When it comes to selecting the right materials for construction or plumbing projects, the 10 inch metal pipe stands out for its unmatched durability, reliability, and versatility. Drawing from extensive industry experience and thorough market analysis, this article delves into the technical specifics and practical applications of the 10 inch metal pipe, aiming to provide valuable insights for industry professionals and decision-makers.
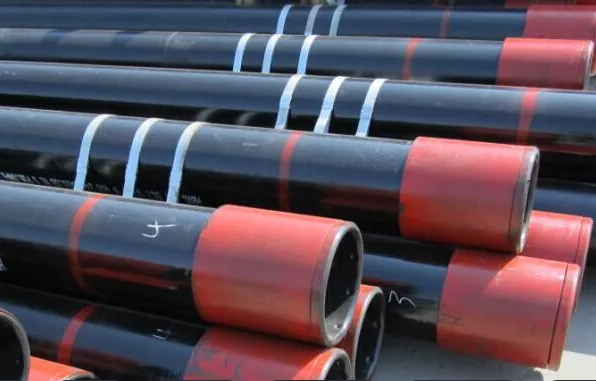
Fundamentally, the choice of metal in pipe construction is critical. Among available options, stainless steel, galvanized steel, and cast iron are common preferences due to their resistance to corrosion, tensile strength, and overall longevity. A 10 inch diameter offers substantial throughput, making it ideal for tasks requiring significant fluid or gas transfer without sacrificing structural integrity.
Real-world applications of the 10 inch metal pipe are as diverse as they are critical. In the oil and gas industry, these pipes form the backbone of infrastructure, enabling secure transportation of resources across challenging terrains. These pipelines are engineered to withstand high pressure and extreme environmental conditions, a testament to the engineering prowess behind their design and fabrication. Experts in the field emphasize regular inspections and maintenance as part of operational best practices to mitigate risks and prolong service life.
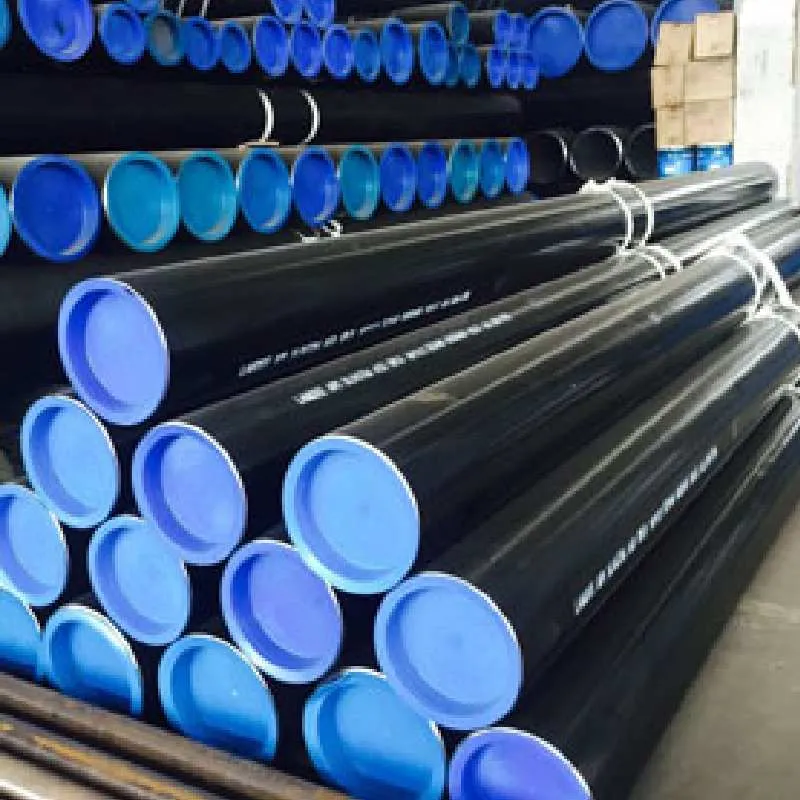
In civil engineering, 10 inch metal pipes are integral to municipal water systems and sewage networks where capacity and dependability are paramount. Installation of these systems demands meticulous planning, specialized knowledge, and adherence to industry standards. Professional consultation often involves mapping the layout to ensure optimized flow and minimal environmental impact. Engineers utilize computer-aided design (CAD) software for precision in planning and execution, ensuring compliance with regulatory frameworks.
Trust is built on transparency and verified performance. Many manufacturers provide detailed specifications and testing results, reflecting their commitment to quality assurance. These documents often include tensile strength tests, corrosion resistance metrics, and pressure tolerance data, all essential for stakeholders to make informed decisions. Those involved in procurement need an acute understanding of these parameters to match product features with project requirements.
10 inch metal pipe
Customization options further exemplify the versatility of 10 inch metal pipes. While standard dimensions and materials cover most needs, bespoke solutions cater to unique environmental or technical demands. Whether requiring specific coatings, joint types, or wall thicknesses, collaborating with manufacturers to tailor products offers bespoke solutions enhancing system performance.
Safety remains a cornerstone in the use of any metal piping system. Compliance with international safety standards such as ASTM (American Society for Testing and Materials) or the ISO (International Organization for Standardization) ensures that the products meet rigorous criteria. Industries increasingly rely on smart technology integration—sensors and IoT devices for monitoring structural health in real-time, enabling predictive maintenance and reducing downtime.
Despite the inherent strength of metal piping systems, they are not impervious to wear and tear. Ongoing research in material science is yielding innovations in alloy compositions that promise greater longevity and cost-efficiency. Emerging trends in fortifying metal pipes with composite materials could revolutionize performance metrics, presenting exciting future possibilities for industry advancement.
Ultimately, the utilization of a 10 inch metal pipe in any project should be justified by thorough needs assessment and commitment to quality. Engaging with experienced suppliers and maintaining an informed perspective on technology advancements can considerably enhance project outcomes.
In conclusion, the 10 inch metal pipe is more than just a conduit; it is a critical component in many of the infrastructures that support our daily lives. Its selection and application require a blend of expertise, rigorous material science, and an unwavering focus on standards compliance. As technology and industry demands evolve, those who harness the capabilities of this dependable component will find themselves at the forefront of efficiency and innovation.