In the world of piping solutions,
seamless pipes are a pivotal component for various industrial applications. Their strength, durability, and adaptability make them a popular choice in sectors ranging from petrochemicals to construction. For those seeking to navigate the complex landscape of seamless pipe dimensions, a clear understanding of their specifications can simplify the selection process and ensure optimal performance in any project.
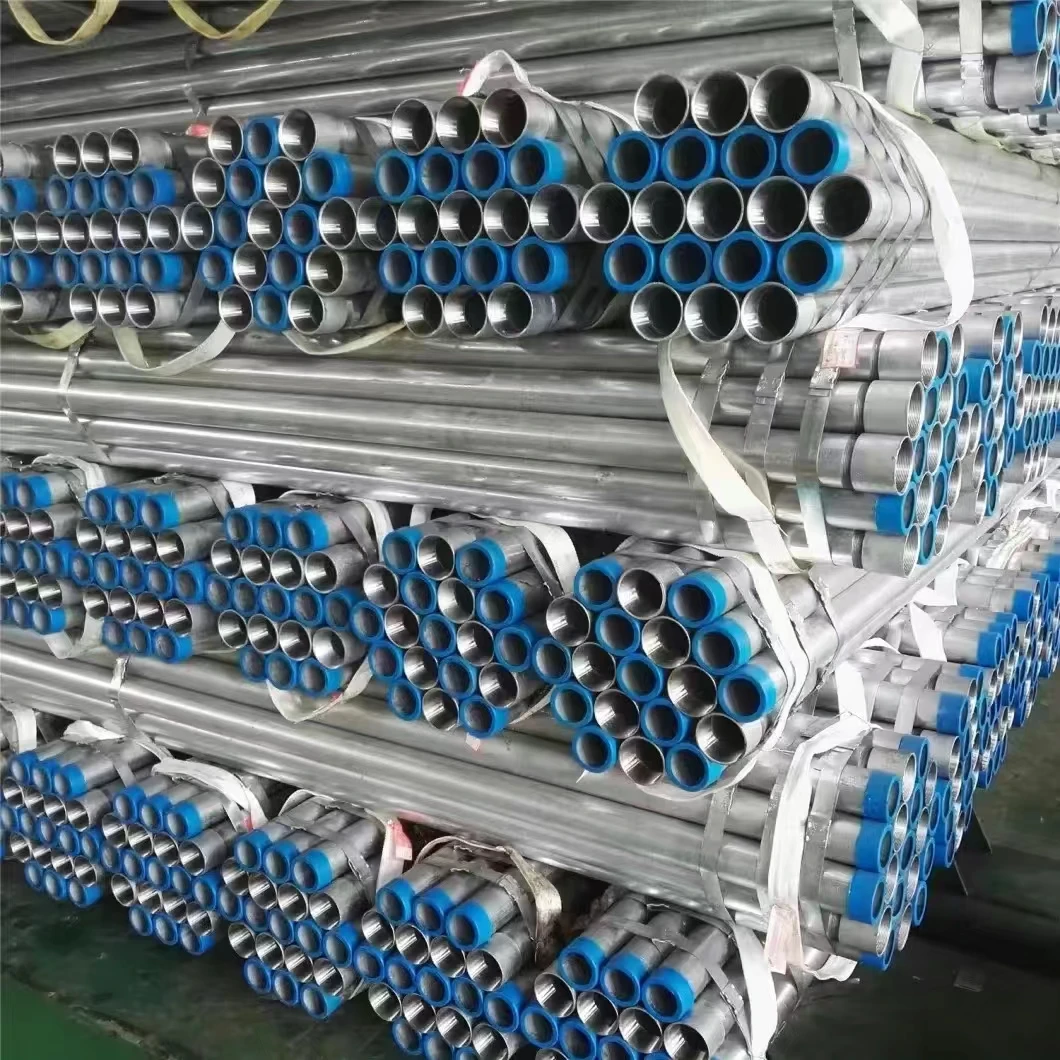
Seamless pipes, unlike welded ones, are manufactured without any seams, providing enhanced structural integrity. This characteristic is crucial when dealing with high pressure, high temperature, and corrosive environments. The absence of seams also reduces the likelihood of the pipe failing along a weld, thus ensuring reliability in critical applications.
Industries rely on specific standards to classify the dimensions of seamless pipes. Standards such as ASTM, ASME, and API delineate the measurements, categorizing them by outer diameter (OD), wall thickness, and length. These metrics are vital in determining the pipe's suitability for specific functions. For example, a thick-walled seamless pipe is preferable in high-pressure situations, as it can withstand more stress without deforming.
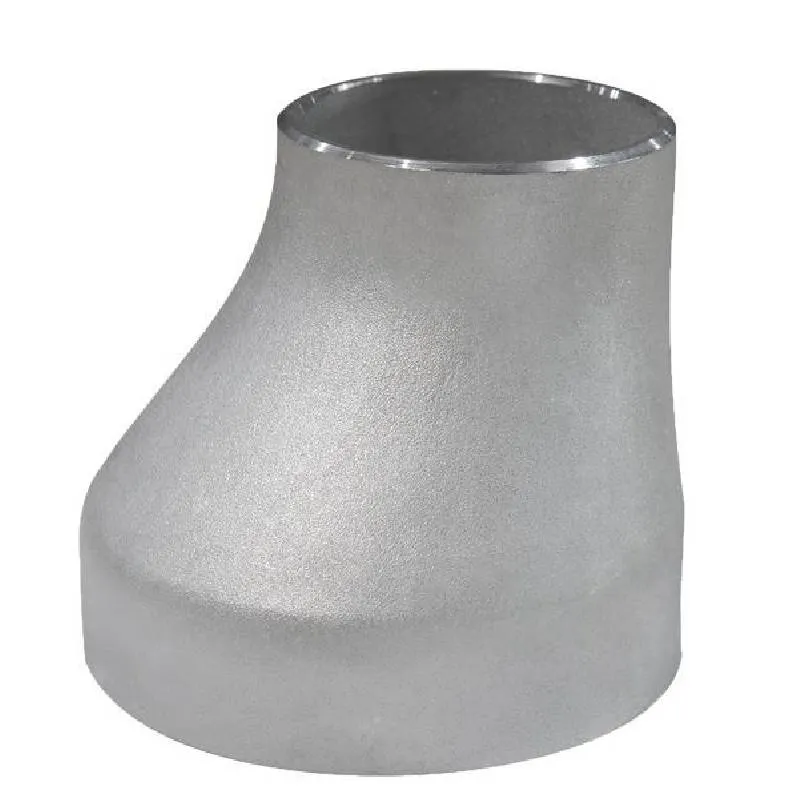
The outer diameter is often the first specification to consider. It can range from as small as a quarter of an inch to several feet, catering to varying industry requirements. The choice of diameter directly impacts fluid flow rates and pressure levels within the pipe, making it a critical factor in pipe selection. Projects that require rapid transportation of gases or liquids at high velocities typically necessitate larger diameters.
Wall thickness is another essential parameter to consider. It plays a significant role in the pipe's ability to resist pressure. Known as the schedule in industry parlance, wall thickness influences not only the pipe's strength but also its weight, cost, and insulation properties. Thicker walls are ideal for high-pressure applications, whereas thinner walls might be selected for lower pressure systems or where weight is a concern.
ss seamless pipe dimensions
Length specifications are also important, with seamless pipes available in fixed or random lengths. This flexibility allows manufacturers and engineers to tailor their order to the specific requirements of their projects, reducing waste and unnecessary expenditure. Seamless pipes can be precision cut to meet the exact length needed for any installation, offering additional customization for unique project needs.
While understanding these dimensions is critical, consulting with a knowledgeable supplier or industry expert can improve decision-making. These professionals can provide insights into the latest advancements in seamless pipe manufacturing, including material innovations that enhance performance, such as corrosion-resistant alloys or double-layered structures.
Equally crucial is selecting a reliable and experienced manufacturer. Trusted brands adhere strictly to international standards and offer warranties that underline their confidence in their product's reliability. These guarantees can be particularly important in sectors like oil and gas or pharmaceuticals, where seamless pipe failure could have serious implications.
In conclusion, while seamless pipe dimensions can initially seem daunting, a clear understanding of their different aspects can significantly inform and enhance the selection process. Reliance on industry standards and expert advice ensures that the chosen pipes not only meet but often exceed operational expectations, providing safety, efficiency, and cost-effectiveness in all their applications. Armed with this knowledge, industries can confidently procure the right seamless products to suit their specific operational demands, ensuring longevity and success in their projects.