Blind flanges, often integral components in industries reliant on the safe handling of pressurized fluids, perform a critical function by securely sealing pipe ends and openings. Effective strategies for reducing blind flanges are continuously evolving, drawing from industry expertise, technological advancements, and authoritative standards. This discussion delves into practical methods and insights that enhance the efficiency, safety, and cost-effectiveness of blind flange utilization.
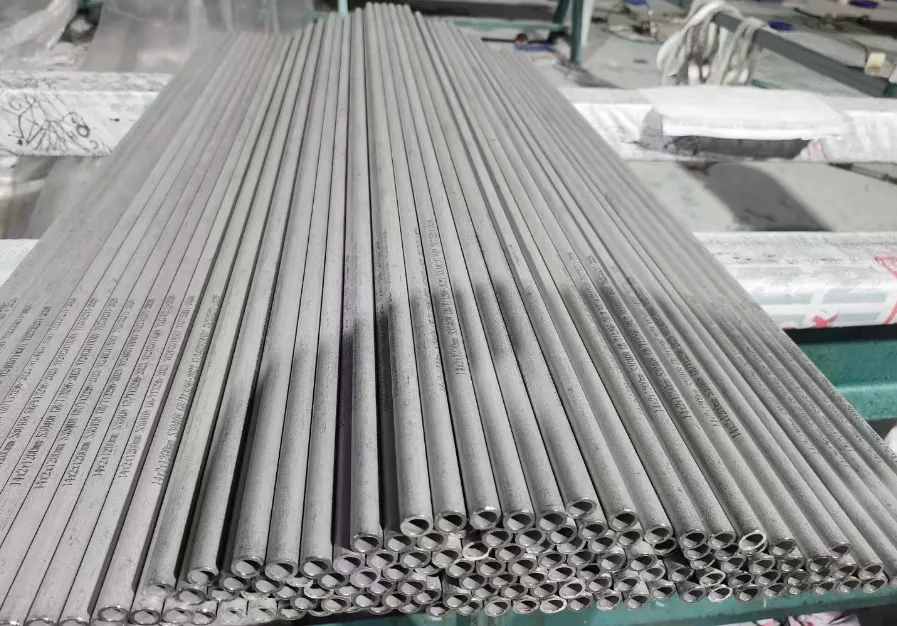
When managing the deployment of blind flanges, experience underscores the importance of understanding the specific requirements of each application. Experienced engineers recognize that not all blind flanges are created equal; selecting the appropriate material, size, and pressure rating is crucial. High-quality blind flanges made from corrosion-resistant materials such as stainless steel or alloy variants ensure durability and longevity, particularly in industries exposed to harsh environmental conditions. This expertise not only extends the life of the components but also reduces the frequency of replacements, leading to decreased operational costs.
Innovation in blind flange design has introduced a spectrum of nuanced features aimed at improving overall performance and reliability. Advanced manufacturing techniques allow for precision-engineered products that meet stringent industry standards. A prominent example is the integration of enhanced gasket sealing technologies, which significantly minimize the potential for leaks. These developments draw from authoritative research and rigorous testing procedures, ensuring compliance with global safety and performance standards.
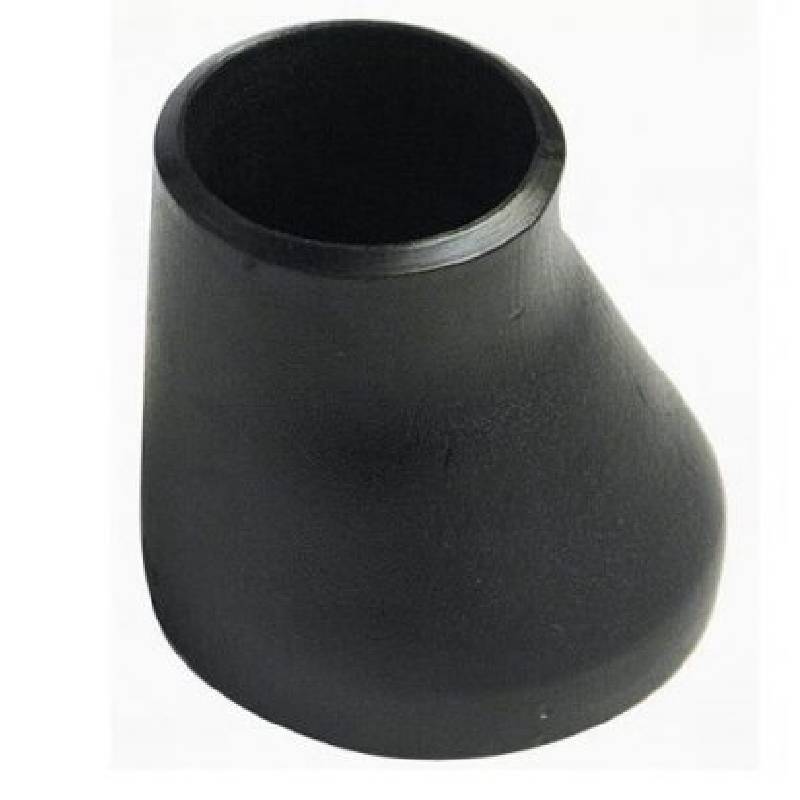
Moreover, a thorough understanding of the operational environment and its challenges is essential for optimizing the use of blind flanges. Expertise in environmental analysis allows for the selection of components that best resist degradation due to temperature fluctuations, chemical exposure, and mechanical stress. By aligning the characteristics of the blind flange with the specific conditions of the application, industries can reduce maintenance needs and enhance the overall efficiency of their piping systems.
reducing blind flange
Another critical aspect of reducing blind flange usage without compromising safety and effectiveness is the implementation of proper installation techniques. Industry regulations and authoritative guidelines emphasize the importance of correct torque application and alignment during the installation process. Proper training and certification programs ensure that personnel are equipped with the necessary skills and knowledge to perform installations that comply with industrial standards. This trustworthiness in procedural execution is vital for maintaining system integrity and preventing costly operational disruptions.
Additionally, adopting digital monitoring solutions represents a transformative step in optimizing blind flange management. Real-time data collection on parameters such as pressure and temperature enables proactive maintenance and timely interventions, thereby reducing the need for unnecessary replacements. The integration of Internet of Things (IoT) technologies has further facilitated the capability to monitor and analyze performance data remotely, empowering decision-makers with valuable insights to enhance operational efficiencies.
The strategic reduction of blind flanges is also intertwined with a broader sustainability agenda. As industries strive towards minimizing their environmental impact, the role of blind flange management in reducing material waste and energy consumption becomes increasingly significant. By prioritizing long-lasting, efficient materials and minimizing the frequency of replacements, businesses align operational excellence with ecological stewardship.
In conclusion, effective strategies for reducing blind flange usage hinge on a comprehensive understanding of the interplay between material selection, manufacturing advancements, installation processes, and digital technology integration. Drawing from a wealth of experience and authoritative knowledge, industries can enhance the safety, efficiency, and sustainability of their operations. The commitment to innovative practices and adherence to established standards solidifies a foundation of trustworthiness, ensuring that blind flange management not only meets but exceeds the dynamic demands of contemporary industrial applications.