Steel welded pipes have emerged as a cornerstone in various industries, owing to their versatility, resilience, and cost-effectiveness. Their applications span from construction and infrastructure to automotive and oil and gas industries, proving them indispensable for modern engineering solutions.
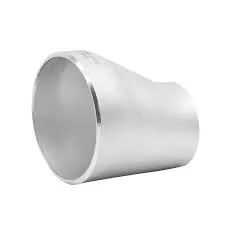
A defining feature of steel welded pipes is their method of production. Unlike seamless pipes, which are manufactured through a process of extrusion, welded pipes are made by forming flat steel sheets or plates into a pipe shape and welding the seam. This welding technique provides more control over pipe specifications, allowing for precise sizing, which plays a significant role in meeting specific project requirements.
Experience in the field of welded pipes highlights their outstanding adaptability to different industrial needs. In construction, for instance, these pipes are praised for their robustness and corrosion resistance, essential properties for structural stability and longevity. During a recent project focusing on a metropolitan subway system, the choice of steel welded pipes was dictated by their ability to withstand both external and internal pressures, crucial for underground installations subject to constant stress and environmental factors.
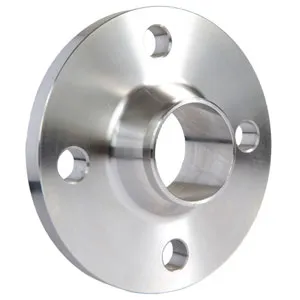
The expertise behind steel welded pipes involves a deep understanding of metallurgical properties and welding techniques. The HF-ERW (High-Frequency Electric Resistance Welding) method is commonly applied. This technique ensures a smoother finish and a more uniform grain structure, contributing to the pipe’s durability and leak-proof nature. Metallurgists and engineers constantly enhance these processes to meet evolving industry standards such as ASTM or ASME, ensuring that the final products adhere to rigorous quality and safety measures.
steel welded pipe
Steel welded pipes also reflect a level of authoritativeness in standardization and industry regulation. Manufacturers commonly align their production processes with international standards like API (American Petroleum Institute) or ISO (International Organization for Standardization) to guarantee that the pipes will integrate seamlessly into global infrastructure projects. Such adherence not only reinforces trust in the product but also certifies their usage in critical safety environments, from skyscraper builds to chemical transportation.
Trustworthiness in steel welded pipes stems from rigorous testing and quality assurance practices. Many manufacturers conduct ultrasonic testing, radiography, and hydrostatic testing to ensure no defects in the weld or the steel. These tests are pivotal in establishing a pipe's integrity, particularly when used in high-pressure applications. A particular case involved a leading oil company that utilized these pipes, relying heavily on their ability to transport volatile substances safely across large distances, thereby preventing environmental hazards and maintaining operational efficiency.
Moreover, technological advancements and smart systems for quality control are continually enhancing the trustworthiness of these pipes. The integration of IoT (Internet of Things) technology has allowed real-time monitoring of pipe health, predicting maintenance needs before issues arise, further cementing their role in safety-critical operations.
In conclusion, the realm of steel welded pipes is marked by their indispensable role across industries, characterized by expert manufacturing techniques and rigorous quality standards. The experience drawn from various applications underscores their reliability and effectiveness, while ongoing advancements in production and monitoring technologies continue to enhance their performance. For industries seeking a tried-and-true solution that balances strength, versatility, and cost, steel welded pipes stand as a commendable choice, fully meeting the stringent requirements expected in today's demanding applications.