Achieving a high-quality pipe to plate weld is a cornerstone in construction, oil and gas, and manufacturing industries. It is not just about joining two metal pieces; it's a testament to engineering precision, safety, and longevity of structures. Successful welds require both the art of a skilled welder and the science of metallurgical understanding.
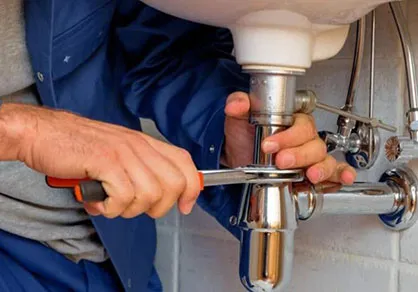
Insight into Pipe to Plate Welding
At its core, pipe to plate welding involves joining a cylindrical pipe segment to a flat plate, typically through methods like MIG, TIG, or Stick welding. The choice between these techniques depends on material types, placement conditions, and desired strength and durability of the weld. Typically, pipelines carrying high-pressure fluids or gases, or structural frameworks supporting heavy loads, mandate precision in execution.
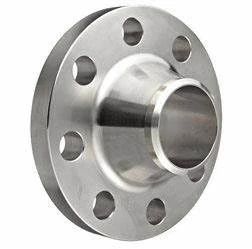
The Welding Process
The welding process commences with meticulous preparation. Cleanliness is crucial; oil, rust, moisture, or any contaminants on the welding surfaces can compromise integrity. Hence, surfaces undergo degreasing and brushing.
Aligning the pipe to the plate with precision avoids stresses once the weld cools and shrinks.
Next, the right welding technique and parameters are selected. For instance, MIG welding is often favored for its speed and efficiency, suitable for most carbon and alloy steels. TIG welding, however, provides superior control over the joining process, making it ideal for stainless steels and aluminum where oxidation during welding can be an issue.
Setting the right current, voltage, and feed rate parameters is pivotal. Each material and thickness demands a specific configuration to ensure penetration without burn-through. Welders often refine these settings based on their past experience and manufacturer guidelines for the best outcomes.
Challenges and Solutions
One frequently encountered challenge is the differential thermal expansion. When a hot molten weld pool cools and solidifies, it contracts, sometimes leading to stresses or even cracks. This is mitigated by pre-heating the components and employing slow cooling techniques, especially in high carbon steels which are susceptible to thermal cracking.
Another common issue is distortion. The heat from welding causes expansion in metal, leading to misalignment or warping. Clamp fixtures and sequencing weld passes can help manage distortion. Tack welds, small welded spots before completing the seam, also offer stability during the process.
pipe to plate weld
Quality Assurance
To assure the integrity of pipe to plate welds, non-destructive testing (NDT) methods come into play. Techniques such as radiographic testing, ultrasonic testing, and magnetic particle testing are invaluable. They help detect sub-surface discontinuities that might not be visible to the naked eye. Cutting edge digital imaging and acoustic emission technologies have further enhanced the resolution and reliability of these tests.
Economic Considerations
In industries where budget constraints are as critical as safety regulations, optimizing welding costs without compromising quality is essential. Efficient work planning, material usage optimization, and embracing automated welding solutions are facets. Robotic welding stations, though requiring upfront investment, can deliver consistent, high-quality welds round the clock.
Environmental Responsibility
With growing emphasis on environmental responsibility, welding procedures are evolving. Reduction in fumes and energy consumption is now possible via advanced, eco-friendly welding technologies. Microwelding and laser welding, though still niche, are emerging as green alternatives.
Expertise and Training
Crucially, the skill and experience of the welder can greatly impact the outcome. Continuous training and certifications ensure adherence to industry standards and keep welders abreast of the latest advancements. Engineering teams must work closely with welders to devise optimal welding plans respecting material science insights and practical constraints.
Finally, fostering an environment of rigorous self-assessment and peer reviews aids in maintaining the highest standards. Welder qualification tests, performance audits, and feedback loops are fundamental tools that build trust and credibility.
In conclusion, the realm of pipe to plate welding is a sophisticated intersection of precision engineering and skilled craftsmanship. Mastery in this domain not only influences the robustness and durability of industrial structures but also uplifts safety standards and drives innovations for future-ready solutions. Investing in technology, training, and environment-friendly practices ensures sustainable and reliable welding methodologies, fostering industrial growth and environmental stewardship alike.