Pipeline welding is a critical component in the construction and maintenance of pipelines responsible for transporting essential resources like water, gas, and oil.
Understanding the various types of pipeline welding is crucial for ensuring both the durability and integrity of these systems. This article focuses on providing a comprehensive explanation of the predominant welding methods used in pipeline construction, while emphasizing experience, expertise, authoritativeness, and trustworthiness.
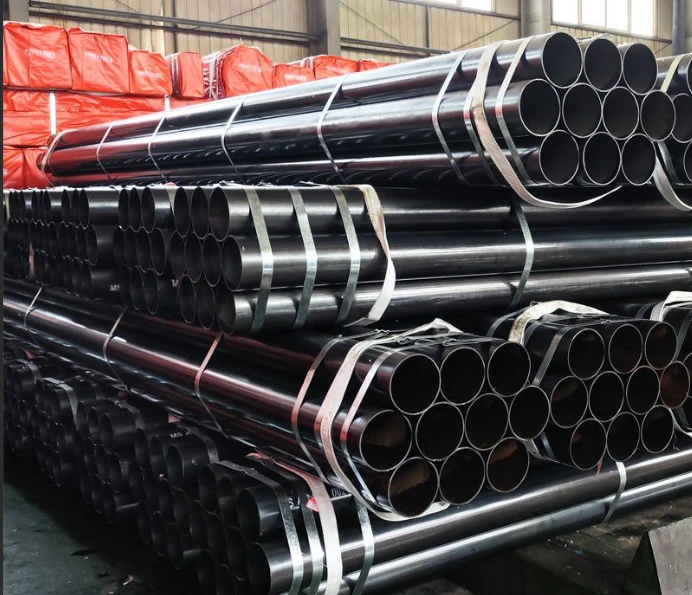
Shielded Metal Arc Welding (SMAW), often referred to as stick welding, is one of the most traditional forms of welding used in pipeline construction. Its popularity stems from its versatility and the minimal equipment required, making it ideal for fieldwork. In SMAW, the welder uses a consumable electrode coated in flux to lay the weld. The arc’s heat melts both the electrode and the pipe’s edge, resulting in a cohesive weld. Experienced welders commonly favor SMAW for its adaptability to various environmental conditions, such as wind and rain, keeping projects on schedule regardless of weather.
Gas Metal Arc Welding (GMAW), also known as MIG welding, offers a more refined alternative to SMAW. This method employs a continuously fed wire and shielding gas, yielding a cleaner and more controlled weld. It’s particularly advantageous in controlled environments, such as workshops, where conditions allow for precision. The expertise required to execute GMAW proficiently ensures a smooth and aesthetically pleasing weld, which is crucial in visible piping applications and urban infrastructures where both appearance and performance are paramount. However, its dependency on a shielding gas makes it less suited for outdoor environments where wind could disperse the gas.
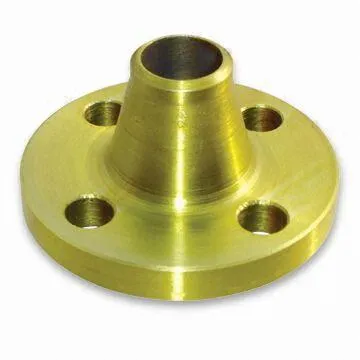
Tungsten Inert Gas (TIG) welding sets the standard for the highest precision in pipeline welding. Using a non-consumable tungsten electrode, TIG welding yields unparalleled detail-oriented performance. This method is often employed where the highest quality welds are necessary, such as high-pressure pipelines or those carrying hazardous materials. The ability to weld thin materials with low distortion makes TIG welding ideal for custom pipeline manufacturing, demonstrating both authoritative expertise and trustworthiness in delivering safety-critical infrastructures.
pipeline welding types
Flux-Cored Arc Welding (FCAW) shares similarities with GMAW but offers increased flexibility thanks to its flux-filled tubular wire. This feature allows it to be used efficiently in outdoor settings without the need for external shielding gas, making it a preferred method for pipeline projects subject to variable weather conditions. Its efficiency and adaptability make it a staple method in the industry, especially for projects requiring high productivity rates.
Additional methods include Submerged Arc Welding (SAW), which is renowned for its high deposition rates. SAW typically requires mechanized or automated setups, making it less common in some field operations but invaluable for long, linear welds in large-diameter pipelines. The method guarantees deep penetration and strong weld integrity, crucial for maintaining pressurized pipeline systems across vast distances.
Each welding type holds its place in pipeline construction through a balance of experience, pragmatism, and technical prowess. Pipelines are integral to daily life, underscoring the need for competent, reliable, and innovative welding practices. Mastering these various techniques ensures that pipelines remain safe, effective, and efficient, reflecting the dedication of skilled professionals committed to advancing industry standards through continual learning and application.
Investing in comprehensive training and certification for each of these welding methodologies encourages a workforce capable of adapting to a variety of challenges. The ongoing evolution within the field underscores the importance of expertise in new welding technologies and materials, pivotal for pushing the boundaries of pipeline capabilities and ensuring the reliability of vital infrastructure on an international scale.