Welded pipes are an essential component in a myriad of industries, from construction and architecture to oil and gas transportation. Understanding the various types of welded pipes can significantly influence the efficiency and reliability of industrial projects. Here, we delve into the different kinds of welded pipes, emphasizing their applications, benefits, and key considerations.
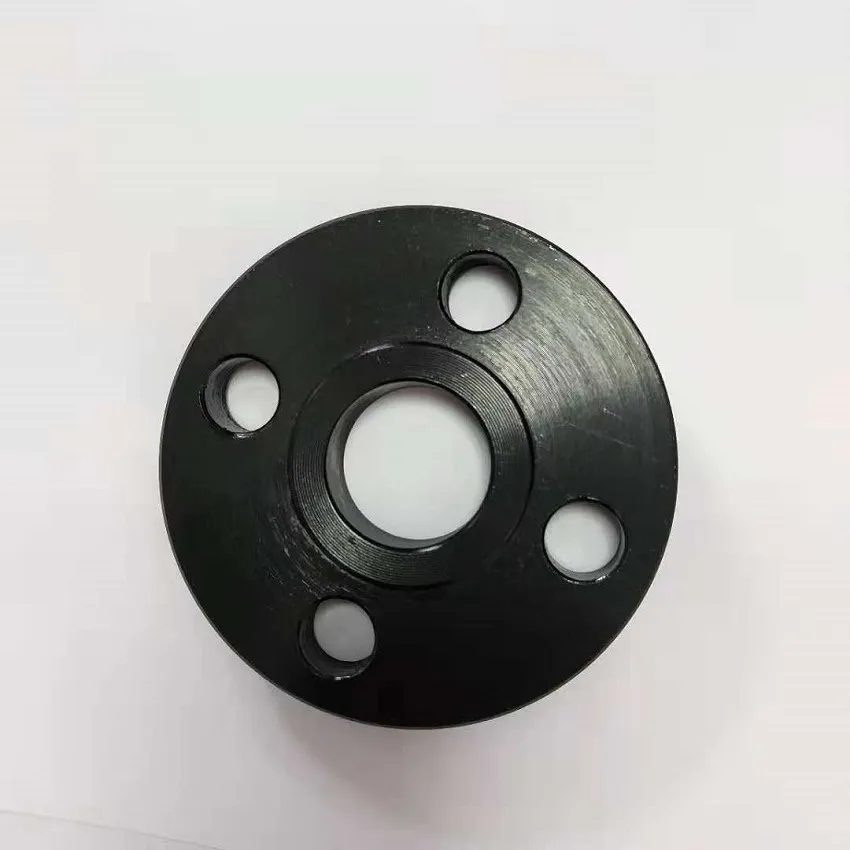
1. Electric Resistance Welded (ERW) Pipes
ERW pipes are one of the most popular types of welded pipes, commonly used for transporting oil, gas, and water. The process involves rolling metal and then welding it longitudinally down its length. ERW pipes are noted for their smooth finish and reliable quality, owing to the high-frequency electric resistance used to weld the seam.
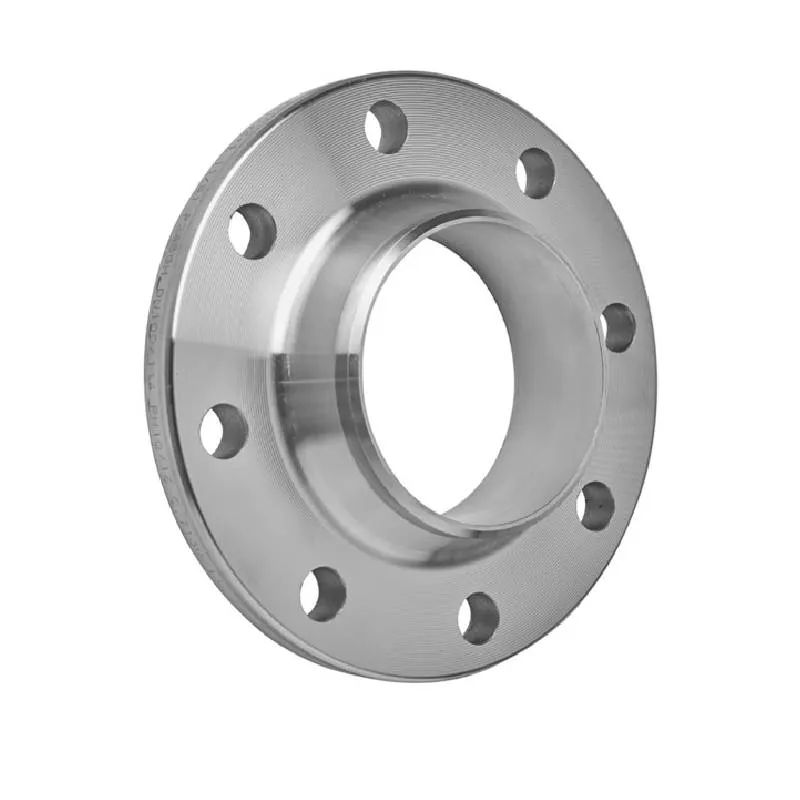
*Applications and Benefits*
ERW pipes are extensively used in fields such as fencing, scaffolding, line pipes, and water and gas transportation. Their major advantage is consistency in the thickness of the wall, offering an excellent flow characteristic for liquids and gases. Furthermore, the process ensures a low-cost production, making ERW pipes a cost-effective choice for joint ventures.
2. Longitudinal Submerged Arc Welding (LSAW) Pipes
LSAW pipes are known for their high-strength and ability to support extreme structural loads. The process involves bending and cutting the steel plates into a cylindrical shape and welding them longitudinally through a submerged arc welding method. This helps in achieving a stronger fusion.
*Applications and Benefits*
These pipes are frequently used in large-scale infrastructure projects such as bridges, high-rise buildings, and underwater piping. LSAW pipes excel in situations where superior strength is crucial. They provide a seamless appearance and are highly resistant to corrosion, withstanding harsh environmental conditions over prolonged periods.
3. Helical Submerged Arc Welding (HSAW) or Spiral Welded Pipes
HSAW pipes are fabricated by bending and welding strips of metal in a spiral pattern. This results in a stronger and more flexible pipe compared to those welded in a straight line.
*Applications and Benefits*
These pipes are particularly advantageous for water and petroleum pipeline systems due to their excellent hydraulic capacity. The spiral welded design distributes stress across a wider area, allowing for greater adaptability in terrains where movement or shifting may occur. Additionally, their manufacturing process allows for longer continuous lengths, reducing the cost of short pieces and connections.
4. Seamless Carbon Steel Pipe
types of welded pipes
While not a welded pipe, the seamless carbon steel pipe sector deserves mention due to its importance in high-pressure environments. These pipes are crafted without a welded seam, providing unmatched strength and durability.
*Applications and Benefits*
They are indispensable in oil and gas industries, particularly in high-pressure applications and in environments that demand robustness, like offshore operations. The absence of a seam reduces the chance of weak spots, ensuring superior strength and longevity. Moreover, these pipes are less prone to issues like corrosion and potential leaks.
5. Fusion Welded Pipe
While similar in some respects to other welded pipes, fusion welded pipes are known for the high heat techniques involved in their creation, resulting in robust joins capable of dealing with high pressure.
*Applications and Benefits*
These pipes are often found in industries requiring strong mechanical properties, such as power generation plants and chemical processing. Their ability to withstand extreme environments and pressures makes them indispensable in contexts where failure is not an option.
Key Considerations for Choosing Welded Pipes
- Material and Coating
Choose pipes made from materials that suit the liquid or gas being transported. Consider coatings that offer extra protection against environmental factors, aiding in longevity.
- Pressure Requirements
Ensure that the pipe can handle the maximum pressure exerted by the contents it will transport, especially for oil and gas industries.
- Cost Efficiency
While ERW pipes are generally cost-effective, projects requiring extra durability might benefit from investing in LSAW or seamless pipes despite higher costs.
- Environmental Impact
Consider the environmental conditions where the pipes will be laid. For harsh conditions,
options like LSAW or fusion welded pipes offer better resistance.
By understanding these types of welded pipes and their respective advantages and applications, industries can make informed decisions, ensuring efficient and long-lasting infrastructure. It’s crucial to align the choice of pipe with the project’s specific needs, considering factors like pressure, environmental conditions, and budget constraints.