Underground pipe welding is a critical component of modern infrastructure, playing an essential role in various industries including oil and gas, water supply, and sewage systems. The techniques and technologies used in underground pipe welding have evolved significantly, offering increased efficiency and reliability. This article delves into the cutting-edge practices, challenges, and innovations in underground pipe welding, providing expert insights grounded in real-world experience.
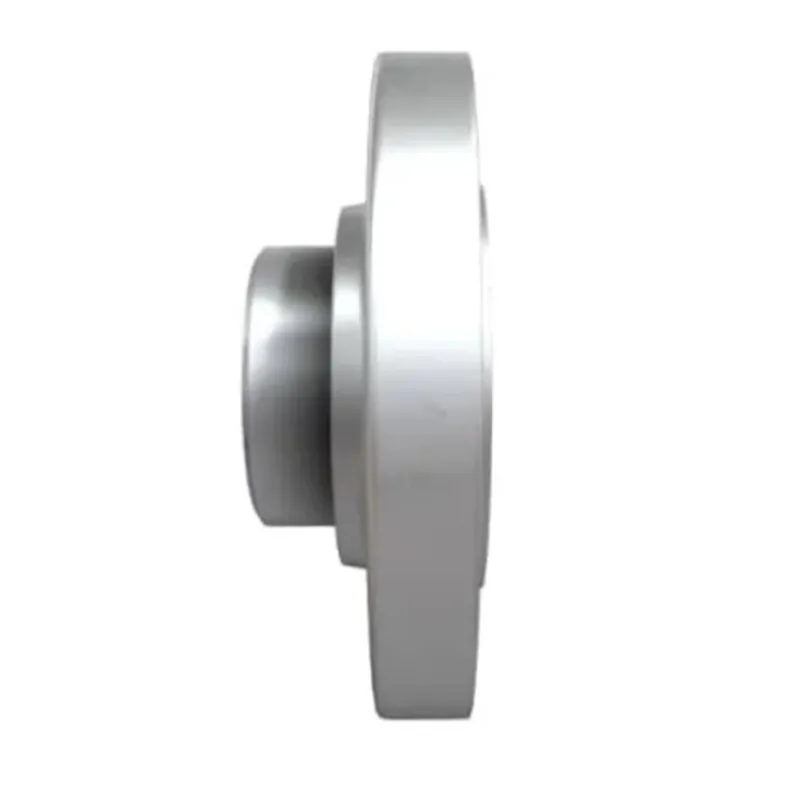
At the core of successful underground pipe welding is a thorough understanding of the environmental conditions and material requirements. Underground environments present unique challenges, such as restricted access, varying soil compositions, and potential exposure to corrosive elements. As a result,
welders must meticulously assess these factors before initiating the welding process. Welding operations in such environments often require specialized equipment designed to operate effectively under these constraints. For instance, advances in automatic and semi-automatic welding technologies have enhanced the ability to achieve precise and high-quality welds in challenging underground settings.
Expertise also dictates the choice of materials and welding techniques tailored to specific project demands. For example, choosing between materials like polyethylene, PVC, or steel depends on the pipeline's intended use, pressure levels, and environmental conditions. Each material has its own set of welding methods; fusion welding is typically used for polyethylene and PVC pipes, whereas steel pipes often require arc welding techniques like TIG or MIG welding. Expert welders not only possess the technical skills for these diverse procedures but also continuously update their knowledge to stay abreast of new materials and methods.
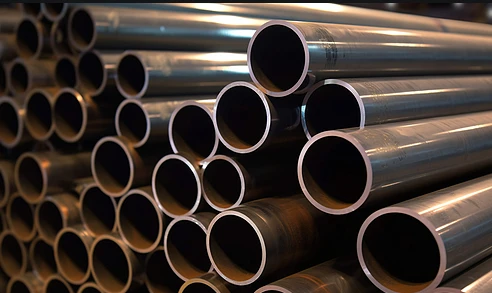
One of the groundbreaking innovations in this field is the integration of real-time monitoring technology. Using sensors and IoT devices, welding operations can achieve unprecedented levels of precision and safety. These devices monitor key parameters such as temperature and pressure during the welding process, ensuring compliance with safety standards and optimal performance. The data collected also allows for predictive maintenance and rapid detection of potential faults, which reduces downtime and enhances the longevity of the pipelines.
Safety is paramount in underground pipe welding. Authoritative bodies, including the American Welding Society (AWS) and similar organizations worldwide, set rigorous safety standards and certifications for welders. Adherence to these standards is not just about legal compliance; it builds trust with clients and stakeholders. Certified welders are equipped with the knowledge to implement best practices that prevent accidents such as gas explosions or leaks, protecting both personnel and the environment.
underground pipe welding
The development of training programs and certifications further underlines the importance of expertise and trust in underground pipe welding. Programs that combine theoretical knowledge with practical experience ensure that welders are thoroughly prepared for the complexities of underground work. Advanced simulation tools and virtual reality training modules are increasingly popular, providing immersive learning environments that replicate real-world scenarios.
Moreover, collaboration between welding professionals, engineers, and environmental scientists is vital for ensuring the success of underground pipe installations. This interdisciplinary approach fosters a comprehensive understanding of the project landscape, enabling the development of innovative solutions that meet both engineering demands and environmental considerations. Such collaborations bolster the authority of the welding industry as a whole, pushing the boundaries of what is achievable underground.
Sustainability is another essential consideration in modern underground pipe welding. Eco-friendly practices, such as using low-emission welding technologies and biodegradable materials, are gaining traction. Welding operations are now often conducted with a keen awareness of minimizing environmental impact, ensuring that infrastructure development and environmental stewardship go hand-in-hand.
In conclusion, the field of underground pipe welding is characterized by a blend of expert knowledge, cutting-edge technology, and a commitment to safety and sustainability. Professionals in this domain continue to push the envelope, integrating innovative solutions that address both traditional and emerging challenges. Through collaboration, continuous learning, and adherence to stringent standards, the industry not only achieves project success but also establishes itself as a cornerstone of modern infrastructure development, trusted across the globe for reliability and innovation.