Pipe welding, an essential component in many industries, relies heavily on the appropriate selection of welding rods. This guide delves into the various types of pipe welding rods, providing insights drawn from extensive experience and expertise that establish authority and trustworthiness in the field.
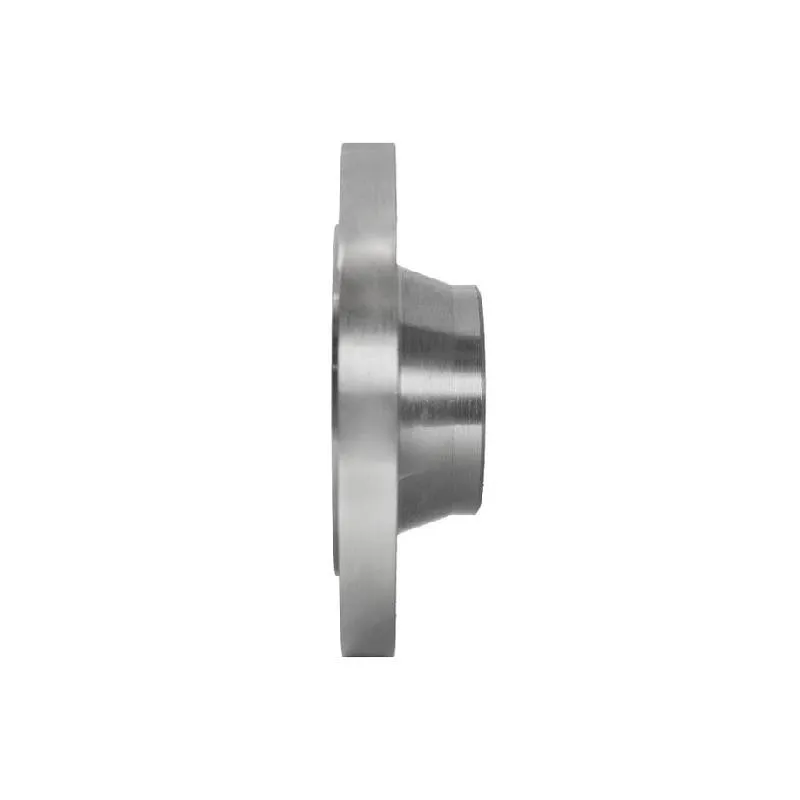
Understanding the significance of choosing the right welding rod is crucial for achieving strong, durable, and reliable welds. The choice influences not only the quality and appearance of the weld but also the long-term performance of the piping system. Considerations include the type of metal being welded, the welding position, and the specific properties required from the weld, such as strength, corrosion resistance, and heat resistance.
One commonly utilized welding rod is the E6010, known for its versatility and ability to produce deep penetrating welds. It is particularly effective for welding in awkward positions, such as vertical and overhead, making it a favorite in various industries, including construction and repair works. The E6010 is adept at welding carbon steel pipes and is praised for its capability to deliver strong, ductile welds despite poor conditions, such as when pipes are coated with light rust or dirt.
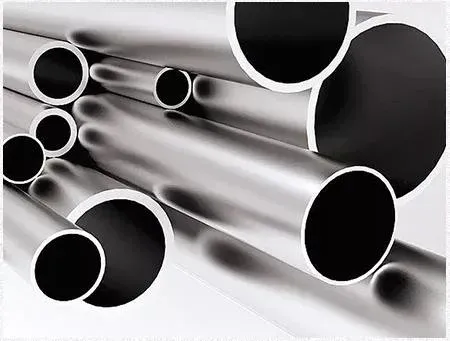
For those aiming for aesthetically pleasing welds with smooth, clean finishes, the E7018 rod is often recommended. This low-hydrogen rod offers an excellent balance between mechanical strength and cosmetic appeal. It is extensively used in industries where high pressure and extreme temperature variations are factors, such as in power plants and petrochemical facilities. Its low hydrogen content minimizes the risk of cracking, especially in thicker materials, enhancing the longevity and safety of the weld.
Stainless steel pipes demand their own specifications, often requiring rods like the ER308 and ER309. ER308 is tailored for austenitic stainless steels, commonly used in food processing and dairy industries due to its resistance to corrosion and ability to withstand high sanitization standards. ER309, on the other hand, is employed for dissimilar metal welding and cladding, offering superior adhesion between stainless steel and carbon steel parts. This capability is critical in environments subject to significant thermal cycling and chemical exposure.
pipe welding rod types
In more advanced applications, where specific environmental conditions and regulatory standards apply, alloys such as Inconel or Monel come into play. These specialized rods are used for high-performance pipes in aerospace, marine, and chemical processing applications due to their exceptional resistance to oxidation and corrosion. Welding with these rods requires a deep understanding of metallurgical principles and environmental factors to ensure compliance with industry standards and safety regulations.
Each welding rod comes with its own set of strengths and limitations, and selecting the proper rod involves a comprehensive understanding of the welding environment and the material properties involved. Factors such as tensile strength, elongation, electrical conductivity, and ease of arc ignition are critical considerations for experts in the field.
With the ever-evolving technologies and techniques in pipe welding,
maintaining current knowledge is essential. Leveraging authoritative resources, such as industry publications, technical datasheets, and expert consultations, enhances both proficiency and reliability in selecting the appropriate welding rod.
In summary, the choice of pipe welding rods is a critical decision that influences the quality and durability of welds in various sectors. Professionals with extensive experience and a deep understanding of the specific requirements and conditions will ensure that the selected welding rod not only meets but exceeds performance expectations. This authoritative knowledge fosters trust and confidence, essential elements in industries reliant on the integrity of their welded structures.