Navigating the intricate realm of metal tubes unveils a world where precision, durability, and versatility converge to sculpt masterpieces in countless industries. Metal tubes, crafted meticulously from various alloys, serve as the backbone for both simple and complex applications, embodying a combination of design and functionality honed over years of expertise.
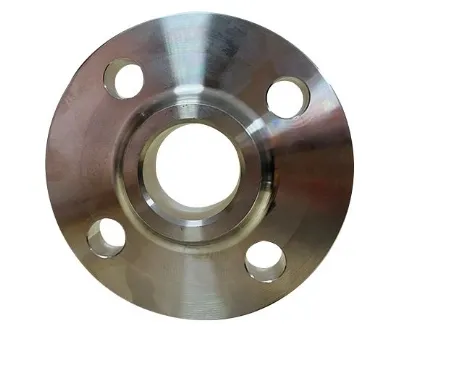
The journey begins with the material selection, often dictated by specific industry needs. The choice between stainless steel, aluminum, copper, and other specialized alloys hinges on factors such as strength, corrosion resistance, and thermal properties. For instance, stainless steel tubes are celebrated for their robustness and resistance to corrosion, making them indispensable in medical equipment and food processing industries. Conversely, aluminum tubes offer the perfect balance of light weight and strength, ideal for aerospace applications where every gram counts.
Manufacturing techniques are an essential component of the tube-making process that speaks volumes about a manufacturer's expertise and authority in the field. Advanced methods, such as seamless tubing and welding, cater to diverse structural requirements. Seamless tubes, renowned for their uniformity and strength, are often preferred in situations where pressure is a critical factor, such as in hydraulic systems. The welding process, although less expensive, is perfect for general structural projects, illustrating a mix of trustworthiness and practicality grounded in professional knowledge.
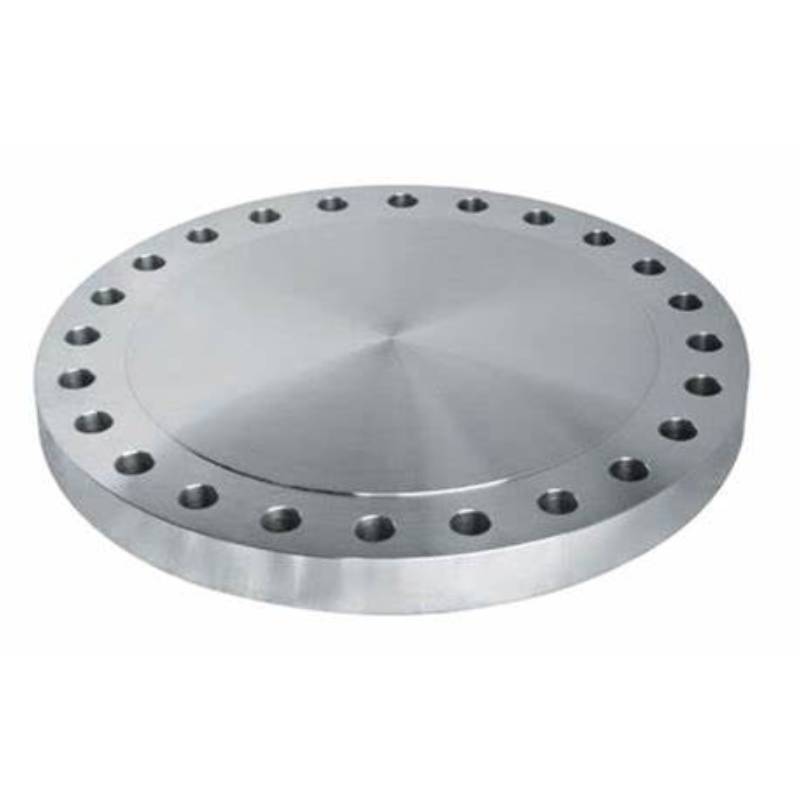
Application versatility is integral, showcasing the true breadth of metal tube usage. Understanding market demands and innovations, these tubes facilitate everything from high-stakes construction feats to intricate musical instruments. The automotive industry, for instance, leverages metal tubes for fuel lines and exhaust systems, whereas the electronics industry uses them in fabricating durable yet lightweight components.
metal tube
Invaluable experience in the metal tubing market is marked by the ability to customize. Tailoring dimensions and finishes to meet client specifications demonstrates a commitment to excellence. Custom finishes, such as powder coating or anodizing, not only enhance aesthetic appeal but also amplify the material's defensive properties against environmental stressors. Such attention to detail fosters client trust and solidifies a brand's authoritative voice in a competitive landscape.
Trustworthiness is cultivated through compliance with international standards and certifications. Adherence to ISO and ASTM standards assures clients of a high caliber product that meets global safety and reliability benchmarks. This framework not only establishes a product’s credibility but matches the global recognition necessary for widespread industry acceptance.
As businesses endeavor to harness the full potential of metal tubes, the significance of a reliable partner in production and supply chains cannot be overstated. Collaborating with a seasoned, reputable manufacturer ensures access to cutting-edge technology and insights into industry trends—key elements that sustain innovation and guarantee satisfaction.
In conclusion, the narrative of metal tubes is one woven from threads of expertise, authority, and trust. Through deliberate material selection, adept manufacturing processes, extensive application potential, and unwavering dedication to quality, the metal tube industry continues to defy limitations, creating possibilities as diverse as the industries it serves. Leveraging these insights ensures a product that is as unique and dynamic as the demand it fulfills.