Understanding the Significance of Alloy Die Casting in Modern Manufacturing
Alloy die casting is an essential process in modern manufacturing, particularly in industries where precision and durability are paramount. It involves the use of high-pressure to force molten metal into a die, a custom-made tool with intricate cavities that form the final shape of the part. The metal alloy, cooled and solidified within the die, then takes on the precise dimensions and features of the cavity, resulting in a strong and dimensionally stable component.
The choice of alloy in die casting plays a crucial role in determining the end product's properties. Common alloys used include aluminum, zinc, magnesium, and copper-based alloys, each with its unique characteristics. Aluminum alloys, for instance, are popular due to their excellent strength-to-weight ratio, corrosion resistance, and thermal conductivity. Zinc alloys, on the other hand, offer high production rates and are ideal for intricate parts with fine details. Magnesium alloys are the lightest of all, providing superior weight reduction without compromising strength, while copper-based alloys provide excellent thermal and electrical conductivity.
Die casting offers several advantages over other manufacturing methods. First, it allows for the creation of complex shapes with high accuracy and consistency, reducing the need for secondary machining. Second, it can produce parts with thin walls and tight tolerances, making it suitable for components requiring intricate designs Second, it can produce parts with thin walls and tight tolerances, making it suitable for components requiring intricate designs
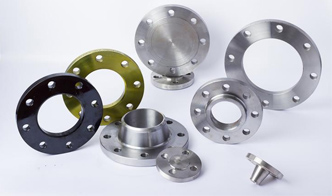
Second, it can produce parts with thin walls and tight tolerances, making it suitable for components requiring intricate designs Second, it can produce parts with thin walls and tight tolerances, making it suitable for components requiring intricate designs
alloy die casting. Third, die casting is highly efficient, capable of producing large quantities of parts quickly and economically.
Moreover, the process of alloy die casting has evolved with advancements in technology. Computer-aided design (CAD) and computer-aided manufacturing (CAM) have revolutionized the design and creation of dies, allowing for even more intricate and precise parts. Furthermore, the integration of robotics and automation has increased efficiency and reduced errors in the casting process.
However, challenges do exist. Die casting can be affected by factors like shrinkage, porosity, and internal stresses, which need to be carefully managed through proper design, material selection, and process control. Additionally, the high initial cost of creating dies can be a barrier, especially for low-volume productions.
In conclusion, alloy die casting is a cornerstone of modern manufacturing, enabling the production of high-quality, durable, and intricate components across various industries, from automotive to aerospace, electronics, and beyond. As technology continues to evolve, we can expect further improvements in efficiency, precision, and sustainability in this vital process.