When it comes to plumbing and construction, connecting galvanized pipes is crucial for ensuring a robust and durable system. Galvanized pipes, coated in a protective layer of zinc, offer excellent resistance to corrosion and rusting, making them a popular choice for both residential and commercial applications. However, connecting these pipes requires a certain level of expertise to ensure longevity and functionality.
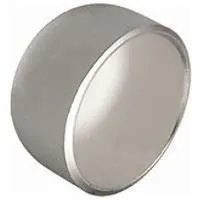
To begin with, selecting the right tools and materials is imperative. A pipe threader, pipe cutter, and the correct pipe wrenches are essential for making accurate cuts and connections. The initial step involves measuring the length of the pipe required and marking it accurately. Utilizing a pipe cutter, one can achieve a clean cut, which is integral for a tight and secure connection. A neat cut ensures there are no jagged edges that could compromise the threading process.
The threading process requires precision as it involves creating threads on the ends of the pipe to allow for a snug fit into connectors or other pipes.
A pipe threader is used to cut threads into the galvanized pipe’s end. It's crucial to ensure that the threads are cut cleanly and uniformly, as inconsistent threading can lead to leaks or connection failures. Applying some cutting oil during the threading process can reduce friction and improve the quality of the threads, thereby prolonging the pipe’s lifespan.
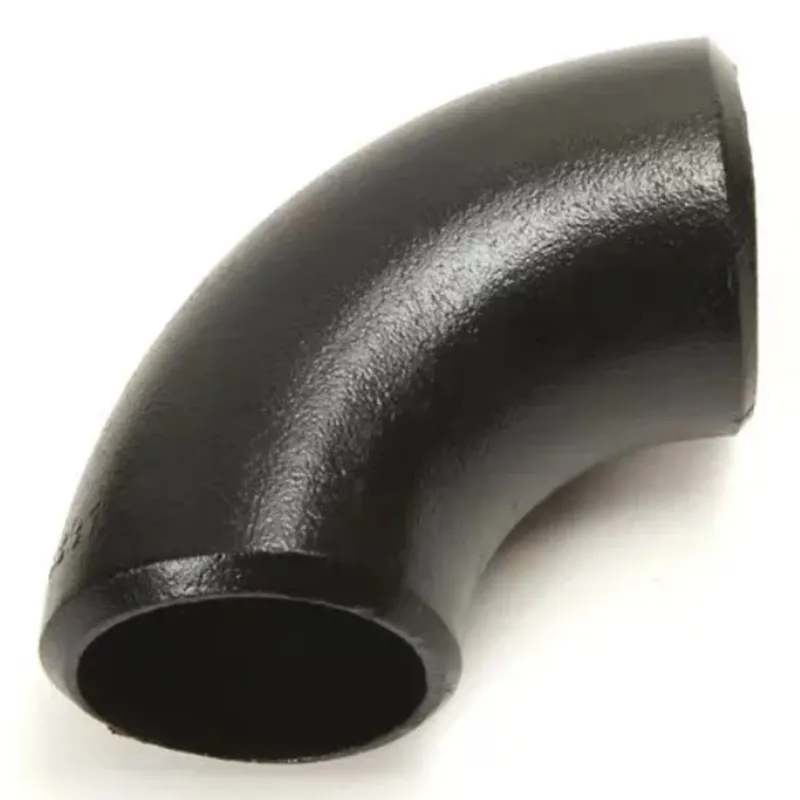
Once the threads are prepared, it’s essential to use a quality pipe joint compound or Teflon tape on the threads. These materials serve as a sealant, preventing potential water leakage and protecting against corrosion. When wrapping Teflon tape, it should be applied in a clockwise direction from the pipe end, covering the threads thoroughly to form an effective seal.
After preparing the threads, the next step is assembly. This involves joining the pipes by screwing them into connectors or fittings such as elbows, tees, or couplings. It’s crucial to avoid over-tightening, as excess force can damage the pipe or fittings. A secure connection is achieved by hand-tightening the joint initially, followed by using a wrench for a couple of additional turns. This method ensures that the connection is tight enough to prevent leaks but not too tight to cause damage.
connecting galvanized pipe
One common challenge in working with galvanized pipes is their propensity to rust over time, especially on the threaded areas where the protective zinc coating is compromised. To mitigate this, periodic inspections and maintenance are advised. During inspections, checking for any signs of rust or corrosion and addressing them promptly helps maintain the integrity of the pipeline. Applying anti-rust spray or paint specifically formulated for metallic surfaces can extend the pipe’s life exponentially by providing an added layer of protection.
In scenarios that require joining galvanized pipes with other materials such as copper or PVC, dielectric unions are recommended. These unions prevent metal-to-metal contact, thus avoiding galvanic corrosion—a common issue when dissimilar metals are connected. This ensures the efficacy and longevity of the plumbing system.
Lastly, adhering to building codes and industry standards is crucial for optimal results. Codes dictate the proper methods and materials for connecting galvanized pipes, and adhering to these not only ensures safety but also guarantees quality. Familiarizing oneself with local regulations and updates in the industry standards can provide the necessary knowledge to execute the task correctly.
For those not inclined to undertake this type of plumbing work, consulting with a professional plumber is advisable. Experienced professionals bring a wealth of knowledge and expertise, ensuring that the job is done correctly the first time. They are well-versed in diagnosing potential issues, choosing appropriate solutions, and executing tasks efficiently, thereby saving you time and mitigating costly future repairs.
Through careful planning, execution, and maintenance, connecting galvanized pipes effectively can sustain high-performance plumbing systems for decades. Whether for water transportation or as part of gas pipelines, the resilience and reliability of these connections offer long-term benefits when managed with expertise and precision.