Selecting the right welding hose pipe can significantly influence the outcome of welding operations. The importance of a high-quality welding hose pipe is often underestimated, yet it is a critical tool in ensuring safety, efficiency, and precision in welding tasks. Within this context, it's vital to delve into the different facets of welding hose pipes, encompassing their functions, material types, maintenance practices, and safety considerations to provide a comprehensive guide.
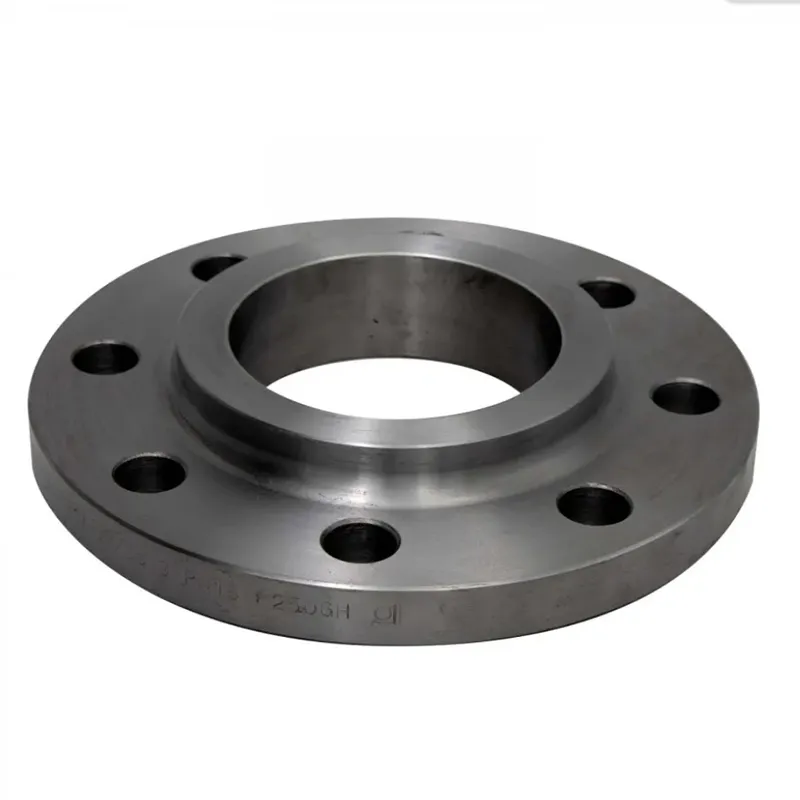
Welding hose pipes serve as conduits for transporting gases required in welding. These gases usually include oxygen, acetylene, argon, or a mixture of gases, which are essential in various welding techniques such as MIG, TIG, and oxy-fuel welding. Choosing a hose pipe that can efficiently and safely transport these gases is crucial for both the quality of the welds and the welder's safety.
One of the primary considerations in selecting a welding hose pipe is its material. Rubber hoses are popular due to their flexibility and durability. They are generally resistant to cuts, abrasions, and impact, making them suitable for rugged working environments. However, for applications requiring strong chemical resistance and higher pressure retention, thermoplastic hoses are preferable. These hoses are lightweight and can withstand higher temperatures while resisting damage from chemicals.
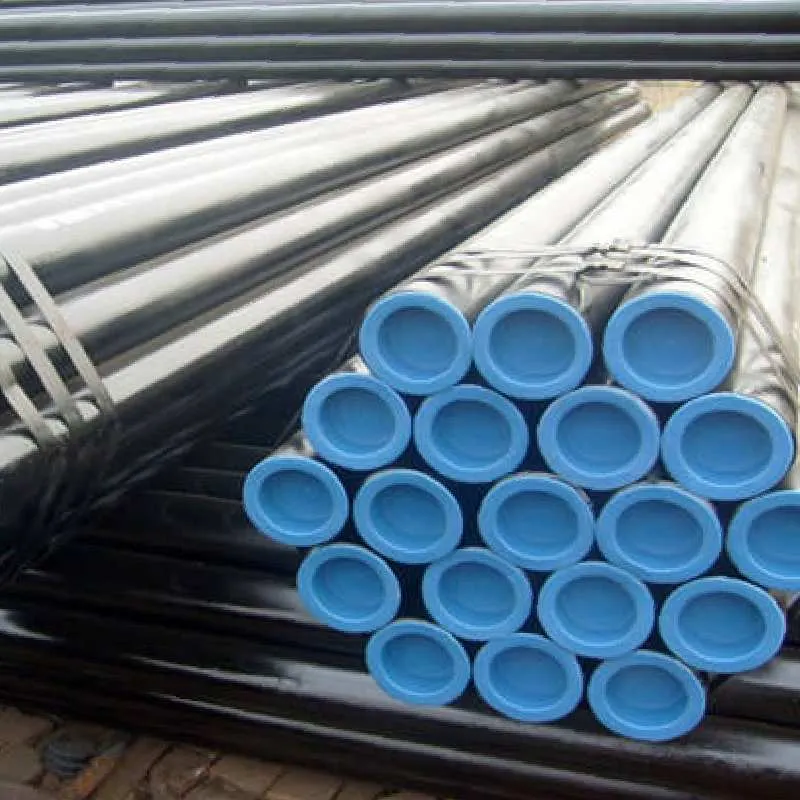
Another critical aspect is the hose's diameter and length, which should match the welding equipment's specifications. An inappropriate diameter can restrict gas flow, leading to inconsistencies in the welding process. Similarly, the hose length influences flexibility in maneuvering around the welding area. Longer hoses offer greater reach but may reduce gas pressure; therefore, balancing length with performance is essential.
It's also imperative to pay attention to the hose pipe's fittings and connections. Reliable fittings prevent gas leaks, which can lead to hazardous situations. Many hoses come equipped with brass or stainless steel fittings, which are robust and resistant to corrosion. Properly securing these fittings with appropriate clamps or crimping tools is essential for maintaining a safe and efficient welding setup.
welding hose pipe
Maintaining the integrity of a welding hose pipe entails regular inspection for signs of wear and tear, such as cracks, bulges, or leaks. Replacing compromised hoses promptly prevents potential accidents and ensures continuous operation. Furthermore, storing hose pipes in cool, dry places prolongs their lifespan, protecting them from environments that might degrade their material integrity.
Incorporating safety measures around the use of welding hose pipes cannot be understated. Regular training and awareness programs about the correct handling and storage of these hoses enhance workplace safety. Using flashback arrestors is also crucial in preventing flames or gases from traveling back through the hose, which could ignite and cause explosions.
Authoritative industry bodies, such as the American Welding Society (AWS) and Occupational Safety and Health Administration (OSHA), provide directives and standards that should guide the usage and management of welding hose pipes. Adhering to these standards not only ensures safety and quality but also enhances the credibility of welding operations.
Finally, trusting well-known and reputable brands when purchasing welding hose pipes can alleviate concerns regarding quality and performance. Brands that comply with international safety and quality standards often ensure their products undergo rigorous testing, hence offering more reliable products.
In conclusion, welding hose pipes are more than just simple conduits for gases; they are critical components that impact the safety, efficiency, and effectiveness of welding tasks. By understanding and implementing the right choice of materials, sizes, fittings, and maintenance routines, one can significantly enhance their welding operations, ensuring a product that meets professional standards of precision and safety. This comprehensive approach fosters an environment of trust, expertise, and authority, crucial metrics not just for optimal welding performance but also for building a reputable presence in the competitive welding industry.