Understanding the various types of welding in piping is crucial for ensuring the integrity, reliability, and efficiency of piping systems across industries. This knowledge not only aids in selecting the appropriate welding technique but also enhances safety standards, improves durability, and reduces maintenance costs. Drawing upon extensive expertise and industry authority,
this article delves into the common yet indispensable welding techniques in piping.
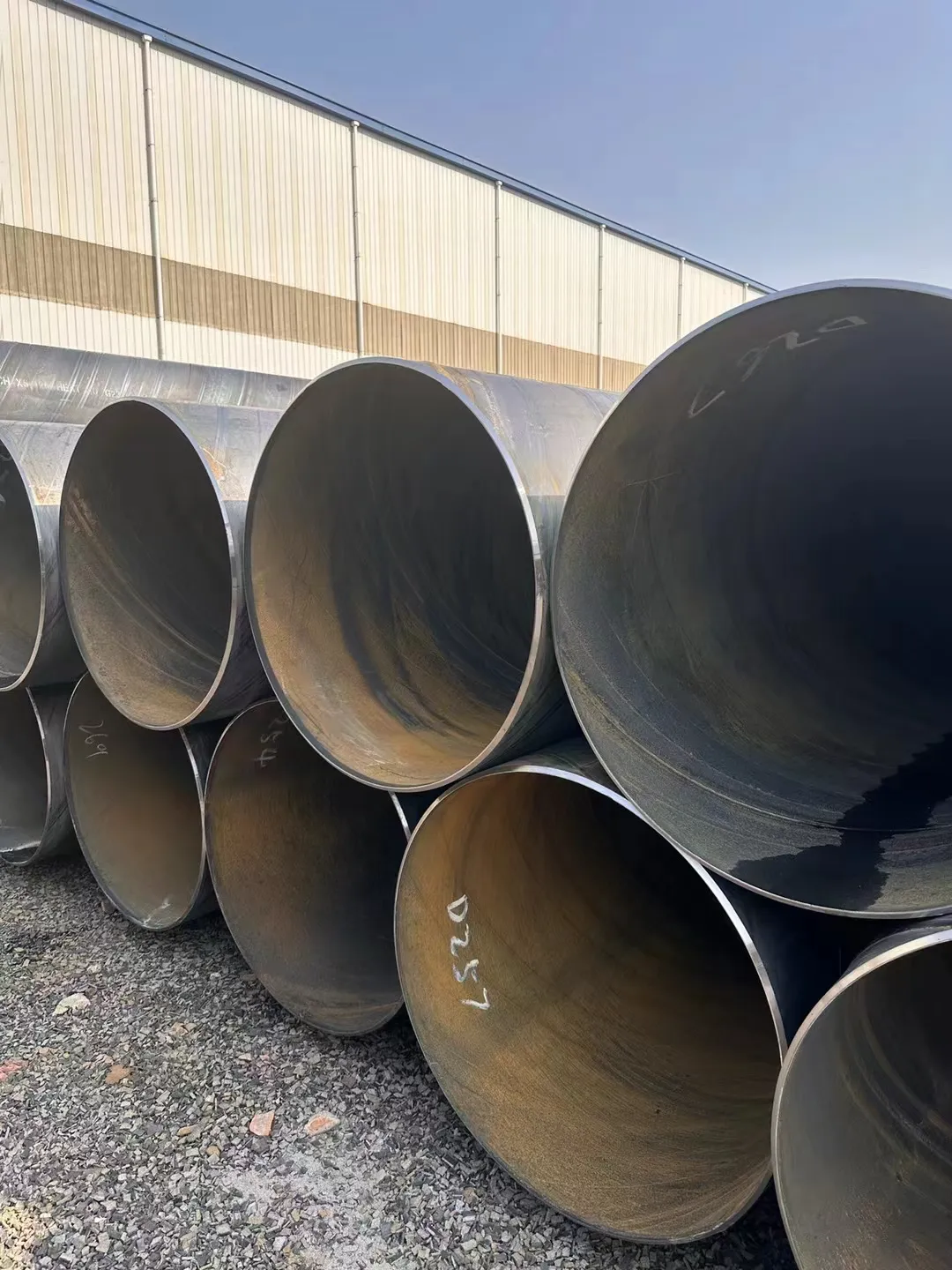
Shielded Metal Arc Welding (SMAW), also recognized as stick welding, is one of the most traditional and widely-used techniques in welding piping systems. This process involves a consumable electrode covered with a flux to lay the weld. The flux coating disintegrates during the welding process, releasing vapors that act as a shielding gas and providing a protective slag. Known for its versatility and simplicity, SMAW is suitable for a wide range of materials and is particularly effective for welding thicker materials. Moreover, its portability does not require complex equipment, making it a favorite in repair and fieldwork.
Gas Tungsten Arc Welding (GTAW), often referred to as TIG welding, leverages a non-consumable tungsten electrode to produce the weld. The process requires an inert gas shield, usually argon or helium, to protect the welding area from atmospheric contamination. TIG welding is renowned for its precision and the high-quality weld it produces, making it ideal for thin-walled pipes and welding non-ferrous metals such as aluminum and magnesium. The highly skilled nature of this process demands a welder with significant expertise and is vital in applications where appearance and weld integrity are of utmost importance.
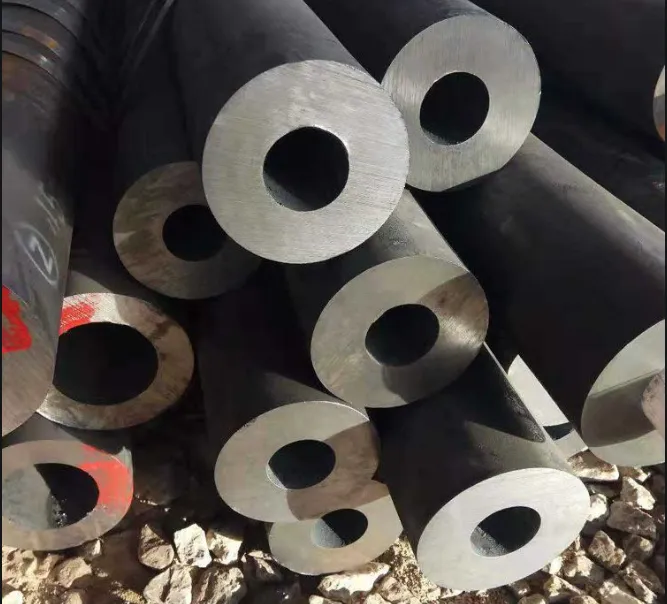
Gas Metal Arc Welding (GMAW) or MIG welding uses a continuous feeding wire that acts as both the electrode and the filler material. A shielding gas, typically a mix of argon and carbon dioxide or pure CO2, is used to protect the weld zone. This method offers high deposition rates and is easier to learn, making it a popular choice in industries where speed and efficiency are critical. Though primarily used for thicker materials in piping, advances in equipment and techniques are expanding its application to thinner materials as well.
types of welding in piping
Flux-Cored Arc Welding (FCAW) bears similarity to MIG welding but utilizes a wire with a core of flux. The process can be either self-shielded or dual-shielded with additional gas. FCAW stands out for its high welding speed and portability, making it advantageous for heavy-duty work and outdoor operations where external environmental conditions can influence gas flow from conventional methods. It is particularly beneficial in industries like construction and shipbuilding, where thicker, heavy-duty materials are common.
Submerged Arc Welding (SAW) is distinctive as it involves the formation of an arc beneath a bed of granulated material. The protective flux blanket facilitates a high deposition rate, with the additional benefit of deep penetration welds. This method is mainly used in large-diameter piping and pressure vessel constructions due to its exemplary efficiency and strength. However, its limitation to flat or horizontal position makes its application somewhat constrained.
Each welding technique has its own set of advantages, tailored to specific pipe materials, positions, and industrial requirements. While advancements in welding technology continue to emerge, the foundation built by these methods remains. Through the lens of experience, expertise, authority, and trustworthiness, the decision on which welding type to employ should incorporate a comprehensive understanding of the specific material characteristics, environmental conditions, and desired outcome of the piping system application.
Ultimately, selecting the correct type of welding is pivotal in realizing the full potential of a piping system, ensuring superior performance and extending the lifecycle of the welded components. As technologies evolve, integrating innovative tools and practices with these traditional methods will continue to meet the diverse and demanding needs of modern industries.