Hydraulic flange fittings serve as a vital component in many industrial systems, offering unparalleled reliability and efficiency in managing high-pressure fluid flow. Through firsthand experience and deep industry knowledge, we unpack the nuances that make hydraulic flange fittings indispensable in modern mechanical applications.
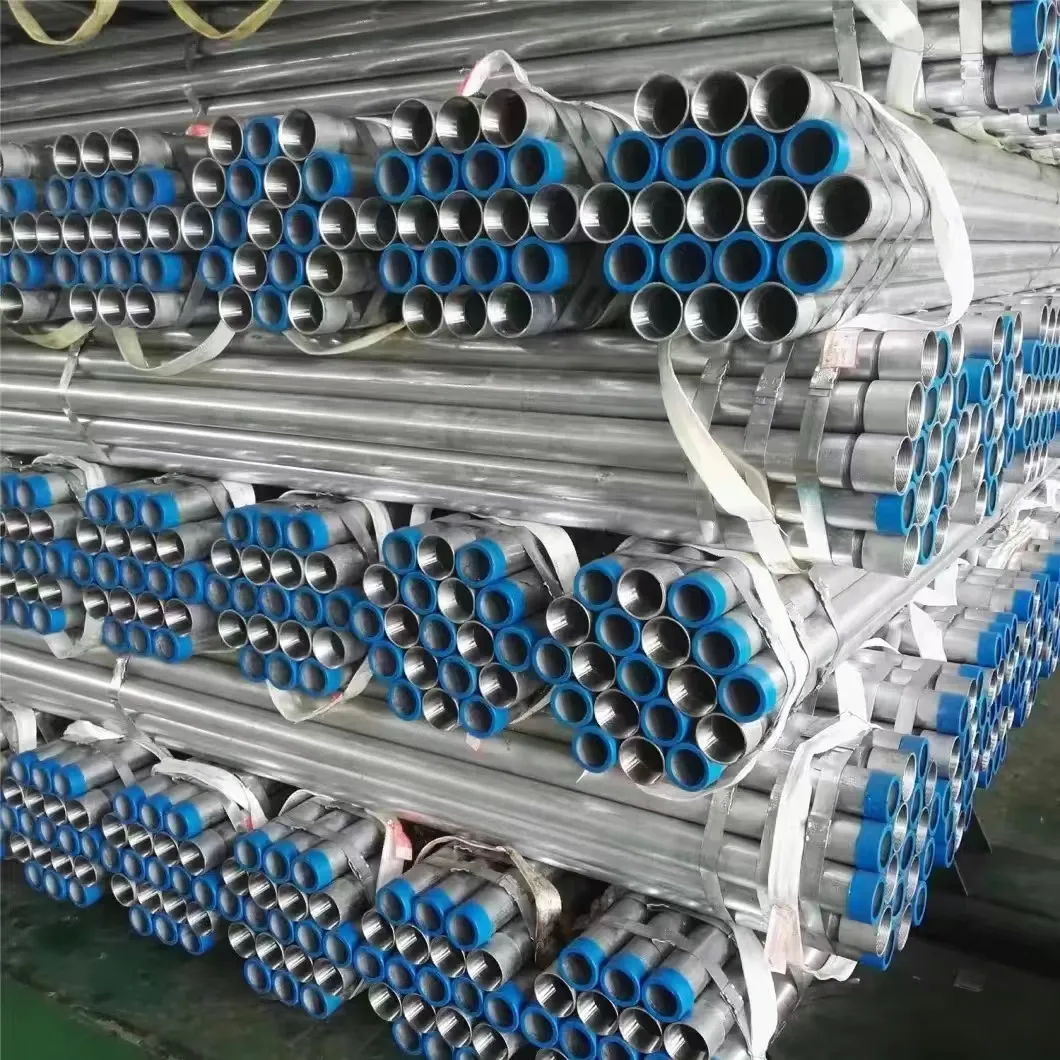
One of the most striking features of hydraulic flange fittings is their design capability to withstand extreme pressure and temperature variations. This is not merely a manufacturing feat but a testament to the engineering precision that goes into developing these components. Flange fittings are meticulously designed to prevent leaks, thereby ensuring seamless operation in hydraulic systems. The high-quality materials used—often steel or stainless steel—are chosen for their endurance and strength, reducing the risk of unexpected equipment failures.
Expertise in selecting the right hydraulic flange fitting can transform the efficiency of an industrial setup. A nuanced understanding of the pressure ratings, dimensional standards, and installation requirements is essential. For instance, choosing between Code 61 and Code 62 flanges can make a substantial difference in performance; Code 61 is suitable for medium-pressure applications, while Code 62 is designed for higher pressures. Such specific knowledge aids in making informed decisions that impact operational efficiency and safety.
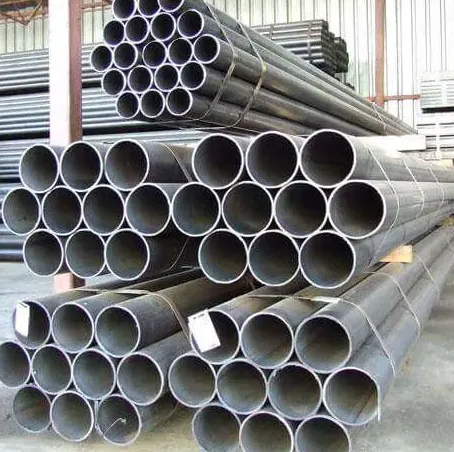
Authoritativeness in the field of hydraulic systems is established through consistent delivery of exceptional performance. Leading manufacturers of hydraulic flange fittings often adhere to rigorous industry standards such as ISO 6162, which ensures uniformity in dimensions and compatibility across various hydraulic applications. This standardization is crucial for global operations, as it guarantees that components can be replaced or upgraded without compatibility concerns. Companies that prioritize these standards are viewed with higher regard, both for their products' reliability and their contribution to advancing industry best practices.
hydraulic flange fittings
Trustworthiness in hydraulic flange fittings is built over time through demonstrated reliability in demanding conditions. Customers and engineers often rely on field test data and real-world application results to evaluate the dependability of these components. Trust is further reinforced by warranties and certifications offered by reputable manufacturers, which provide a safety net against potential defects and assure quality. The relationship between manufacturer and client strengthens as a result, fostering long-term partnerships built on the mutual goal of achieving optimal system performance.
Evaluating the lifecycle and maintenance needs of hydraulic flange fittings is crucial for minimizing operational downtime. Regular inspections and maintenance schedules are recommended to extend the life of these components. Any signs of wear, such as corrosion or fatigue, should be addressed immediately to prevent further damage. Deploying advanced monitoring systems, such as sensors that detect changes in pressure or flow irregularities, can serve as an early warning system, helping prevent costly breakdowns.
Investing in high-quality hydraulic flange fittings is not merely an expenditure but a commitment to enhancing overall system efficiency. As industries continue to push the boundaries of what is possible with hydraulic systems, flange fittings will play a pivotal role in shaping the future of fluid dynamics.