs within an application, ensuring fluid dynamics are maintained according to the system's requirements. These components, often underestimated, play critical roles in directing flow, reducing strain, and compensating for expansion and contraction brought about by thermal variations.
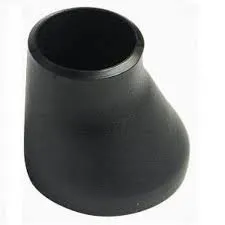
Experience in this domain underscores the importance of material selection. Material compatibility is pivotal for reliability and lifespan. Metals like stainless steel, carbon steel, and alloys are chosen based on their resilience to oxidation, corrosion, and wear. Engineers with years of field experience recognize that selecting the right material is akin to choosing the right foundation for a structure—it defines the durability and safety of the system.
flanges and fittings
Expertise in design and manufacturing transforms raw blueprints into functional excellence. Advances in CNC machining and 3D modeling have revolutionized the production of flanges and fittings, allowing for precise tolerances that enhance the overall functionality of piping systems. Further, non-destructive testing and quality assurance protocols ensure each component meets rigorous industry standards before deployment. Expertise also extends to using advanced software for simulation and stress analysis, predicting the behavior of these components under various operational scenarios.
Authoritativeness emerges from adherence to international standards such as ANSI, ASME, and DIN, which guide the specifications, testing, and certification processes. These standards are non-negotiable benchmarks that have been formulated through decades of research and collaboration among global industry leaders. Compliance ensures that products are not only safe but also versatile for global trade and interoperability. Professionals in this field often engage with standard-setting bodies to remain at the forefront of innovations and regulations.
Trustworthiness is perhaps the most intangible yet critical aspect. It is built over time through consistent performance and reliability. Suppliers and manufacturers who invest in quality control, after-sales service, and continuous improvement cultivate a reputation that transcends transactional relationships. Customers, ranging from small enterprises to large industries, rely on this trust to sustain their operations without interruptions. User testimonials, case studies, and industry awards serve as testament to a company's commitment to excellence.
In conclusion, flanges and fittings may appear as simple components within a complex system, yet their role is profoundly significant. Their design, material, manufacturing process, and compliance with standards are scrutinized by experts aiming to optimize pipeline systems. The industry's commitment to innovation and quality assurance not only enhances performance but also builds a framework of trust. As technology evolves, so too will the capabilities of these products, ultimately enhancing the efficiency and sustainability of industrial operations while maintaining unwavering standards of safety and reliability.