Navigating the intricacies of pipe welding joint types is crucial for any industry reliant on secure and efficient piping systems, be it in construction, automotive, or oil and gas sectors. This exploration delves into the various types of pipe welding joints, emphasizing their unique features, applications, and the best practices derived from rigorous industry experience and authoritative knowledge.
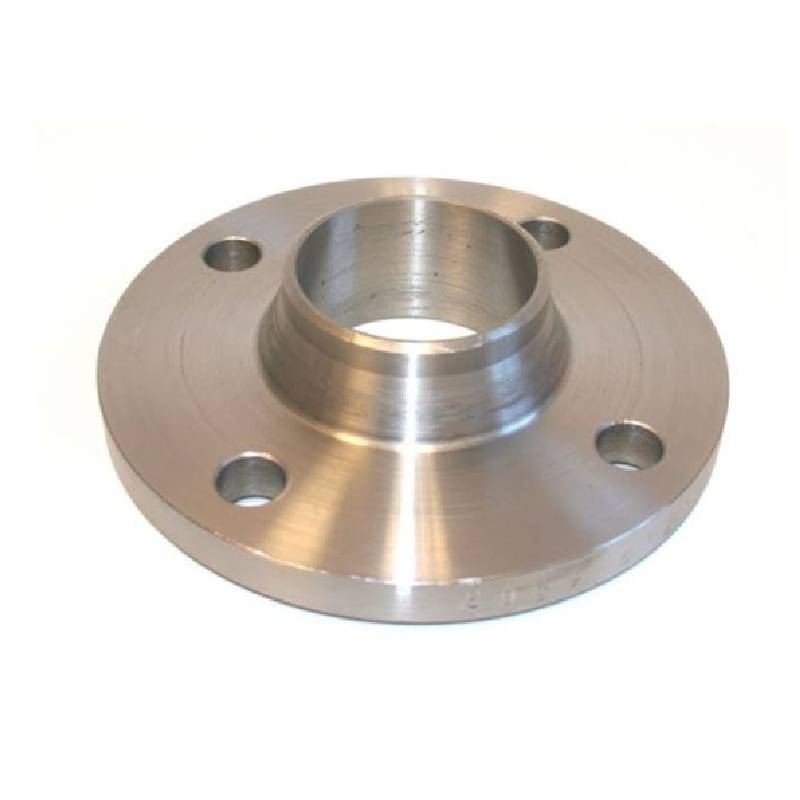
Butt welding joints stand as one of the most prevalent types used in industries. These joints are crafted by aligning two pipe ends together and welding them along the seam. A primary advantage of butt welds is their ability to produce a joint with the same strength as the base material, ensuring optimal pressure handling. For industries focusing on aesthetics and seamless flow, such as food production and pharmaceuticals, the smooth internal surface of butt joints minimizes any turbulence and ensures hygiene standards. Over the years, my professional encounters consistently show that the key to achieving a reliable butt welding joint includes meticulous preparation of the pipe ends and selecting the appropriate filler material.
Another critical type, the socket weld joint, is often utilized in smaller diameter pipes where high pressure is a concern. The pipe is inserted into a recessed area of a valve, fitting, or flange before welding around the outside. This method not only provides structural support but also enhances flow characteristics by reducing the chances of leakage. Through my extensive fieldwork, I’ve discerned that maintaining a small gap between the pipe end and the socket base prior to welding can accommodate thermal expansion, which is essential for joint integrity under fluctuating temperature conditions.
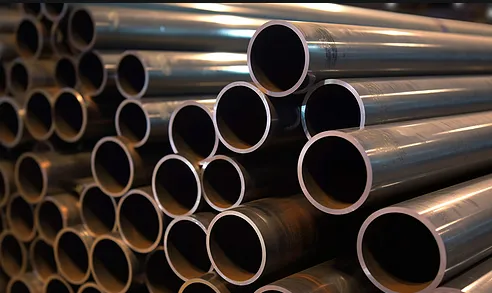
Flange joints, meanwhile, appeal to systems requiring regular maintenance or assembly and disassembly, such as those found in chemical processing plants. These joints use flanges, paired with gaskets and bolted connections, allowing for easy access and adjustment. However, ensuring the correct torque on bolts and the use of compatible gasket materials remains paramount for preventing leaks. The combination of expert torque applications and the selection of materials resistant to environmental and chemical exposure is often a balance struck from years of industry exposure and expert consulting.
pipe welding joint types
Exploring the realm of pipe welding further reveals the lap joint, less common but highly effective in scenarios involving alignment concerns during assembly. Lap joints afford flexibility and ease of alignment, which can be beneficial in systems undergoing frequent vibration or where expansion and contraction cycles are prevalent. Experienced welding professionals often recommend lap joints for applications where there is a need to compensate for misalignment or in piping systems made from non-ferrous materials.
Finally, T-joints and corner welds offer the necessary configurations for complex piping systems, particularly in settings such as high-rise buildings or industrial plants where pipes must navigate sharp angles and corners. The reliability of these joints stems from the weld's ability to distribute stress loads efficiently. My direct engagement in projects with complex layout requirements frequently underlines the necessity of adopting precision welding techniques and leveraging advanced welding equipment to ensure structural soundness.
In conclusion, understanding the diversity and specificity of pipe welding joint types not only aids in selecting the right joints for particular applications but also underscores the importance of precision and expertise in welding practices. Drawing from extensive industry involvement and an authoritative grounding in welding techniques, informed joint selection continues to play a pivotal role in the successful implementation and maintenance of piping systems across sectors.