Welding large pipes is a highly specialized task that resides at the apex of industrial engineering, combining art and science to lay the foundation for robust infrastructures. The significance of this process in oil and gas, water transport, and large-scale construction cannot be overstated. Mastery over this process is not merely an option but a necessity for professionals aiming to maintain high standards of safety, efficiency, and durability.
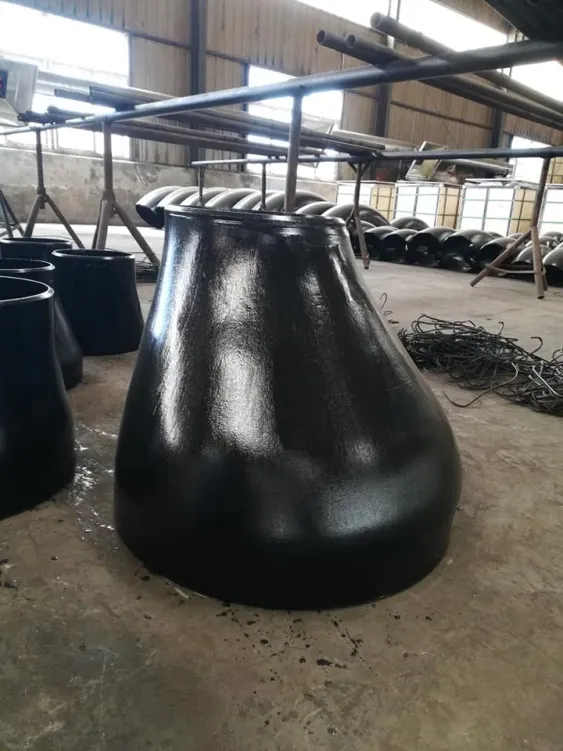
In practice, welding large pipes requires a profound understanding of various welding techniques, including but not limited to arc welding, TIG (Tungsten Inert Gas) welding, and MIG (Metal Inert Gas) welding. Each method has its own set of advantages and challenges. For instance, arc welding is renowned for its strength and reliability, which is crucial when dealing with the immense pressures associated with large pipes used in oil pipelines or undersea water lines. On the other hand, TIG welding is known for producing clean, precise welds that are essential in high-quality projects where appearance and performance are equally important.
An often-underrated aspect of pipe welding is the preparation. True expertise is reflected in meticulous preparation of the work area and materials. Cleaning the pipe surface to remove any contaminants, ensuring perfect alignment before welding, and selecting the appropriate welding rod or filler material based on pipe material are critical steps. Mistakes in this preparatory phase often lead to catastrophic failures, making experience and attention to detail indispensable traits in a skilled welder.
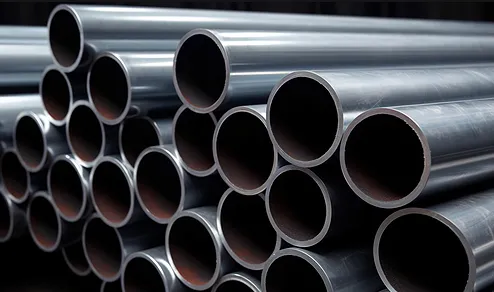
The authoritative voice in the field of welding big pipes comes from the rigorous certification and training programs that professionals undergo. Bodies like the American Welding Society (AWS) set the global standards, ensuring that certified welders are up to date with the latest safety protocols, technology, and quality control measures. Certification not only lends credibility to the welder but also assures clients of the welder’s competency and commitment to industry excellence.
welding big pipe
Trustworthiness in the welding sector is cultivated through a track record of successful projects, transparent business practices, and adherence to the highest safety standards. Building client confidence hinges on delivering consistent quality, maintaining open lines of communication, and employing cutting-edge technology. Usage of modern non-destructive testing (NDT) methods, such as ultrasonic, radiographic, and magnetic particle testing, underscores a firm's dedication to verifying the integrity of their welds without compromising the structural component.
The technological advancements in welding are reshaping the landscape with automation and robotics playing increasingly pivotal roles. Automated welding systems for large pipes ensure higher precision, reduce human error, and enhance productivity, thus aligning with the industry's demand for efficiency and reliability. However, this does not undermine the role of skilled welders; rather, it augments human expertise, allowing professionals to leverage technology to achieve unparalleled results.
In conclusion, the realm of welding big pipes goes beyond mere technical know-how; it is about continuous learning, adapting to technological advancements, and adhering to the stringent standards of safety and precision. As industries evolve, the demand for adept welders will inherently grow, highlighting the need for well-rounded professionals who possess not only the requisite technical skills but also the ability to innovate and uphold integrity in their craft. For anyone venturing into this field, embedding oneself in lifelong learning and embracing new technologies will pave the way for a successful and fulfilling career.